Worked on getting the linkage made up for operating the mower clutch today.
To operate the mower clutch, I'm using the same lever that I had originally made up for tensioning the flat belt.
This is the position of the lever with the clutch disengaged.
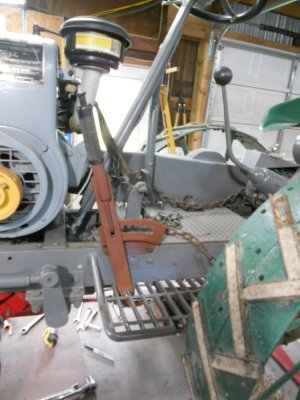
And this is with it engaged.
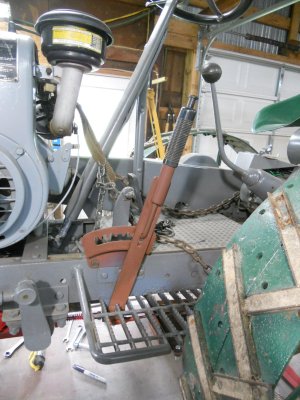
The movement on this lever is forward and backward and the movement of the clutch arm on the clutch case is side to side.
So first I made up this shaft with two arms on it.
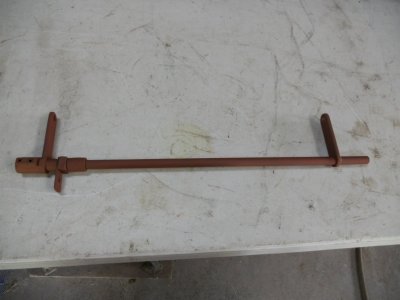
This is mounted on the right side and fastened to the mower drive unit mounting brackets.
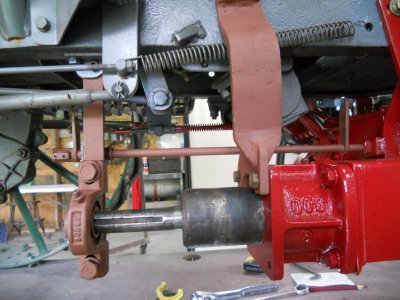
I'm using a triangular shaped bellcrank to change the forward and backward movement of the clutch lever to a side to side movement.
This bellcrank is mounted under the step on the left side.
You can see a linkage rod connected to the bottom of the clutch lever and going to one end of the bellcrank.
The linkage rod that is connected to the other end of the bellcrank runs over to the other side of the tractor.
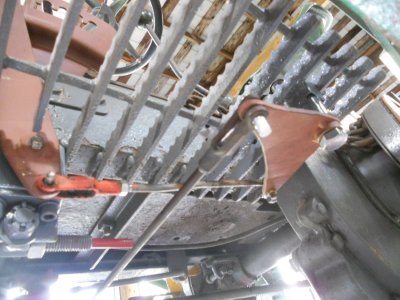
This rod coming from the bellcrank connects to this rear shaft arm.
The front arm on this shaft has a linkage rod connected to it that goes to the clutch lever on the side of the clutch case.
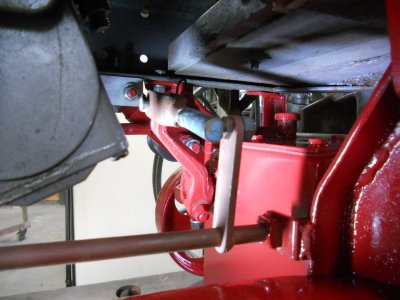
To operate the mower clutch, I'm using the same lever that I had originally made up for tensioning the flat belt.
This is the position of the lever with the clutch disengaged.
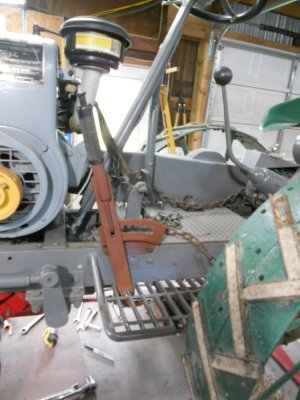
And this is with it engaged.
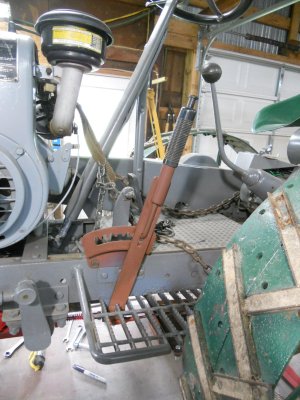
The movement on this lever is forward and backward and the movement of the clutch arm on the clutch case is side to side.
So first I made up this shaft with two arms on it.
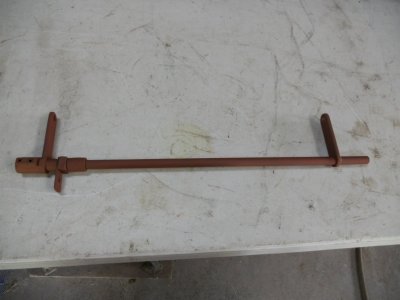
This is mounted on the right side and fastened to the mower drive unit mounting brackets.
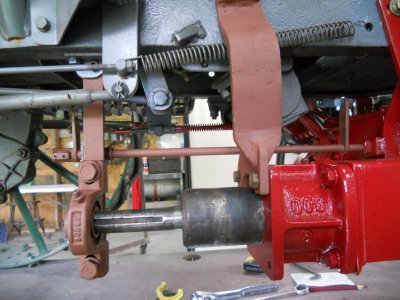
I'm using a triangular shaped bellcrank to change the forward and backward movement of the clutch lever to a side to side movement.
This bellcrank is mounted under the step on the left side.
You can see a linkage rod connected to the bottom of the clutch lever and going to one end of the bellcrank.
The linkage rod that is connected to the other end of the bellcrank runs over to the other side of the tractor.
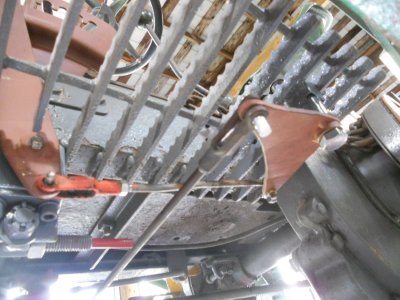
This rod coming from the bellcrank connects to this rear shaft arm.
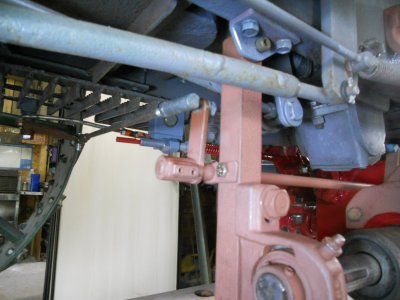
The front arm on this shaft has a linkage rod connected to it that goes to the clutch lever on the side of the clutch case.
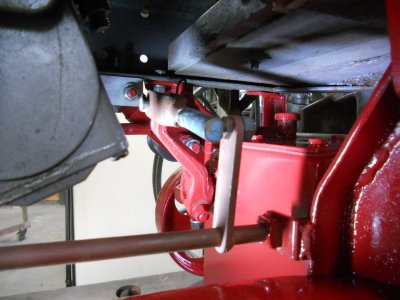