Two short pieces of 2 x 4 can be used so the front plate rests on them and the unit can be stood upright.
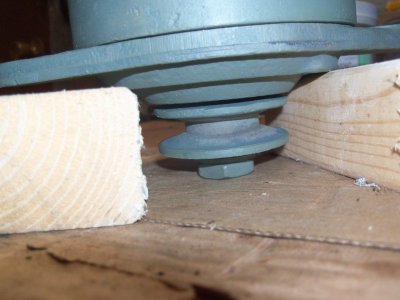
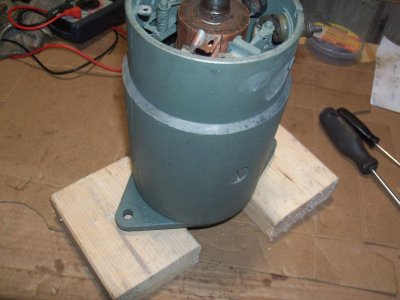
With the two brush arms, springs and field wires in their approximate place the brush arms can be held back and the brushes installed. A new set of brushes was installed as one of the wires on an old brush had broken away from the actual brush.
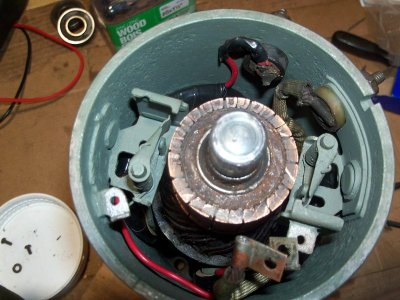
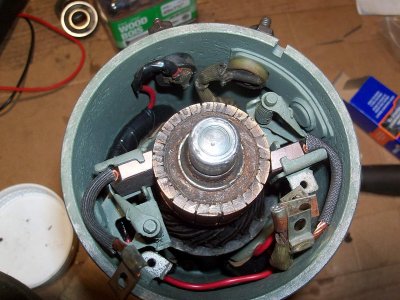
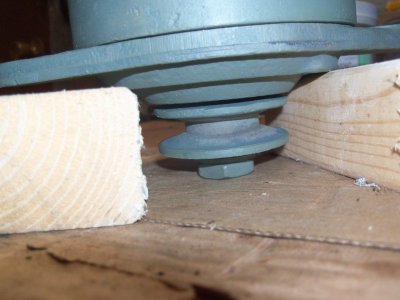
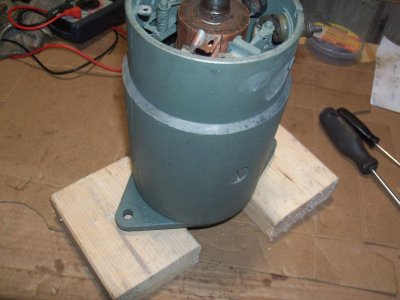
With the two brush arms, springs and field wires in their approximate place the brush arms can be held back and the brushes installed. A new set of brushes was installed as one of the wires on an old brush had broken away from the actual brush.
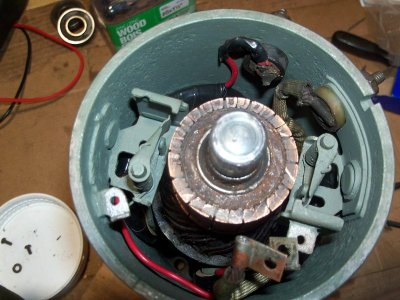
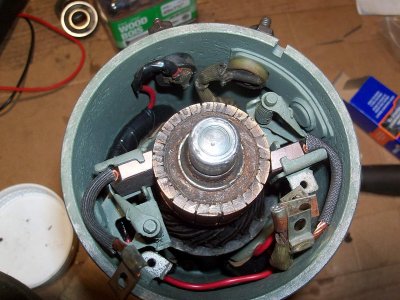