Dad couldn't resist and bought this old Van Norman Rotary Broach at the local auction. Its missing a few pieces and really needs to be cleaned and oiled up. We'll see if it was worth it when we get it into the shop and see what work and what doesn't. Everything turns and moves with no funny noises but it didn't have a plug on the cord to test it out. We have many tractor and vehicle heads that could use milling so we decided to take the risk. Its in the back of the F-250 right now and I need to put the loader on the Case IH 485 to lift it out. Not sure of the weight so we may need to use 2 loaders to lift it. This is an auction photo. I'll get some more tomorrow.
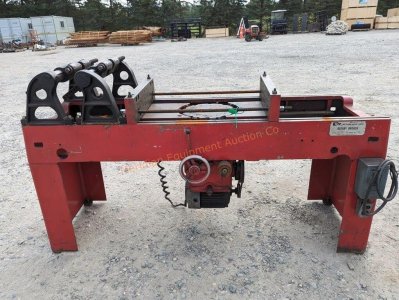
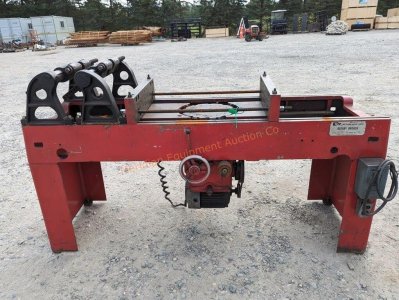