I picked up this sickle mower back while I was still living up in Buckley, Michigan.
I don't know what it was used on. I had thought a Gravely but I don't think so. The drive connection is on the front so that means that it had to have been mounted on the back of a tractor. Gravely attachments are mounted on front and the photos that I've found of their sickle mowers don't look anything like this.
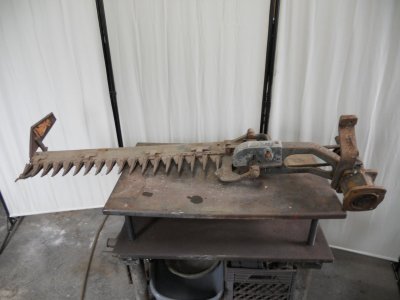
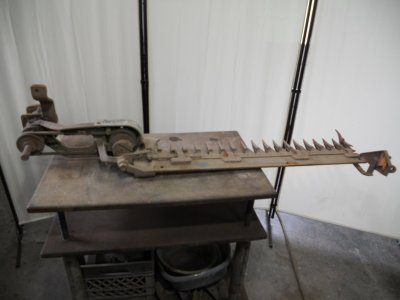
The drive pulley housing fastenings to the tractor.
The cast iron bracket going out to the sickle bar can rotate up and down from the drive pulley housing.
The sickle bar can also rotate up and down from the end of this bracket.
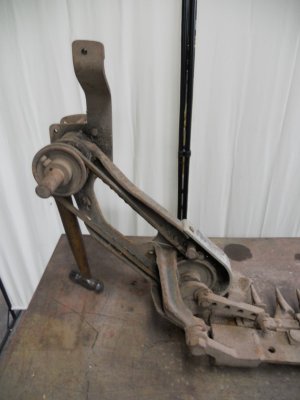
The drive wheel that the pitman arm is attached to has a counterbalance weight on it.
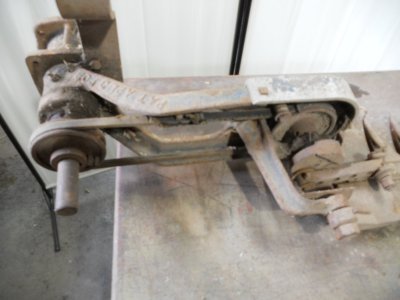
There is a notch machined into the pitman arm for clearance for this counterbalance weight.
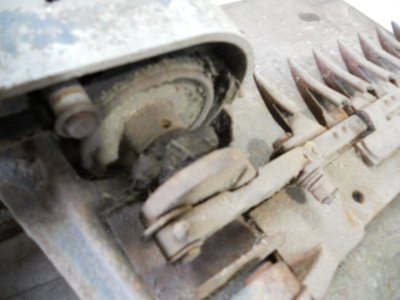
One tooth has the point broken off of it but I have some extra teeth somewhere.
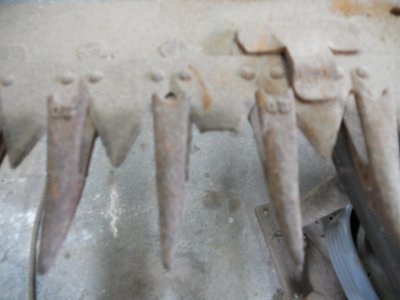
Even before I had picked up this sickle bar, I had built up a mid 1960's Sears Custom garden tractor with a sickle mower on it.
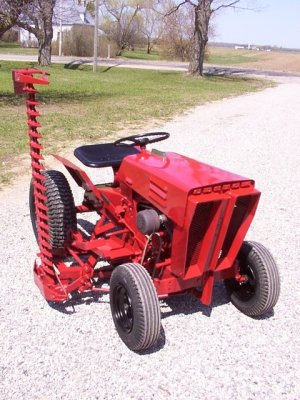
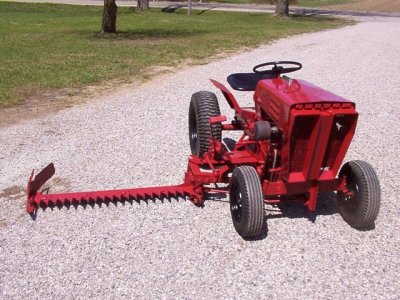
I ended up selling that tractor.
After I got this sickle bar, I thought of building up another Sears tractor with a sickle bar mower again so I found another Sears Custom garden tractor to put this sickle bar on.
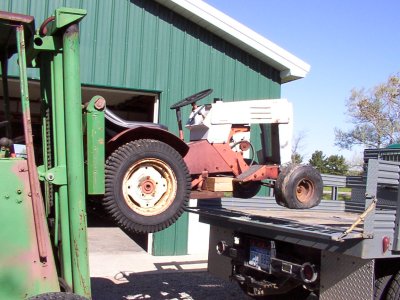
However, I'm thinking of putting this sickle bar on my old 38 Shaw garden tractor instead of re-doing another Sears ?
There certainly looks like there is enough room under it to mount the mower down between the front and rear wheels on this side.
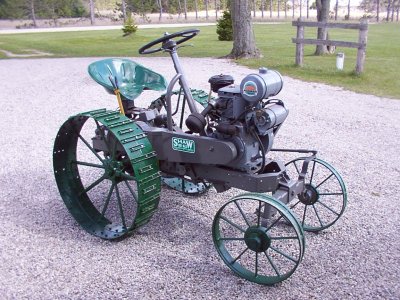
I don't know what it was used on. I had thought a Gravely but I don't think so. The drive connection is on the front so that means that it had to have been mounted on the back of a tractor. Gravely attachments are mounted on front and the photos that I've found of their sickle mowers don't look anything like this.
