The crawler was too fast when I had first got it running and I had put as small a sprocket as I could on the right angle drive box to slow it down.
However, it is still way to fast.
In first gear, it runs the speed that I feel it should be in 2ed or 3ed gear.
It won't move the crawler at all in 3ed gear now.
So I need to figure out how to reduce the gear ratio some more.
To do that, I've got together these parts so that I can make a jackshaft with different size sprockets on it.
The small sprocket is welded to the hub but the larger sprocket is bolted to the hub instead of welded.
I did this so that if I still need to make it slower, I can easily put a larger sprocket on that hub.
Here's how it looks put together.
The jackshaft assembly will almost fit in the space to the left of the right angle gearbox.
I have unbolted the mounting brackets for the drive gearbox and moved it over to the right about 1/2 inch. This will be just enough so the the left mounting bracket for the jackshaft will clear the clutch & brake assembly on the left side by about 1/4 inch.
I have also taken the drive sprocket off the drive gearbox and turned to around to that it is no longer lined up with the lower sprocket.
With moving the drive gearbox over that 1/2 inch, I also need to move the lower sprocket over the same amount on the axle shaft.
The left mounting bracket is made up for the jack shaft and bolted in place.
The right mounting bracket is made up but not fastened in place yet.
I have to mill slots into both mounting brackets for the mounting bolts so I can adjust the jackshaft.
This shows how the jackshaft will fit down into this space.
The chain from the sprocket on the drive gearbox will go to the large sprocket on the jackshaft.
Then the chain from the small sprocket on the jackshaft will go down to the sprocket on the axle to reduce the final drive gearing.
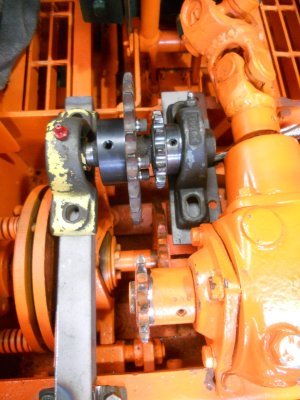