Okay .. change of plans again !
When I first started working on this crawler, I wanted to put a front end loader on it so I went looking on the internet to see what was available.
Because this is about the same size of the bigger garden tractors, I was looking for garden tractor loaders for sale and I found two within about an hour and a half drive from me.
These both had a 4 foot wide bucket which would work well with my crawler being 3 foot wide but I ran into two problems.
#1 - the inside width between the upright posts that attach to the tractor were only around 30 inches wide so that would be a problem.
Also, after getting some closeup photos of the loaders and size dimensions for the upright posts and the loader arms, I realized that these would not be strong enough for this loader.
With this crawler having twice the horsepower than the regular Agricat and weighing much more than the average garden tractor, it will put much more force on the loader and the garden tractor loader frame just isn't strong enough to suit me.
#2 - the price was $1,300 and 1,800.
The width of the buckets on the regular tractor loaders that I looked at are 6 or 7 foot wide and the inside width between the uprights and the loader arms run around 4 to 4-1/2 foot wide so they would take a lot of work to make one of them fit.
Also, the price for anything that was within reasonable condition was $1,500 to $2,500 range.
That is when I had decide to forget about a loader and just use this grader blade that I already have.
A couple of weeks ago, while casually looking thru Marketplace on Facebook, I saw an add that had just been posted about an hour before for this front end loader off a midsize utility tractor for $600.
It was only about 45 minutes from me and after getting some dimensions from the seller, I bought the loader.
The rams on three of the hydraulic cylinders are in very good condition.
The ram on the left side of the bucket has a lot of small fine pits.
All four rams were coated with grease.
All four cylinders are 24 inch long housings.
I will have to shorten the loader arms but it looks like I won't have to do much ( if anything ) to the width.
Everything is plenty strong enough to handle the force of being mounted on the crawler.
The bucket is about 54 inch wide so that is only 6 inches wider than the garden tractor loader bucket.
The inside width between the loader arms at the top of the bend is around 37 inches.
The inside width between the top of the upright post is around 35-3/8 inches.
The inside width between the bottom of the upright post is around 36-1/2 inches.
The loader frame needs to attach to the outside of the track frame rails on the crawler.
These are around 36 inches wide to the outside of the rails so this loader is already just about the right width to fit.
The outside width between the fenders is around 35 inches so they will clear the loader arms.
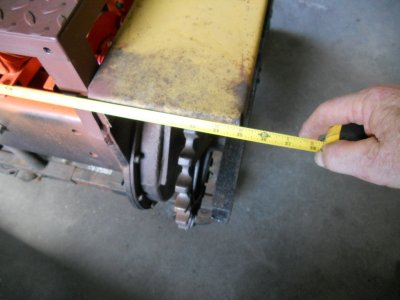