Given the age of my tractor and the obvious lack of maintenance in the past, the needle bearings in which the blades shafts are running directly (no sleeve), over time the bearings managed to wear out the shafts. Back when this tractor wasn't mine the owner had me replace one of the shafts that was really worn out with a brand new and now came the time to fix the other shafts.
BTW you'll see 3 shafts in the pictures, I had kept the replaced shaft and we fixed it. It won't be used as I'll leave the "brand new" one running but it will already be fixed.
I asked for the prices of the 2 shafts models... One of the shafts was 350$+ (CAN) and the other one NLA. Of course, got to be complicated. Having such shafts built from scratch would be even more expensive especially that they are hardened on their whole length.
Well I'm lucky enough to have amazing friends, one of them being a skilled welding teacher and the other one owning a CNC lathe and an extensive array of tooling (same friend that machined me pulleys for my JD 47 snowblower).
I prepared the shafts on my lathe by turning them down where the needle bearing runs on the shaft as to remove any dirt or contaminates. No picture at this stage sadly ):
Then my welder friend did his magic with a specific kind of welding rods made to rebuild shafts and provide a really hard surface, something in the bearing-race range (55-60 rockwells). He followed a time-consuming procedure of doing 2 passes opposite to each other on the shafts then letting it cool down. This way he made sure (and verified) not to overheat the shaft which would have un hardened it.

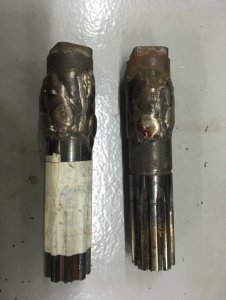
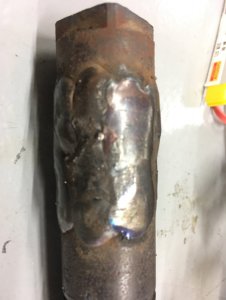
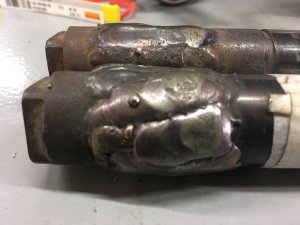
And then another time-consuming task, we machined down the shaft with a CBN insert (Cubic Boron Nitride, harder than "standard" carbide insert, just a bit less hard than diamond) to the correct diameter (IIRC 25mm, close to 1 inch but not exactly; even back in those days the bearings installed in US-made tractors were metric!). It was time consuming since machining such hard material require tiny depth of cut, something like 0.005". It was something like 35-40 passes of ~20s each or roughly half an hour of machining per shaft.
Here is a video of the machining, yes it's expected not to have standard chips but close to "molten" metal flowing away :
Good and bad news. The surface finish is AMAZING! it's nearly mirror finish! On the other hand there is still some pitting in the surface at some locations...
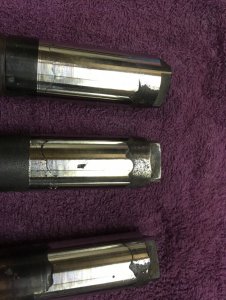
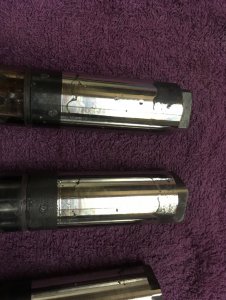
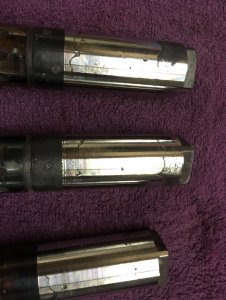
It's not too clear why it happened and given it's so time consuming it will stay this way. The bearings will probably wear out faster... may be the shafts too...
As a mitigation, I added grease fittings to the 3 spindle housings so I'll be able to "push" any debris that forms overtime out of the needle bearings. I'll inspect the bearings each couple of years and worst case I'll replace them if they start to show signs of damages as a mitigation. Best scenario would have been to make brand new shafts... May be I'll have to do this in the future, I'll see.
An alternative fix could have been to put a sleeve on the damaged section and use a bigger needle bearing after having modified the spindle to accept a bigger needle bearing but I preferred trying to stay as OEM as possible. Turning down the shafts and adding a sleeve with the correct diameter for the needle bearings was out of the question as it would have removed too much of the square by which the blade holders are powered from. Spray welding was out of the equation as it doesn't provide a hardened surface on which a bearing can run directly.
So far the mower is a bit quieter (the timing belts create quite a lot of noise) and there are no strange noises coming out of it.
