I have mounted the shifter on the back of the transmission and I have also made up the shaft that goes thru the bellhousing that will operate the throwout bearing.
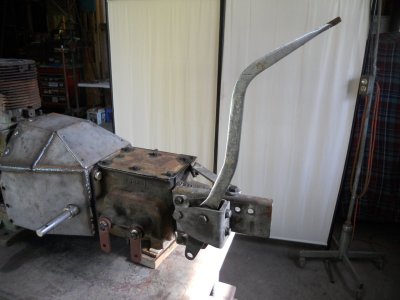
The shifter can be mounted in three different positions. It is in the farthest forward position now. I won't make up the shifter rods until I know which of the three positions the shifter will be in.
I'm waiting for a Farmall Cub throwout bearing to arrive so I can't go any farther on the transmission.
While I'm waiting on parts, I have gotten out the parts for the two drive clutches on the rear axle. The clutch pads are removed from the clutch discs and the discs plates have been sandblasted.
I got on line and found new clutch pads that are the same size as what is on this crawler. They are for a bush hog mower so I have ordered 4-new clutch pads and the rivets to mount them.
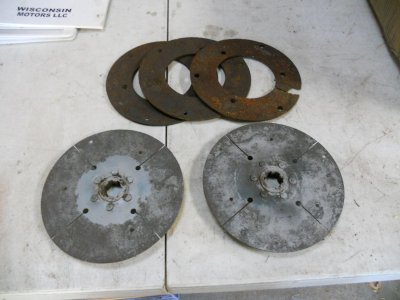
The clutch disc plates have been sandblasted, primed and painted gray.

These are the rest of the parts to complete the rear axle.
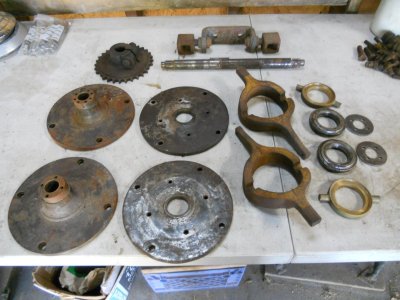
These parts have been sandblasted and primed.
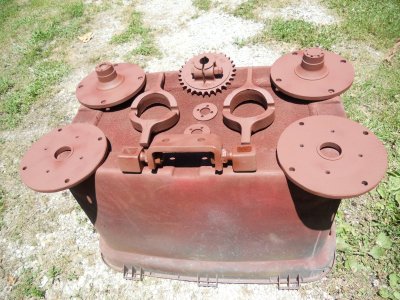
These are the original springs for the drive clutches. They all have become rusted, some rather badly. After cleaning them up and priming them, I have decided that I'm not going to use them.
Luckily, these are the same size as the springs that are used on stamping dies so I have ordered 8-new ones and have thrown the old ones away.
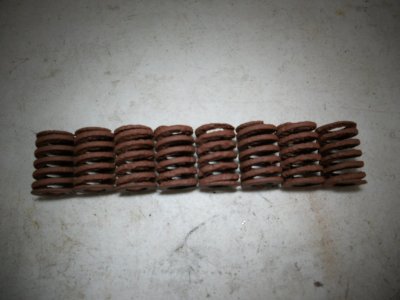
So now I'm waiting on even more parts to arrive. Meanwhile, I can still set up the rear drive system.
I've mounted the rear chain sprocket on the axle shaft and bolted it in place.
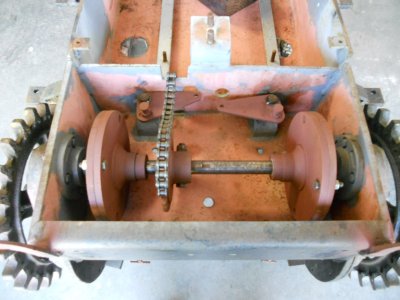
I never had the correct engine or transmission for this little crawler but I did get this right angle drive gearbox with it.
The gearbox is mounted with 4-bolts on the bottom of it. I have made up two angle iron brackets and bolted them to the bottom of the gearbox.
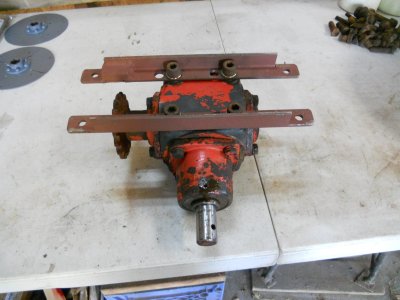
This way I can mount it in the crawler from above instead of having to bolt in place from under the crawler.
The gearbox is set in place and ready to have the mounting holes drilled and tapped thru the holes in the angle iron brackets.
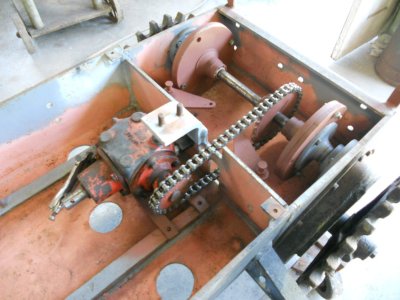
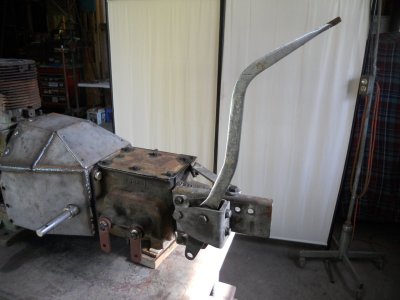
The shifter can be mounted in three different positions. It is in the farthest forward position now. I won't make up the shifter rods until I know which of the three positions the shifter will be in.
I'm waiting for a Farmall Cub throwout bearing to arrive so I can't go any farther on the transmission.
While I'm waiting on parts, I have gotten out the parts for the two drive clutches on the rear axle. The clutch pads are removed from the clutch discs and the discs plates have been sandblasted.
I got on line and found new clutch pads that are the same size as what is on this crawler. They are for a bush hog mower so I have ordered 4-new clutch pads and the rivets to mount them.
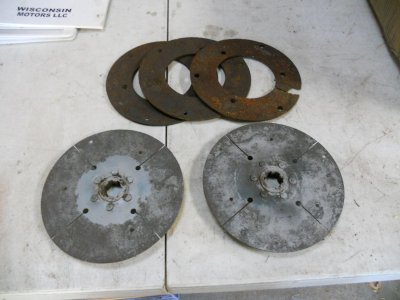
The clutch disc plates have been sandblasted, primed and painted gray.

These are the rest of the parts to complete the rear axle.
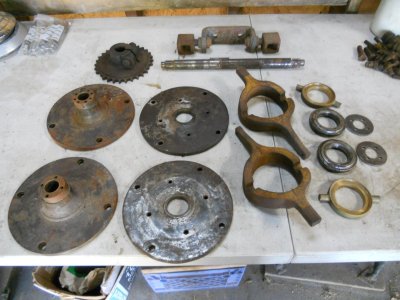
These parts have been sandblasted and primed.
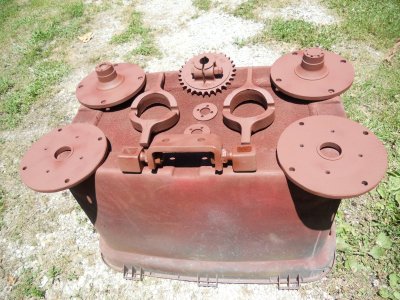
These are the original springs for the drive clutches. They all have become rusted, some rather badly. After cleaning them up and priming them, I have decided that I'm not going to use them.
Luckily, these are the same size as the springs that are used on stamping dies so I have ordered 8-new ones and have thrown the old ones away.
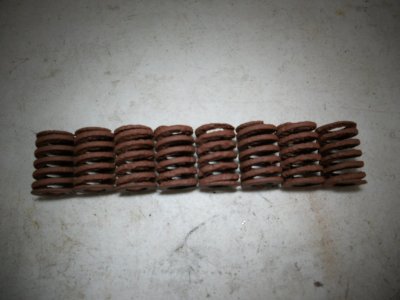
So now I'm waiting on even more parts to arrive. Meanwhile, I can still set up the rear drive system.
I've mounted the rear chain sprocket on the axle shaft and bolted it in place.
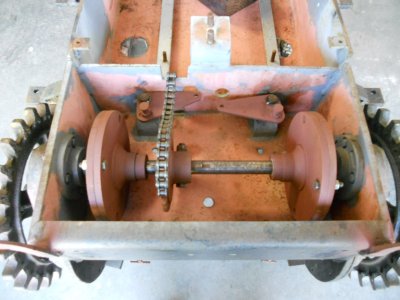
I never had the correct engine or transmission for this little crawler but I did get this right angle drive gearbox with it.
The gearbox is mounted with 4-bolts on the bottom of it. I have made up two angle iron brackets and bolted them to the bottom of the gearbox.
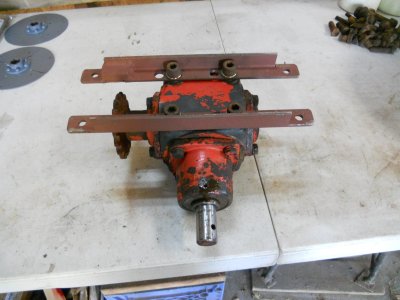
This way I can mount it in the crawler from above instead of having to bolt in place from under the crawler.
The gearbox is set in place and ready to have the mounting holes drilled and tapped thru the holes in the angle iron brackets.
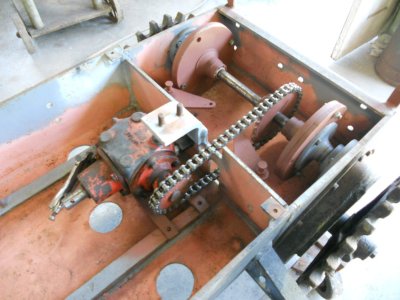