Testing Of Three Wire PM Alternators
Consult the manufacturer’s specifications and service manual for the correct test procedures if available.
If this service information is not available there are a few tests that can be performed on three wire PM alternators to verify if they are working. Below is a picture that shows three possibilities as to how a three wire stator may be configured and a few tests that the reader can perform to verify if the PM alternator is producing voltage.
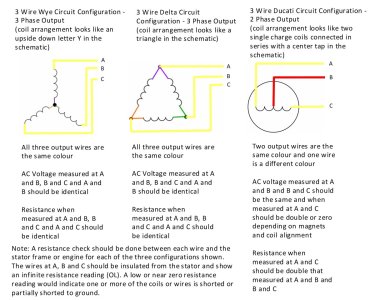
Since I have never worked on a three wire stator system I cannot tell you what the resistance or voltage readings should be. In the three wire three phase configured units where all three wires are the same colour I would suggest labelling the three wires as A, B and C with a piece of masking tape so you make sure you are testing the correct wire during each test. In testing the three wire two phase stator it would only be necessary to label the two wires which are the same colour.
I would suggest that the voltage and resistance readings should be similar to what is observed in a two wire system and to make sure that all three wires have an infinite resistance when an ohm meter is used to check for conductivity between each wire and the stator frame or engine ground as each of the wire circuits should not be connected to a ground point as shown in the schematics I have drawn. The biggest thing to remember is that the voltage level at all three phases of alternating current on the three phase wiring configurations should be almost identical and that resistance checks of each of the three separate coils on a 3 phase system should also be almost identical as well. If the voltage levels of all three phases are virtually identical on a three phase unit configuration and as described earlier on a two phase unit configuration the PM alternator portion of the charging system is probably ok.
There may be a wiring problem, a blown fuse or a bad rectifier / regulator elsewhere in the charging system circuit. Check the connections at all the terminals where the wires connect to the rectifier / regulator as well as the three wires that connect it to the PM alternator output wires to verify they are not shorted or open using standard testing procedures. Check to make sure that the wire that connects to the ground terminal on the rectifier / regulator (if so equipped) has good continuity with the negative terminal of the battery. If the rectifier / regulator body of the unit acts as the ground connection in the direct current portion of the charging circuit verify it has a good ground connection. Running a temporary jumper wire from the body of the regulator / rectifier to the negative terminal of the battery can be done to verify there is not a bad ground connection through the chassis. Also check the fuse in the wiring as having an open circuit between the body of a rectifier / regulator and the ground point can sometimes result in the fuse blowing from my experience. If the three wire PM alternator is outputting an AC voltage as described earlier and all other connections and switches have been verified as having good conductivity then odds are the rectifier / regulator has failed. There is no way of accurately testing most rectifier / regulators that I know of and from what I have read. There are tests suggested by manufacturers to determine the integrity of the rectifier diodes but these will usually prove inconclusive and most will eventually tell you to replace the rectifier / regulator with a known good working unit to see if it fixes the problem.
If there was no or a very low voltage reading (under 15 volts) observed with the AC voltmeter connected as described earlier first verify that you have the multimeter set to measure AC volts and not DC volts – this is an easy mistake to make and I have done it myself. Once that is verified it may be assumed that one or more of the charge coils or stator, a connection or wires going to it or the flywheel magnets are bad. If this is the case removal and inspection of the stator is in order so it can be inspected for any burn or heat damage and to verify the exact configuration of the three wire stator to ensure the correct tests were being done.
This concludes the theory and testing information I can offer on a three wire PM alternator.
Hopefully others reading this have found it informative and now have a better understanding of PM alternator charging systems and their testing to help diagnose and repair a PM alternator charging problem.