Stage-4
Tuff Torq K66 Service
This oil change is at a total of 190 hrs on the clock and 127 hrs since the last K66 oil change on mine.
Before starting, I recommend,
1) An impact wrench, air is fine, but if you have an air compressor you probably have one already, just remember to not use too much force, the top fan pulley nut is 45 foot lbs.
A cordless impact at 1/2” will be fine, 3/8” I’m not sure, so this info would be nice to know.
An electric, corded impact that can be bought for approximately $25 at 100’ lbs rating would work fine also.
The point of the impact wrench is to safely remove and install the top fan pulley nut while minimizing the risk of breaking the fragile fan blades.
Here are some examples, there's one for every budget,
Cheapest,
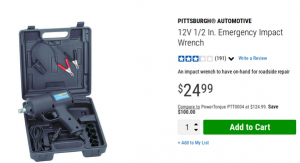
For the cordless crowd,
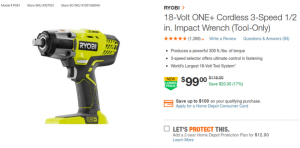
For those that have air compressor's, (I have this one, works great-6 yrs now)
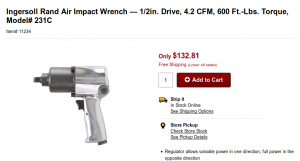
2) Have the Tuff Torq PDF’s on the service with you, I have supplied them, they are on the Tuff Torq Parts page, and I will always recommend what they say over anything I say if there is conflict. I don’t think there is any, but just in case, please, always refer to Tuff Torq over an individual such as myself, and please, don’t hesitate to talk with Tuff Torq to confirm or just get extra guidance.
I have found Tuff Torq easy to talk with in my experience, and for those skeptical, GOOD, I am too. If you doubt me and think I’m the kind of person that just gives away a job well done without any work, just read some of my earlier threads or talk with some of the senior members.
By now you should be starting here,
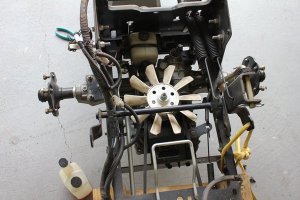
1) Make sure the top is clean, observe the reservoir bottle fluid level, is there any damage to the fan blades, is the belt frayed, etc.
This was mine,
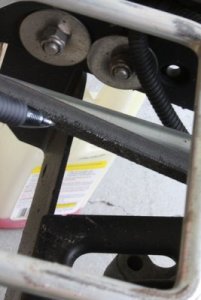
The edges of my belt show wear, I’m replacing it,
The fluid level was fine,
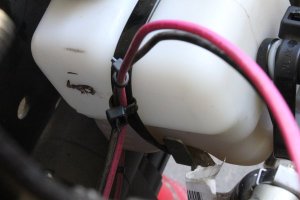
2) Remove fan, belt pulley and 15mm top nut with your impact wrench and socket. (at the low torq settings special impact sockets are not needed), it has standard threads (lefty loosey, righty tighty) While holding the belt tight on the pulley with one hand, remove the nut. The belt held choked tight against the pulley uses the natural grip of the belt to hold the pulley from moving. The impact wrench will loosen the nut by very quick hammer blows and resist loosening by leverage.
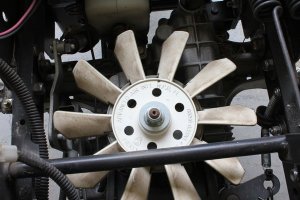
Choked belt,
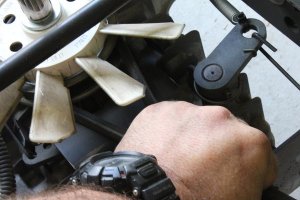
This was the built up dirt between the fan and pulley,
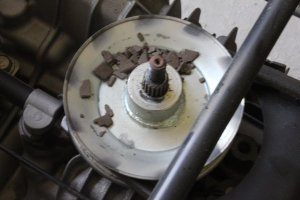
With the above being said, you can use a socket wrench. I would use a helper if possible to hold the belt with 2 hands and have sufficient strength to counter your muscle input, harder but will work fine, fan blades, fan blades, can’t say it enough. If you break them, don’t panic, they are easy to purchase not terribly priced but you will wait with your project.
If you have PB Blaster or WD-40, with care not to spray your belt (remember it’s a listed solvent too) with a straw you could put a dab on the threads to get absorbed first.
3) The belt can be easily removed from the main transaxle pulley, from the side my hand is on. If you are replacing the belt, just cut it,
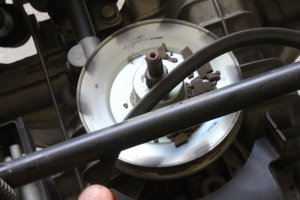
Stage-4, Continued on the next reply...
Tuff Torq K66 Service
This oil change is at a total of 190 hrs on the clock and 127 hrs since the last K66 oil change on mine.
Before starting, I recommend,
1) An impact wrench, air is fine, but if you have an air compressor you probably have one already, just remember to not use too much force, the top fan pulley nut is 45 foot lbs.
A cordless impact at 1/2” will be fine, 3/8” I’m not sure, so this info would be nice to know.
An electric, corded impact that can be bought for approximately $25 at 100’ lbs rating would work fine also.
The point of the impact wrench is to safely remove and install the top fan pulley nut while minimizing the risk of breaking the fragile fan blades.
Here are some examples, there's one for every budget,
Cheapest,
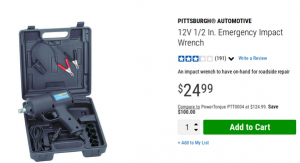
For the cordless crowd,
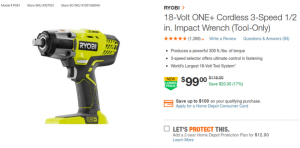
For those that have air compressor's, (I have this one, works great-6 yrs now)
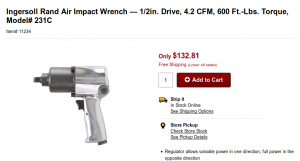
2) Have the Tuff Torq PDF’s on the service with you, I have supplied them, they are on the Tuff Torq Parts page, and I will always recommend what they say over anything I say if there is conflict. I don’t think there is any, but just in case, please, always refer to Tuff Torq over an individual such as myself, and please, don’t hesitate to talk with Tuff Torq to confirm or just get extra guidance.
I have found Tuff Torq easy to talk with in my experience, and for those skeptical, GOOD, I am too. If you doubt me and think I’m the kind of person that just gives away a job well done without any work, just read some of my earlier threads or talk with some of the senior members.
By now you should be starting here,
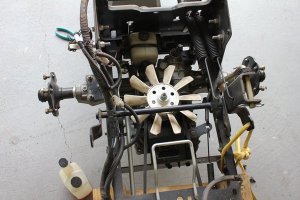
1) Make sure the top is clean, observe the reservoir bottle fluid level, is there any damage to the fan blades, is the belt frayed, etc.
This was mine,
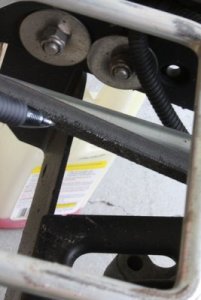
The edges of my belt show wear, I’m replacing it,
The fluid level was fine,
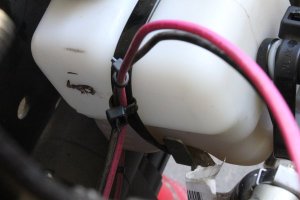
2) Remove fan, belt pulley and 15mm top nut with your impact wrench and socket. (at the low torq settings special impact sockets are not needed), it has standard threads (lefty loosey, righty tighty) While holding the belt tight on the pulley with one hand, remove the nut. The belt held choked tight against the pulley uses the natural grip of the belt to hold the pulley from moving. The impact wrench will loosen the nut by very quick hammer blows and resist loosening by leverage.
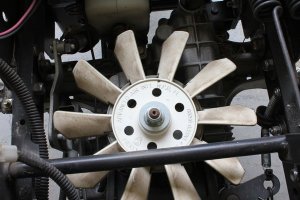
Choked belt,
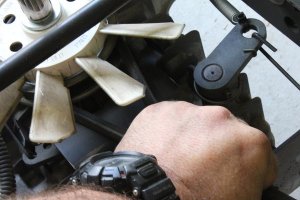
This was the built up dirt between the fan and pulley,
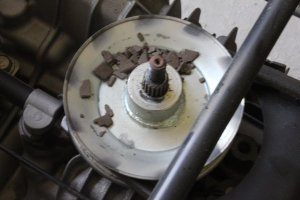
With the above being said, you can use a socket wrench. I would use a helper if possible to hold the belt with 2 hands and have sufficient strength to counter your muscle input, harder but will work fine, fan blades, fan blades, can’t say it enough. If you break them, don’t panic, they are easy to purchase not terribly priced but you will wait with your project.
If you have PB Blaster or WD-40, with care not to spray your belt (remember it’s a listed solvent too) with a straw you could put a dab on the threads to get absorbed first.
3) The belt can be easily removed from the main transaxle pulley, from the side my hand is on. If you are replacing the belt, just cut it,
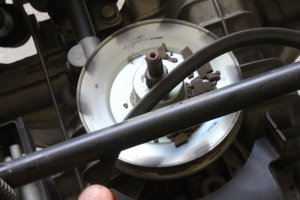
Stage-4, Continued on the next reply...