BTW you might observe on the pictures that the shafts seem a bit to have run-out toward the square. We don't know if the OEM shafts were a bit crooked or if the welding bent them but the blade turn straight, at least enough for a mower.
I hope some of you found this interesting
BTW you'll see 3 shafts in the pictures, I had kept the replaced shaft and we fixed it. It won't be used as I'll leave the "brand new" one running but it will already be fixed.
I asked for the prices of the 2 shafts models... One of the shafts was 350$+ (CAN) and the other one NLA. Of course, got to be complicated. Having such shafts built from scratch would be even more expensive especially that they are hardened on their whole length.
Well I'm lucky enough to have amazing friends, one of them being a skilled welding teacher and the other one owning a CNC lathe and an extensive array of tooling (same friend that machined me pulleys for my JD 47 snowblower).
I prepared the shafts on my lathe by turning them down where the needle bearing runs on the shaft as to remove any dirt or contaminates. No picture at this stage sadly ):
Then my welder friend did his magic with a specific kind of welding rods made to rebuild shafts and provide a really hard surface, something in the bearing-race range (55-60 rockwells). He followed a time-consuming procedure of doing 2 passes opposite to each other on the shafts then letting it cool down. This way he made sure (and verified) not to overheat the shaft which would have un hardened it.

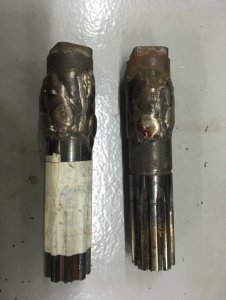
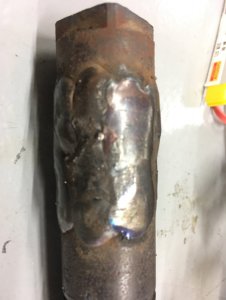
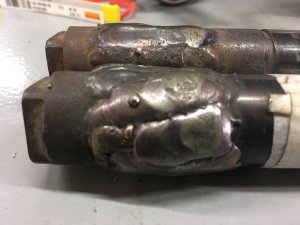
And then another time-consuming task, we machined down the shaft with a CBN insert (Cubic Boron Nitride, harder than "standard" carbide insert, just a bit less hard than diamond) to the correct diameter (IIRC 25mm, close to 1 inch but not exactly; even back in those days the bearings installed in US-made tractors were metric!). It was time consuming since machining such hard material require tiny depth of cut, something like 0.005". It was something like 35-40 passes of ~20s each or roughly half an hour of machining per shaft.
Here is a video of the machining, yes it's expected not to have standard chips but close to "molten" metal flowing away :
Good and bad news. The surface finish is AMAZING! it's nearly mirror finish! On the other hand there is still some pitting in the surface at some locations...
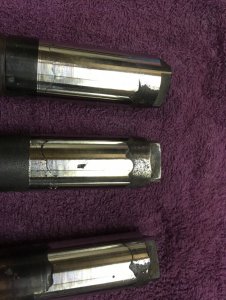
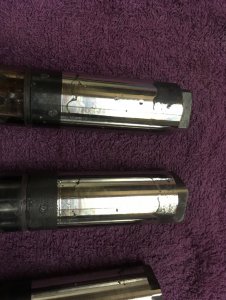
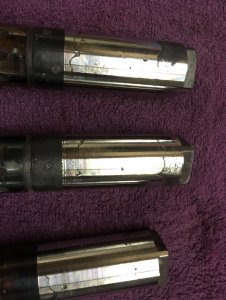
It's not too clear why it happened and given it's so time consuming it will stay this way. The bearings will probably wear out faster... may be the shafts too...
As a mitigation, I added grease fittings to the 3 spindle housings so I'll be able to "push" any debris that forms overtime out of the needle bearings. I'll inspect the bearings each couple of years and worst case I'll replace them if they start to show signs of damages as a mitigation. Best scenario would have been to make brand new shafts... May be I'll have to do this in the future, I'll see.
An alternative fix could have been to put a sleeve on the damaged section and use a bigger needle bearing after having modified the spindle to accept a bigger needle bearing but I preferred trying to stay as OEM as possible. Turning down the shafts and adding a sleeve with the correct diameter for the needle bearings was out of the question as it would have removed too much of the square by which the blade holders are powered from. Spray welding was out of the equation as it doesn't provide a hardened surface on which a bearing can run directly.
So far the mower is a bit quieter (the timing belts create quite a lot of noise) and there are no strange noises coming out of it.
BTW you might observe on the pictures that the shafts seem a bit to have run-out toward the square. We don't know if the OEM shafts were a bit crooked or if the welding bent them but the blade turn straight, at least enough for a mower.
I hope some of you found this interesting
