Well this was suppose to be another last year winter project but here I am eight months later into spring. I'm now making the two pull rod assemblies. Staying with the drawing using 1/4" flat bar stock & 5/8" round. The only thing I changed was the use of schedule 40 round pipe for the clevis end. I was pacing the shop trying to find something else. I happened to walk by my pallet buster which I used 1" square tube with 3/16 walls. I had another section of that. This worked out great. I think this would be a better choice anyway. I was going to thread the section but decided to just weld a 5"x 5/8" piece of all thread to the bars.

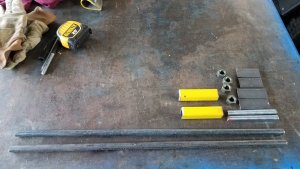
I used a 1/2" spacer & a couple of fender washers on each side to give me some clearance for the draft bar connection.
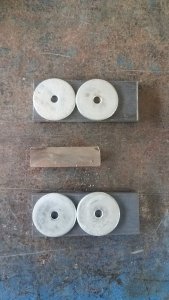
To keep the two welded nuts next to the square tube I ran the threaded rod into the tube then screwed the two nuts at the end. I then put a jamb nut at the top then tightened them together to weld, worked out great.
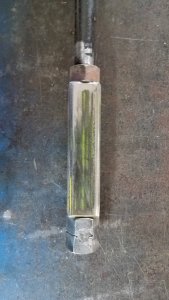
This took some time setting this contraption up. A little tap her a little there & a little shimming to align things up. I then torqued the pipe clamp then tack weld all around to keep things where there suppose to be before running a bead.
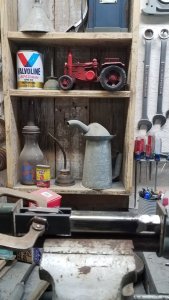
I chased the two welded nuts with a tap to clear the threads.
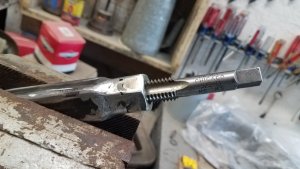
After laying everything out for a pic I thought this thing looks long! The drawing calls for 5/8" bar 26" long w/ 5" thread end. I cut my bars 26" long & welded 5" pieces of all thread & guess what! It's exactly 5" too long. The 26" long bar included the 5" of thread making the bar with threads a total of 26" not like mine 31". Well I'll just cut at the weld then cut what I don't need off then weld back. I'm thinking before I do that I'll set this whole thing up on the tractor & measure to make sure what I need.
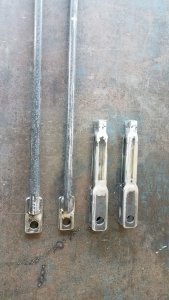
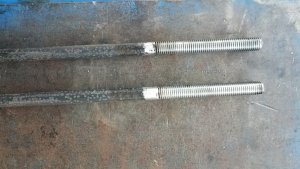
Next up making the center adjustable clevis.

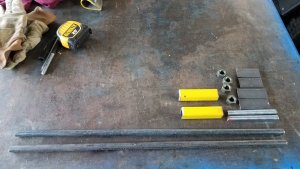
I used a 1/2" spacer & a couple of fender washers on each side to give me some clearance for the draft bar connection.
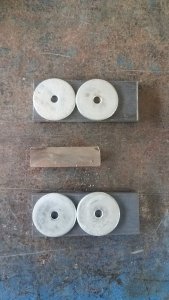
To keep the two welded nuts next to the square tube I ran the threaded rod into the tube then screwed the two nuts at the end. I then put a jamb nut at the top then tightened them together to weld, worked out great.
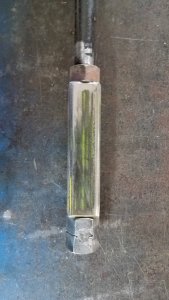
This took some time setting this contraption up. A little tap her a little there & a little shimming to align things up. I then torqued the pipe clamp then tack weld all around to keep things where there suppose to be before running a bead.
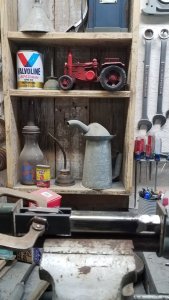
I chased the two welded nuts with a tap to clear the threads.
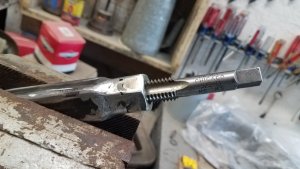
After laying everything out for a pic I thought this thing looks long! The drawing calls for 5/8" bar 26" long w/ 5" thread end. I cut my bars 26" long & welded 5" pieces of all thread & guess what! It's exactly 5" too long. The 26" long bar included the 5" of thread making the bar with threads a total of 26" not like mine 31". Well I'll just cut at the weld then cut what I don't need off then weld back. I'm thinking before I do that I'll set this whole thing up on the tractor & measure to make sure what I need.
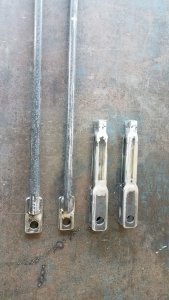
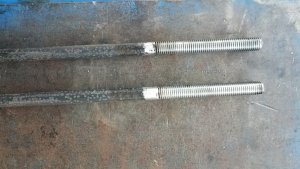
Next up making the center adjustable clevis.