May be I already explained this previously but anyway, lately I found out that my hitch is not letting the snowblower sitting properly on the ground. The scraper blade is touching at the back instead of the front. This leaves a lot of snow on the ground and sometimes it causes the blower to "climb" on snowbanks instead of ripping through it.
I was looking for a while now the height of the main pivot pin from the ground. Seems I did not evaluate this properly and this causes my problems. A member of MTF was nice enough to provide me the measurement measured on his 445 resting on concrete with the blade down on float.
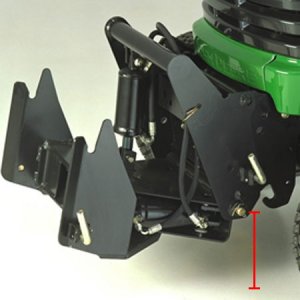
Since there are multiple versions of this hitch, there can be variations to this height. Here is what I know so far, measure taken from the ground to the center of the pin.
BM17347 : 425, 445, 455 : 7.5" -- This is the hitch I used. I had the height at 6.25" and it makes quite a difference!
BM18120 : F900 series
BM18121 : 318, 322, 332 : 8.5"
BM18122 : 420, 430 : 6.5" (at least for the 430 which has an extension frame. 420 not sure.)
BM19782 : x465-x595, X700 series : 7.75"
BM20921 : 2210
LVB24898 : 4010, 4100, 4110, 4115
I will probably modify my hitch this weekend to fix this mistake. Should be relatively easy, drill higher, cut the hitch under this new hole and make a new bracket for the top of the hydraulic cylinder.
I was looking for a while now the height of the main pivot pin from the ground. Seems I did not evaluate this properly and this causes my problems. A member of MTF was nice enough to provide me the measurement measured on his 445 resting on concrete with the blade down on float.
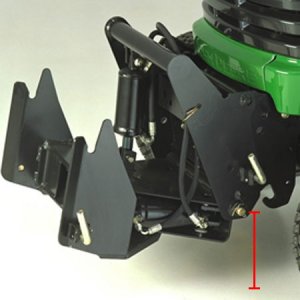
Since there are multiple versions of this hitch, there can be variations to this height. Here is what I know so far, measure taken from the ground to the center of the pin.
BM17347 : 425, 445, 455 : 7.5" -- This is the hitch I used. I had the height at 6.25" and it makes quite a difference!
BM18120 : F900 series
BM18121 : 318, 322, 332 : 8.5"
BM18122 : 420, 430 : 6.5" (at least for the 430 which has an extension frame. 420 not sure.)
BM19782 : x465-x595, X700 series : 7.75"
BM20921 : 2210
LVB24898 : 4010, 4100, 4110, 4115
I will probably modify my hitch this weekend to fix this mistake. Should be relatively easy, drill higher, cut the hitch under this new hole and make a new bracket for the top of the hydraulic cylinder.