2018-03-16
Ok, the snowblower will probably not be useful for this winter ): I think I am listening too much to ThisOldTony, Joe Pieczynski and Stefan Gotteswinter videos!
Anyway, here is a part (well 2) I needed to make. Previous owner ate them and replaced them by silly parts he welded to the snowblower... I did not agree with that
To make this recipe you will need
- 12" of 1.25" x 0.375" flatbar
- 9.5" of 2" x 0.25" flatbar
- 2x 0.125" drill bits (you will break one and strugle to remove it from the hole)
- 0.375" drill bit (this one is still no match for the Delta DP600 but you won't break it)
- a drill press
- a welder
- a Markal silver-streak (this is the magic pen to write on metal, even oily or greasy!)
- a bandsaw
- a 20T press
- scrap metal to use as cheap bending die since you never have the time to build a copy of Swag Offroad's bending press
Consider that I am using .25" stock on the ground since I did not want to try killing myself with flying metal bending something thicker. Safety first!
First after looking after every single pictures of this part on Google and not finding much dimensions, you will draw this on your stock
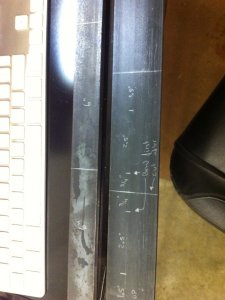
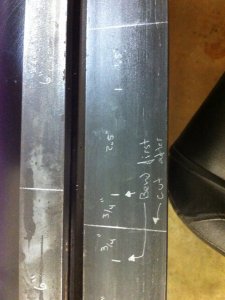
Since you don't have proper bending tools, you will set both short ends in the center and make the bends BEFORE cutting the 2 parts appart. This will make up for the too wide bottom die you made.
Then you will enjoy making your parts forgetting to take pictures of the process and will come up with that
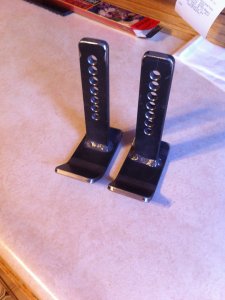
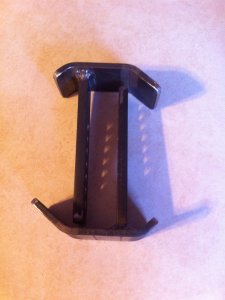
Quick informations making up for missing pictures
To make the hole equally unevenly spaced on both parts, weld them together and drill them both at the same time. Drilling 7 deep holes is faster and more "ISO-ish" than 14 shorter holes. Those holes are for adjusting the height. I need only one (my driveway is pretty flat) but I like breaking drill bits therefore I made all of them.
The holes are spaced 0.5" apart and on the female part (the snowblower) there are 2 holes 0.75" apart. This will give you adjustment by 0.25" increments. I plan on adding a 3rd hole on the female part 0.875" from one of the 2 others to upgrade to 0.125" increments. Do I really need this? I don't know but I prefer drilling before painting the whole thing.
Those are the shoes for behind the snowblower to prevent it from digging while going backward mostly. The longer side go backward.
Next step will be to make the front shoes!