I have this small driveshaft off something ? It has a sliding yoke on the right end that has both a 1 inch and a 3/4 inch diameter shaft with a keyway in them.
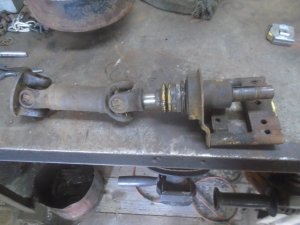
The U-joint mounting flange is removed from the left end of the driveshaft.
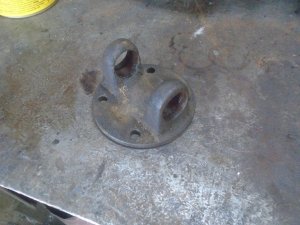
I want to fasten this mounting flange to the center of the brake drum on the back of the transmission but I'll need a spacer to clear the bolt in the center that holds the drum onto the transmission.
I have already pressed the studs out of the drum.
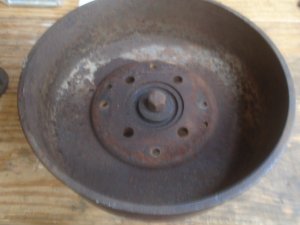
This piece of aluminum is just big enough diameter to clear the studs in the drum.
I have turned it down to leave a lip that fits into the counter-bore in the center of the drum.
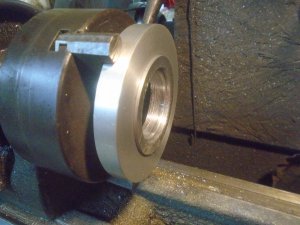
Then I turn it around and machine a counter-bore that the U-joint flange fits into.
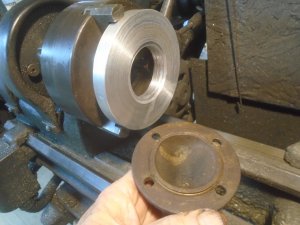
The holes are drilled out and counter-board in the spacer so it fits over the studs and can be bolted down.
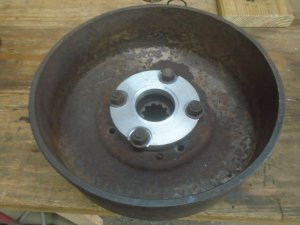
I've had to notch out four places around the U-joint flange to clear the nuts on the studs. The first hole is drilled and tapped for the studs to fasten the U-joint flange in place.
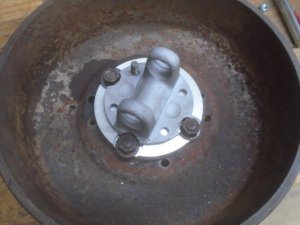
The finished U-joint flange is mounted to the drum.
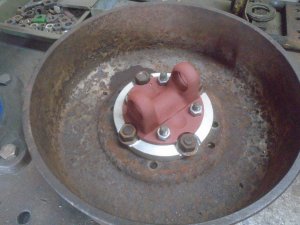
I'm going to take just the end piece with the sliding joint and it will be mounted onto the flange on the drum.
This gives me one end of a driveshaft with either a 1 inch or 3/4 inch shaft that should be easy enough to adapt to the model-T rear axle.
This is the length of the shaft when closed.
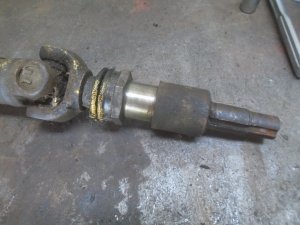
And the length when fully open.
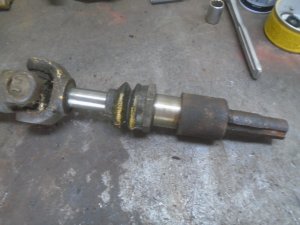
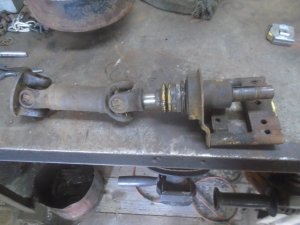
The U-joint mounting flange is removed from the left end of the driveshaft.
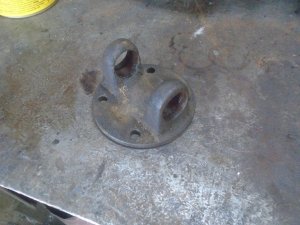
I want to fasten this mounting flange to the center of the brake drum on the back of the transmission but I'll need a spacer to clear the bolt in the center that holds the drum onto the transmission.
I have already pressed the studs out of the drum.
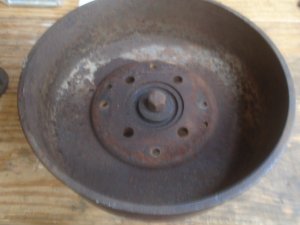
This piece of aluminum is just big enough diameter to clear the studs in the drum.
I have turned it down to leave a lip that fits into the counter-bore in the center of the drum.
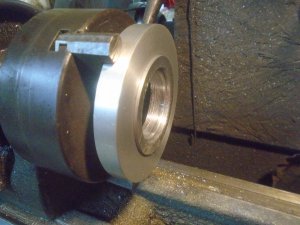
Then I turn it around and machine a counter-bore that the U-joint flange fits into.
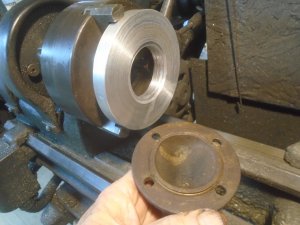
The holes are drilled out and counter-board in the spacer so it fits over the studs and can be bolted down.
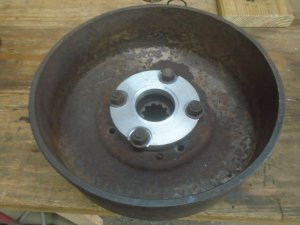
I've had to notch out four places around the U-joint flange to clear the nuts on the studs. The first hole is drilled and tapped for the studs to fasten the U-joint flange in place.
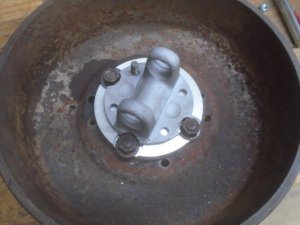
The finished U-joint flange is mounted to the drum.
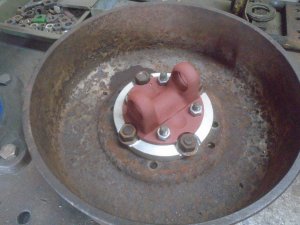
I'm going to take just the end piece with the sliding joint and it will be mounted onto the flange on the drum.
This gives me one end of a driveshaft with either a 1 inch or 3/4 inch shaft that should be easy enough to adapt to the model-T rear axle.
This is the length of the shaft when closed.
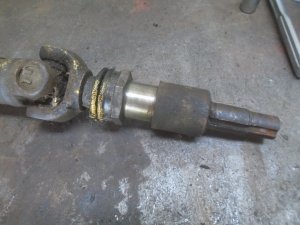
And the length when fully open.
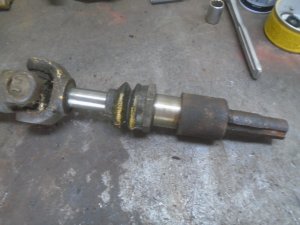
Last edited: