A project with me isn't a real project if there isn't a pause in progress for multiple months 
Last year I did test the trailer behind my MF1655 with a wooden tongue that I made quickly out of a 2x3 as again the length is another dimension I need to figure that might influence how the trailer reacts.
Well it went quite well if we ignore the fact that I broke the tongue multiple times! It is really weird to see the trailer react compared to a standard 2 wheeled trailer, it's hard to trust that it will not hit obstacles inside the curve.
The lessons from those tries were
- the forces applied to the tongue are way greater than I thought
- backing with the trailer is possible but weird and might not be possible in tight spots
- if the tongue is strong enough I am now convinced the tractor could break the steering mechanism, whatever the weak point would be. That being if the tractor gets turning more than the trailer can manage OR while backing the trailer
Well what puzzled me and forced me to pause the work (other than I had to disassemble the trailer to regain space in my garage for winter) is the last point where things could break. It might be overkill to tackle this problem but I did want to try it and find a way to create a mechanical "breaker" for the steering mechanism.
Fast forward to recently after unsuccessful researches online and a discussion with a friend that did suggest something wise here is what I built
First the short arm that will be from the front axle to a pivot that will allow the tongue to pivot up and down. This replaces the 2"x2" square tube that can be seen in the last picture of my previous post.
Had to use a bit of creativity to hold the parts for welding:
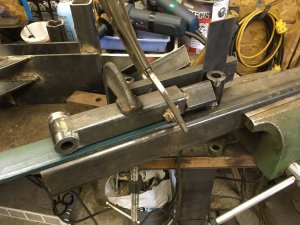
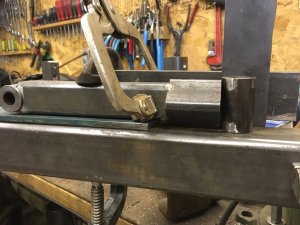
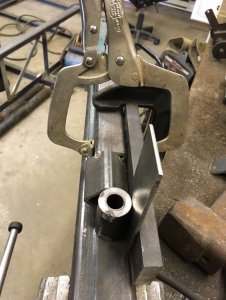
Then now we get into what's hard to explain, how this thing works. Trying to explain this... There will be 2 concentric arms on a shared vertical axis. The primary (square) one will only transfer the pulling force from the tractor to the trailer. It will be turned on it's vertical axis but this turning motion won't be transferred to the steering mechanism directly. There will be the secondary arm (flatbar) that will be able to turn over the primary arm's vertical shaft and this one will be linked by the master tie-rod to the steering mechanism. The secondary arm has an angle piece at it's end that will sit on a square part hinged on a pivot point and will be pushed down by a spring... if the force applied to the primary arm is too great the angle part will pivot and detach the secondary arm from the primary one... OK I realized before starting to write this that it's hard to understand... Pictures to the rescue!
This was the first concept that I built
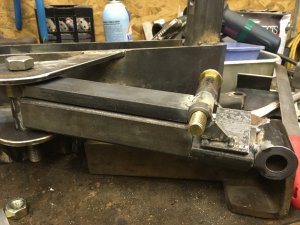
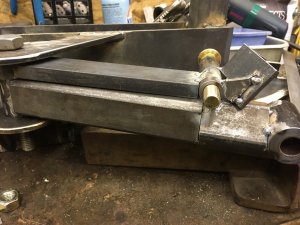
Then I realized that adding a spring to this would be near impossible, there ain't many locations where the spring can be. I had to think about this for a while then realized that I could make a spring (I have music wire and in fact it's inexpensive) and have it sit in the middle of the hinge so I rebuilt the whole thing and made a custom spring out of .100" music wire, that being a super guess. If I need I can order other diameters to change the applied force, it's so easy to make a custom spring when you have a lathe (no not under it's power for a spring that big, I turn the chuck manually).
BTW the vertical shaft with a bolt in it is where the master tie-rod will attach to the secondary arm, at the moment it's adjustable by sliding the U shape part with 4 bolts holding it but eventually the vertical shaft will most likely be welded directly to the secondary arm.
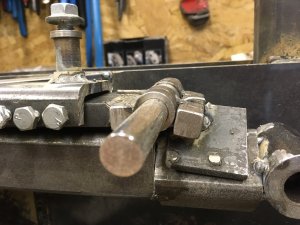
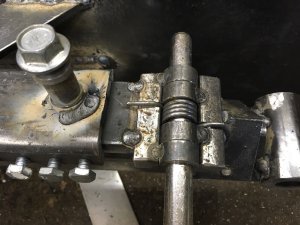
That's where I am at this time, next step will be to assemble the trailer back and try this again! Now I have a 2x2" steel tube for the tongue so hopefully this one won't break (; The biggest question at this time will be to figue what is the right spring strength that I need. Is .100" enough? I guess I can make a spring up to a .125" music wire... that will all be guesses until I think I have the right ratio but also, it's easy to swap the spring any time.

Last year I did test the trailer behind my MF1655 with a wooden tongue that I made quickly out of a 2x3 as again the length is another dimension I need to figure that might influence how the trailer reacts.
Well it went quite well if we ignore the fact that I broke the tongue multiple times! It is really weird to see the trailer react compared to a standard 2 wheeled trailer, it's hard to trust that it will not hit obstacles inside the curve.
The lessons from those tries were
- the forces applied to the tongue are way greater than I thought
- backing with the trailer is possible but weird and might not be possible in tight spots
- if the tongue is strong enough I am now convinced the tractor could break the steering mechanism, whatever the weak point would be. That being if the tractor gets turning more than the trailer can manage OR while backing the trailer
Well what puzzled me and forced me to pause the work (other than I had to disassemble the trailer to regain space in my garage for winter) is the last point where things could break. It might be overkill to tackle this problem but I did want to try it and find a way to create a mechanical "breaker" for the steering mechanism.
Fast forward to recently after unsuccessful researches online and a discussion with a friend that did suggest something wise here is what I built
First the short arm that will be from the front axle to a pivot that will allow the tongue to pivot up and down. This replaces the 2"x2" square tube that can be seen in the last picture of my previous post.
Had to use a bit of creativity to hold the parts for welding:
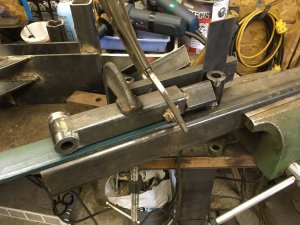
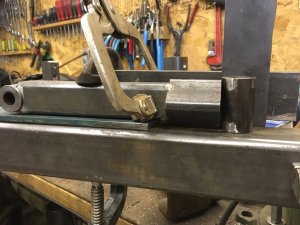
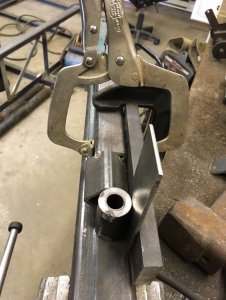
Then now we get into what's hard to explain, how this thing works. Trying to explain this... There will be 2 concentric arms on a shared vertical axis. The primary (square) one will only transfer the pulling force from the tractor to the trailer. It will be turned on it's vertical axis but this turning motion won't be transferred to the steering mechanism directly. There will be the secondary arm (flatbar) that will be able to turn over the primary arm's vertical shaft and this one will be linked by the master tie-rod to the steering mechanism. The secondary arm has an angle piece at it's end that will sit on a square part hinged on a pivot point and will be pushed down by a spring... if the force applied to the primary arm is too great the angle part will pivot and detach the secondary arm from the primary one... OK I realized before starting to write this that it's hard to understand... Pictures to the rescue!
This was the first concept that I built
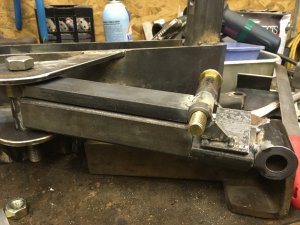
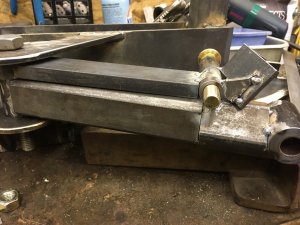
Then I realized that adding a spring to this would be near impossible, there ain't many locations where the spring can be. I had to think about this for a while then realized that I could make a spring (I have music wire and in fact it's inexpensive) and have it sit in the middle of the hinge so I rebuilt the whole thing and made a custom spring out of .100" music wire, that being a super guess. If I need I can order other diameters to change the applied force, it's so easy to make a custom spring when you have a lathe (no not under it's power for a spring that big, I turn the chuck manually).
BTW the vertical shaft with a bolt in it is where the master tie-rod will attach to the secondary arm, at the moment it's adjustable by sliding the U shape part with 4 bolts holding it but eventually the vertical shaft will most likely be welded directly to the secondary arm.
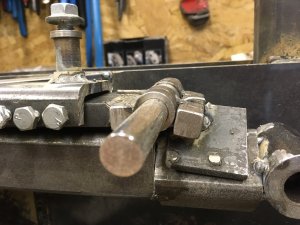
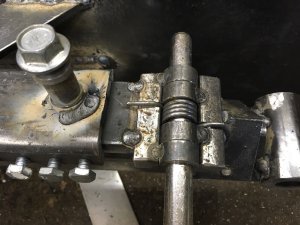
That's where I am at this time, next step will be to assemble the trailer back and try this again! Now I have a 2x2" steel tube for the tongue so hopefully this one won't break (; The biggest question at this time will be to figue what is the right spring strength that I need. Is .100" enough? I guess I can make a spring up to a .125" music wire... that will all be guesses until I think I have the right ratio but also, it's easy to swap the spring any time.