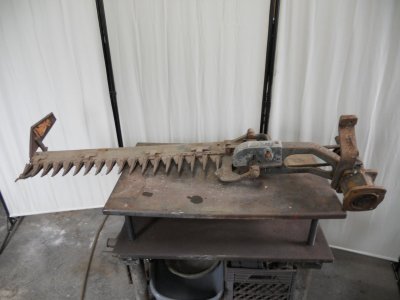
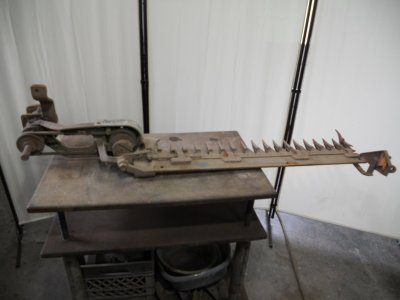
The drive pulley housing fastenings to the tractor.
The cast iron bracket going out to the sickle bar can rotate up and down from the drive pulley housing.
The sickle bar can also rotate up and down from the end of this bracket.
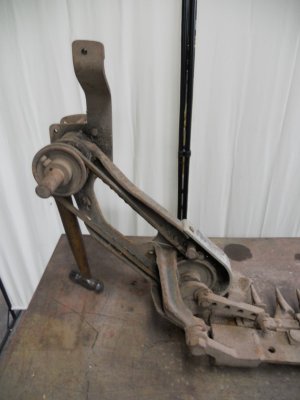
The drive wheel that the pitman arm is attached to has a counterbalance weight on it.
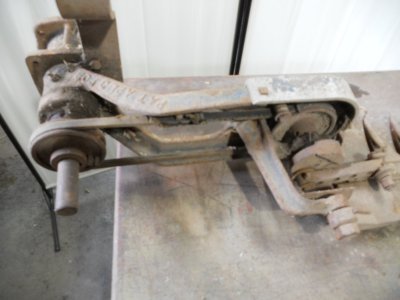
There is a notch machined into the pitman arm for clearance for this counterbalance weight.
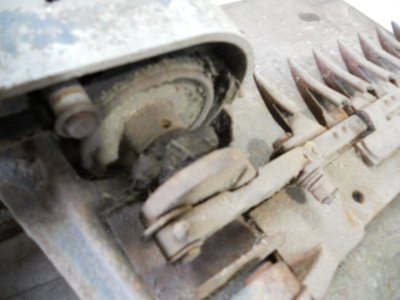
One tooth has the point broken off of it but I have some extra teeth somewhere.
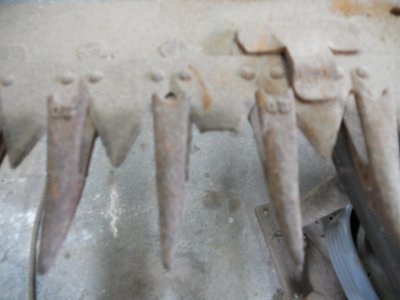
Even before I had picked up this sickle bar, I had built up a mid 1960's Sears Custom garden tractor with a sickle mower on it.
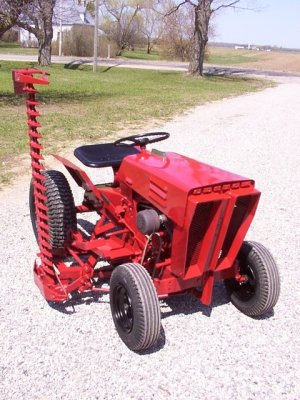
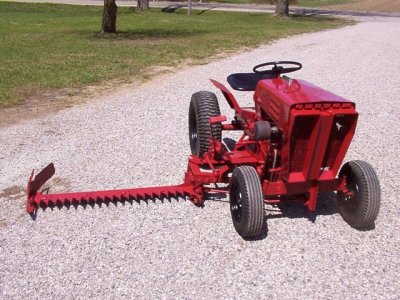
I ended up selling that tractor.
After I got this sickle bar, I thought of building up another Sears tractor with a sickle bar mower again so I found another Sears Custom garden tractor to put this sickle bar on.
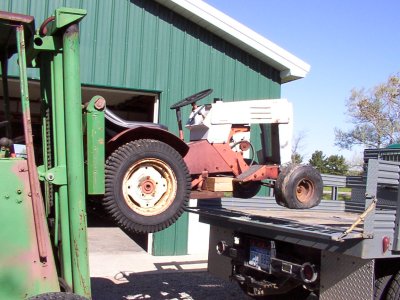
However, I'm thinking of putting this sickle bar on my old 38 Shaw garden tractor instead of re-doing another Sears ?
There certainly looks like there is enough room under it to mount the mower down between the front and rear wheels on this side.
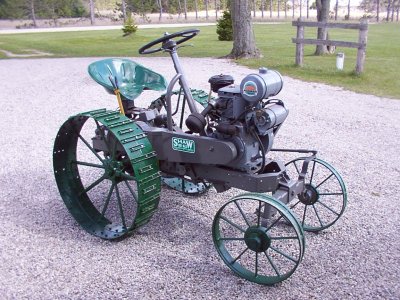
Last edited: