This deck is in great shape except for two spots I'm patching & the rollers. I've never done this before or do I weld very well. I patched these two areas. The long one worked out better than the small square one. I'm thinking the deck metal was much thinner near this area. I kept burning through but eventually got it plugged good.
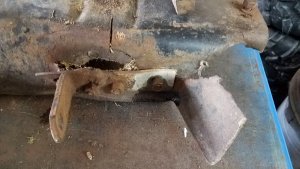
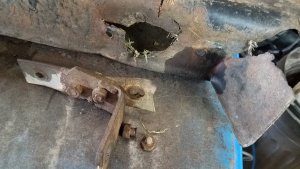
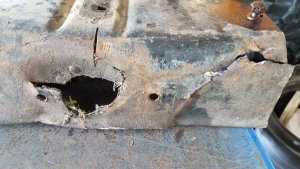
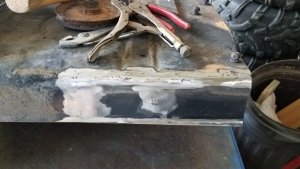
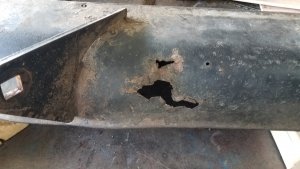

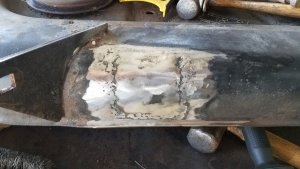
After I cleaned the welds up I spread a thin layer of JB Weld to fill in some voids.
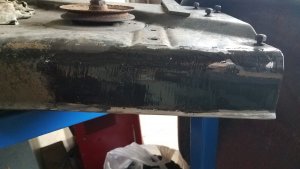
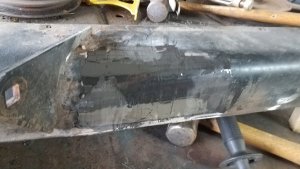
I need to get this lift handle off so I can replace the spring under the button. I have been pulling, soaking, & heating for over a week now but still not coming off.

Next up I'm going to make some rollers. These are too bad to do anything with. If I replaced them it would cost me more than the tractor. I'm thinking of cutting some pieces of 2" PVC pipe with hardwood inserts in each end of each piece with a 3/4" bushing. I might try to coat them with the black Flex Seal spray.
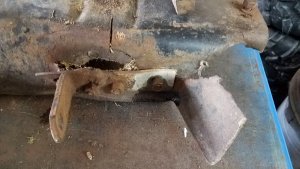
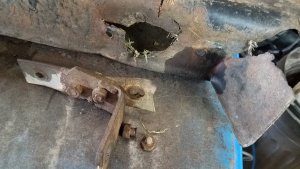
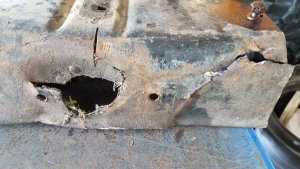
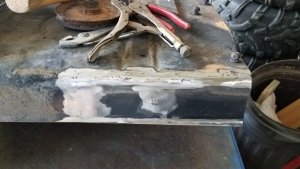
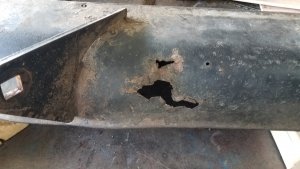

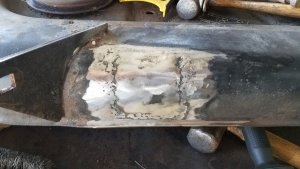
After I cleaned the welds up I spread a thin layer of JB Weld to fill in some voids.
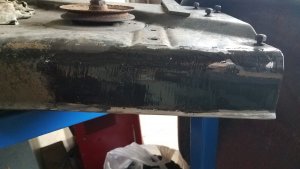
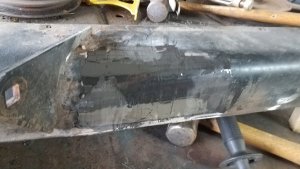
I need to get this lift handle off so I can replace the spring under the button. I have been pulling, soaking, & heating for over a week now but still not coming off.

Next up I'm going to make some rollers. These are too bad to do anything with. If I replaced them it would cost me more than the tractor. I'm thinking of cutting some pieces of 2" PVC pipe with hardwood inserts in each end of each piece with a 3/4" bushing. I might try to coat them with the black Flex Seal spray.