Some of you may remember a few years ago when I mounted the drum from my lawn roller onto the back of a Ridemaster tractor. The roller set up this way was much more practical to use with me riding on it than it was when being pulled behind the R/T tractor. It was easier to move around things like trees and a lot easier when backing up. I really liked the function of the design.
However .. there was one drawback. The Ridemaster just didn't have enough horsepower.
The roller is 5 foot long and 2 foot diameter and weighs around 970 pounds when full of water. The Ridemaster would move it alright on level ground but could hardly make it up any incline at all.
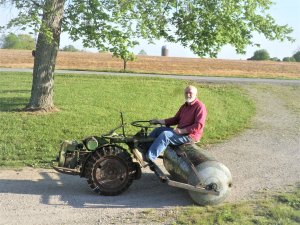
I went ahead and used the powered roller to pack down the gravel that I had put down in front of the garage, then I removed the roller drum from the Ridemaster and mounted the hitch back on it so it could be pulled behind the tractor again.
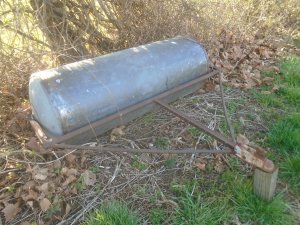
After using it as a pull behind roller again for awhile, I decided that I really liked it better when it was self powered.
Of course I could put it back on the Ridemaster and then put a bigger engine on it too but that would rune a restorable Ridemaster that is complete.
So I looked thru my stuff to see what I could use to power the roller.
I have this 18 HP B&S twin cylinder engine that should give it enough horsepower.
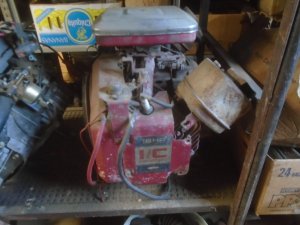
And this hydrostatic drive pump for forward and reverse.
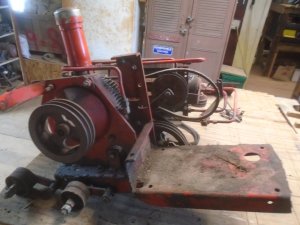
I have a new pair of 8.00x16 tractor tires that my son bought last year but never used.
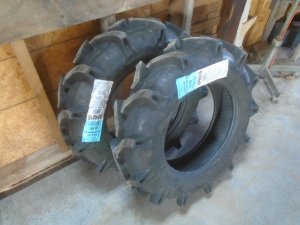
I also have a rear axle out of a mid 60's Cushman 3-wheel Truckster.
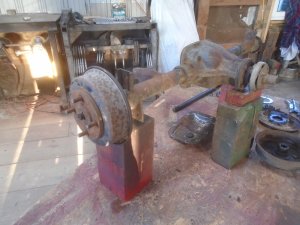
Pulling the brake drums off, there aren't any brake shoes or wheel cylinders and the axle oil seals are leaking bad.
These parts are available but they are pricey. I'm not going to bother with replacing the brakes because the hydrostatic unit acts as a braking unit also. I am going to replace the oil seals and I intend to mount a 4 inch diameter band brake on the drive side of the hydrostatic pump for a parking brake ( this could also be used as a regular stopping brake ).
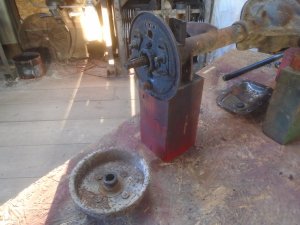
The gears inside look really good.
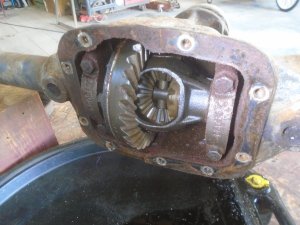
I like the design of the Ridemaster tractor with the engine mounted right on the front drive wheels and with them being able to turn so far around.
I want to build this engine and drive unit with the same design. The Cushman axle is about 42 inch wide and obviously I'm not going to be able to get the wheels as close together as they are on the Ridemaster but I can shorten it up some.
So I have removed the axle shaft from the left side.
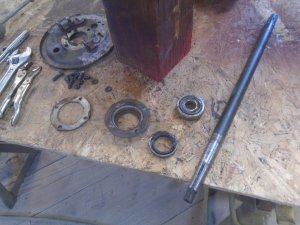
Measuring the housing, it looks like I can shorten it about 8 or maybe 9 inches. That would make the wheel spacing about the same as most 2-wheel walk behind tractors and I can make the axle so it pivots in the center for turning.
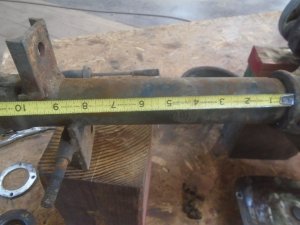
However .. there was one drawback. The Ridemaster just didn't have enough horsepower.
The roller is 5 foot long and 2 foot diameter and weighs around 970 pounds when full of water. The Ridemaster would move it alright on level ground but could hardly make it up any incline at all.
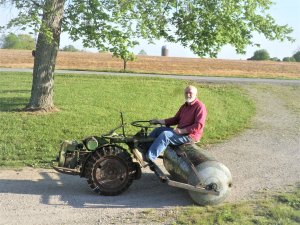
I went ahead and used the powered roller to pack down the gravel that I had put down in front of the garage, then I removed the roller drum from the Ridemaster and mounted the hitch back on it so it could be pulled behind the tractor again.
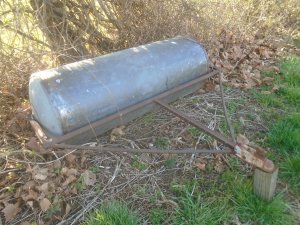
After using it as a pull behind roller again for awhile, I decided that I really liked it better when it was self powered.
Of course I could put it back on the Ridemaster and then put a bigger engine on it too but that would rune a restorable Ridemaster that is complete.
So I looked thru my stuff to see what I could use to power the roller.
I have this 18 HP B&S twin cylinder engine that should give it enough horsepower.
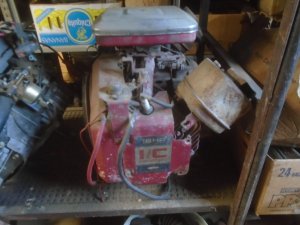
And this hydrostatic drive pump for forward and reverse.
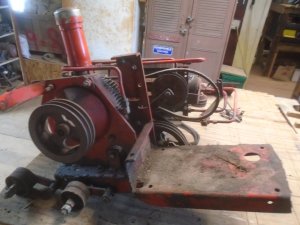
I have a new pair of 8.00x16 tractor tires that my son bought last year but never used.
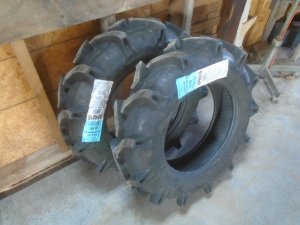
I also have a rear axle out of a mid 60's Cushman 3-wheel Truckster.
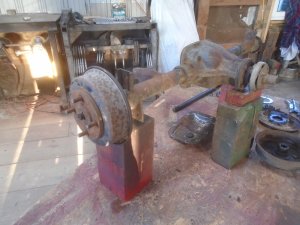
Pulling the brake drums off, there aren't any brake shoes or wheel cylinders and the axle oil seals are leaking bad.
These parts are available but they are pricey. I'm not going to bother with replacing the brakes because the hydrostatic unit acts as a braking unit also. I am going to replace the oil seals and I intend to mount a 4 inch diameter band brake on the drive side of the hydrostatic pump for a parking brake ( this could also be used as a regular stopping brake ).
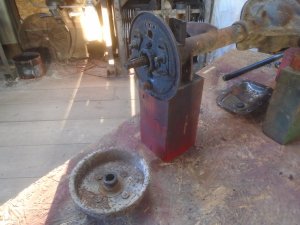
The gears inside look really good.
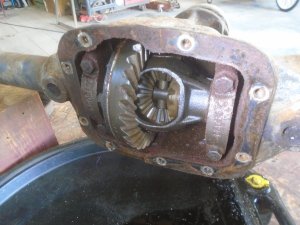
I like the design of the Ridemaster tractor with the engine mounted right on the front drive wheels and with them being able to turn so far around.
I want to build this engine and drive unit with the same design. The Cushman axle is about 42 inch wide and obviously I'm not going to be able to get the wheels as close together as they are on the Ridemaster but I can shorten it up some.
So I have removed the axle shaft from the left side.
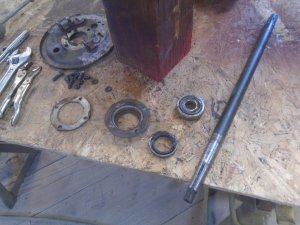
Measuring the housing, it looks like I can shorten it about 8 or maybe 9 inches. That would make the wheel spacing about the same as most 2-wheel walk behind tractors and I can make the axle so it pivots in the center for turning.
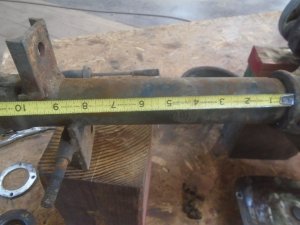
Last edited: