I managed to get the retaining pin to move in the rear axle.
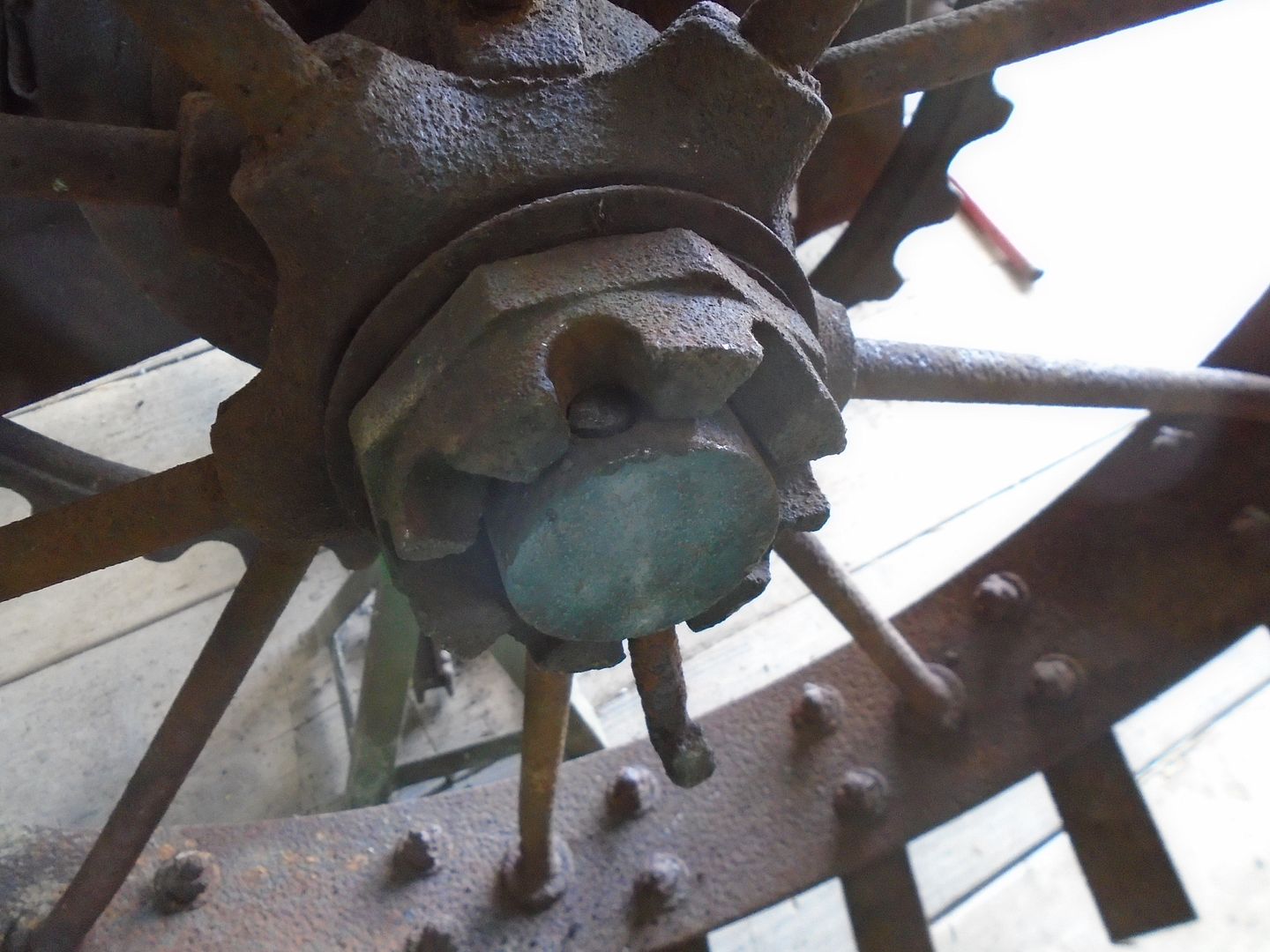
And was able to remove the spacing nut and the washers without any trouble.
This is not a threaded nut, it has three pin grooves machined into it and each one is at a different depth from the face of the nut.
You set the clearance for the ring and pinion gears and then rotate this spacer nut until one of the pin grooves lines up with the hole in the axle.
Then you put the pin in place to hold the wheel on.

This wheel has a grease cup on it and there was enough grease still inside the hub to keep it from rusting to the axle so it slid right off.
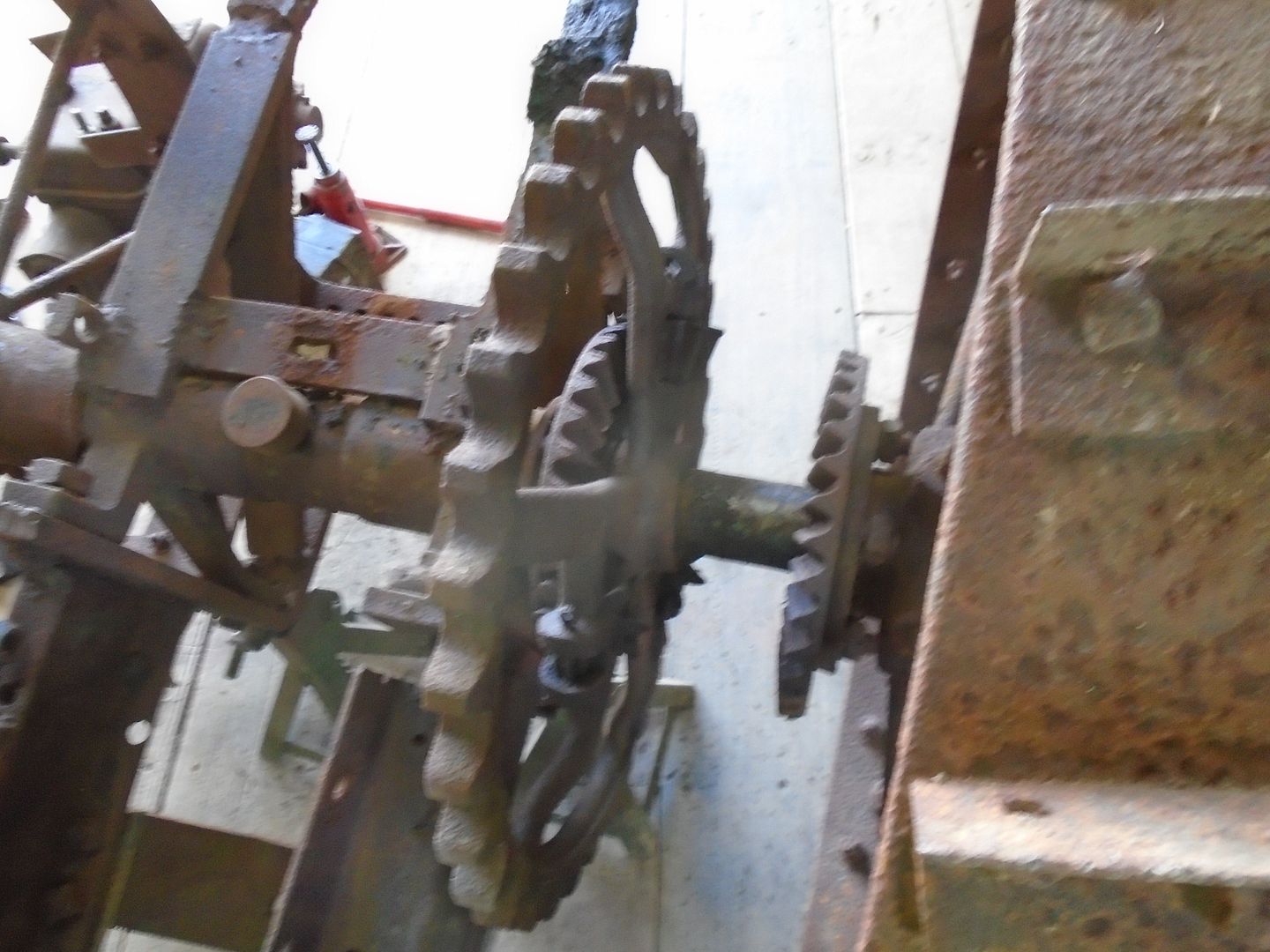
I was glad to see that none of the teeth are cracked or broken on this half of the ring gears.
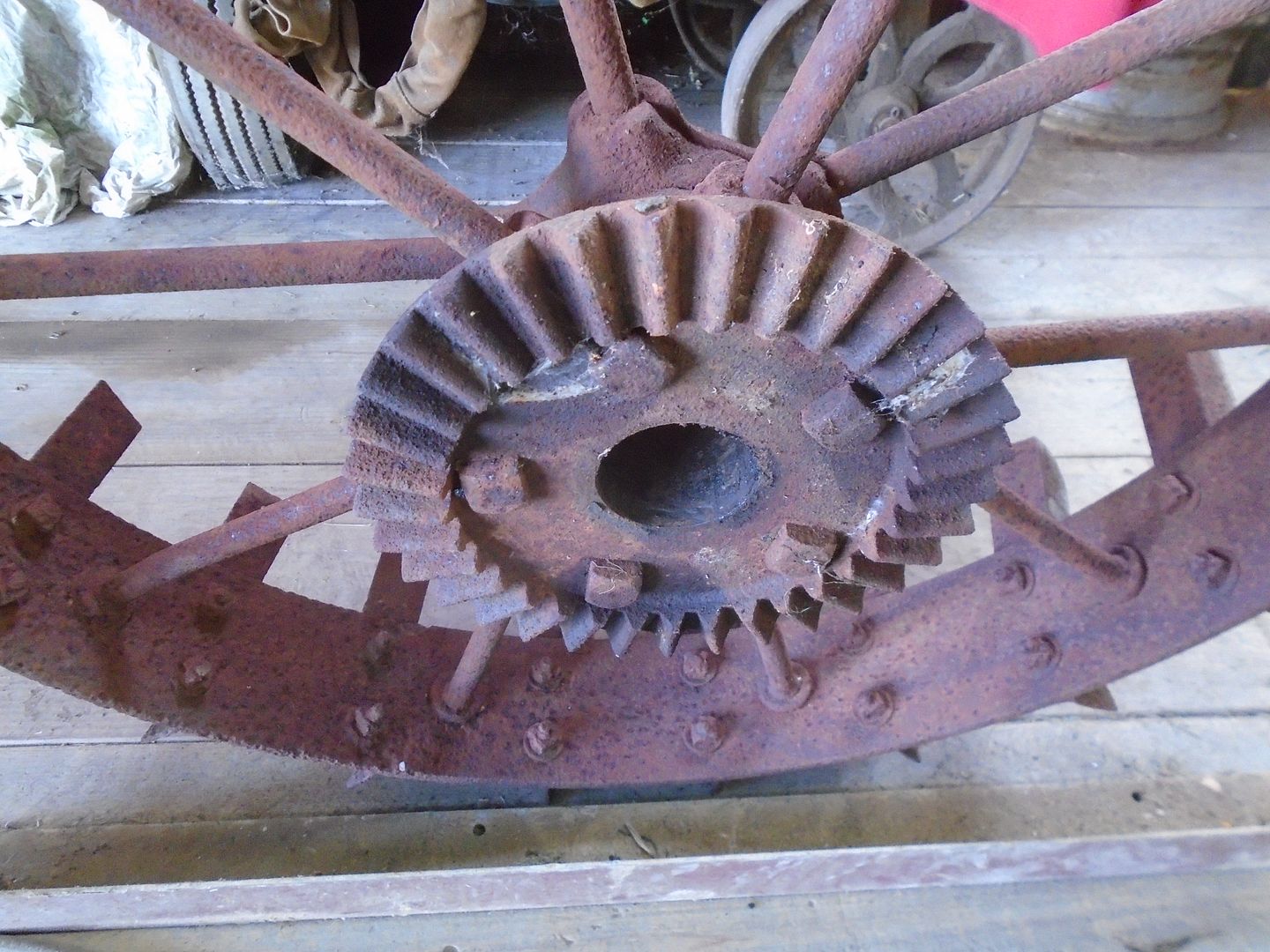
The sprocket does not have a grease fitting on it like the wheel and it took some time to get it worked loose.
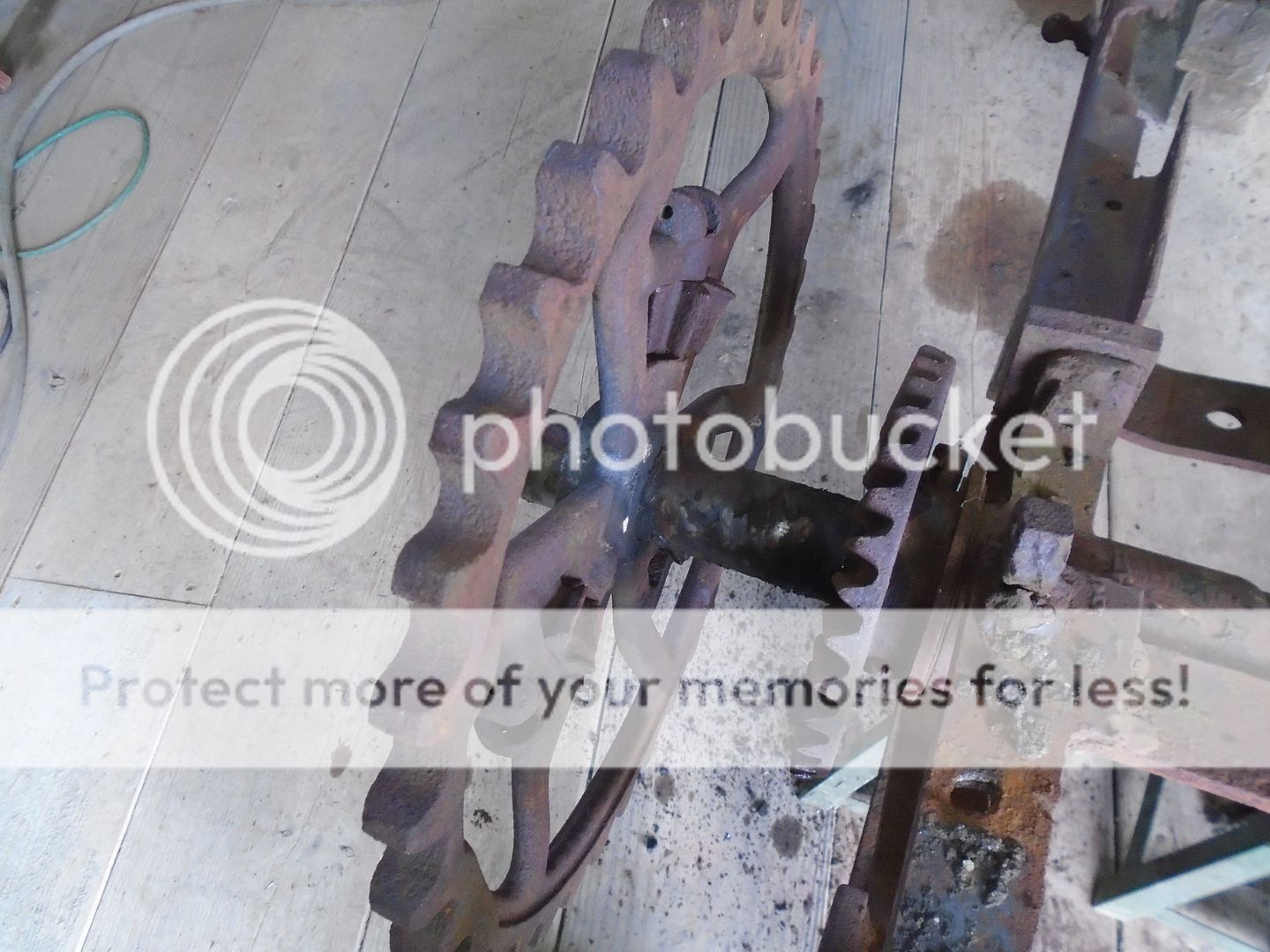
Again, I'm glad to see that there are no broken teeth on this half of the ring gear too.
The axle turns freely in the housing so this is as far down as I'm going to go with this rear end.
I'm working with cast iron that is anywhere from 94 to 96 years old and it was most likely not a high grade cast iron to start with, not like you will find in more expensive tractors and in cars.
I consider myself extremely lucky that I haven't already cracked or broken anything with all of the heating and hammering that I've been doing on it.
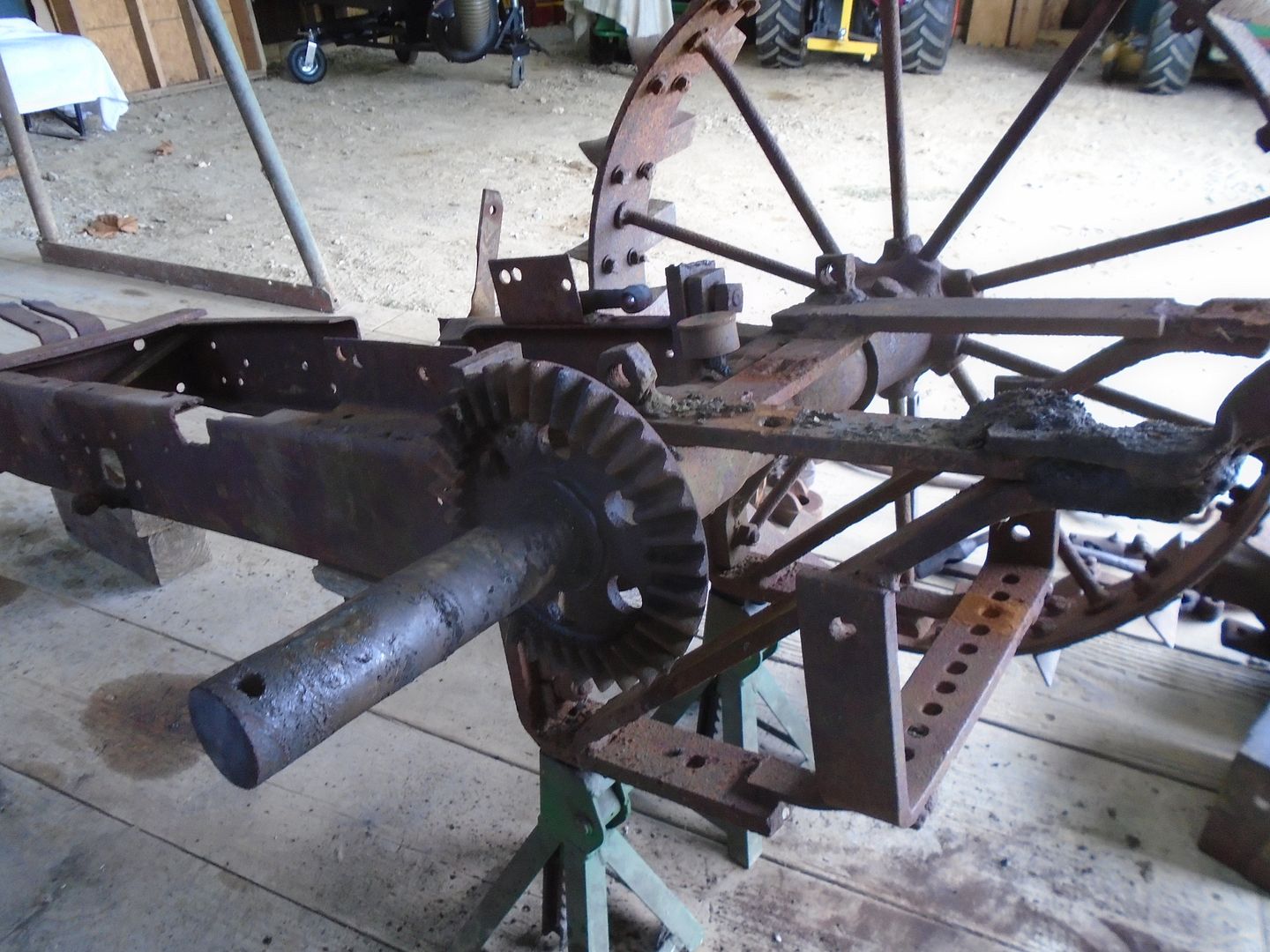
I clamped the sprocket up in the vice to work on getting the pinion gears loose.
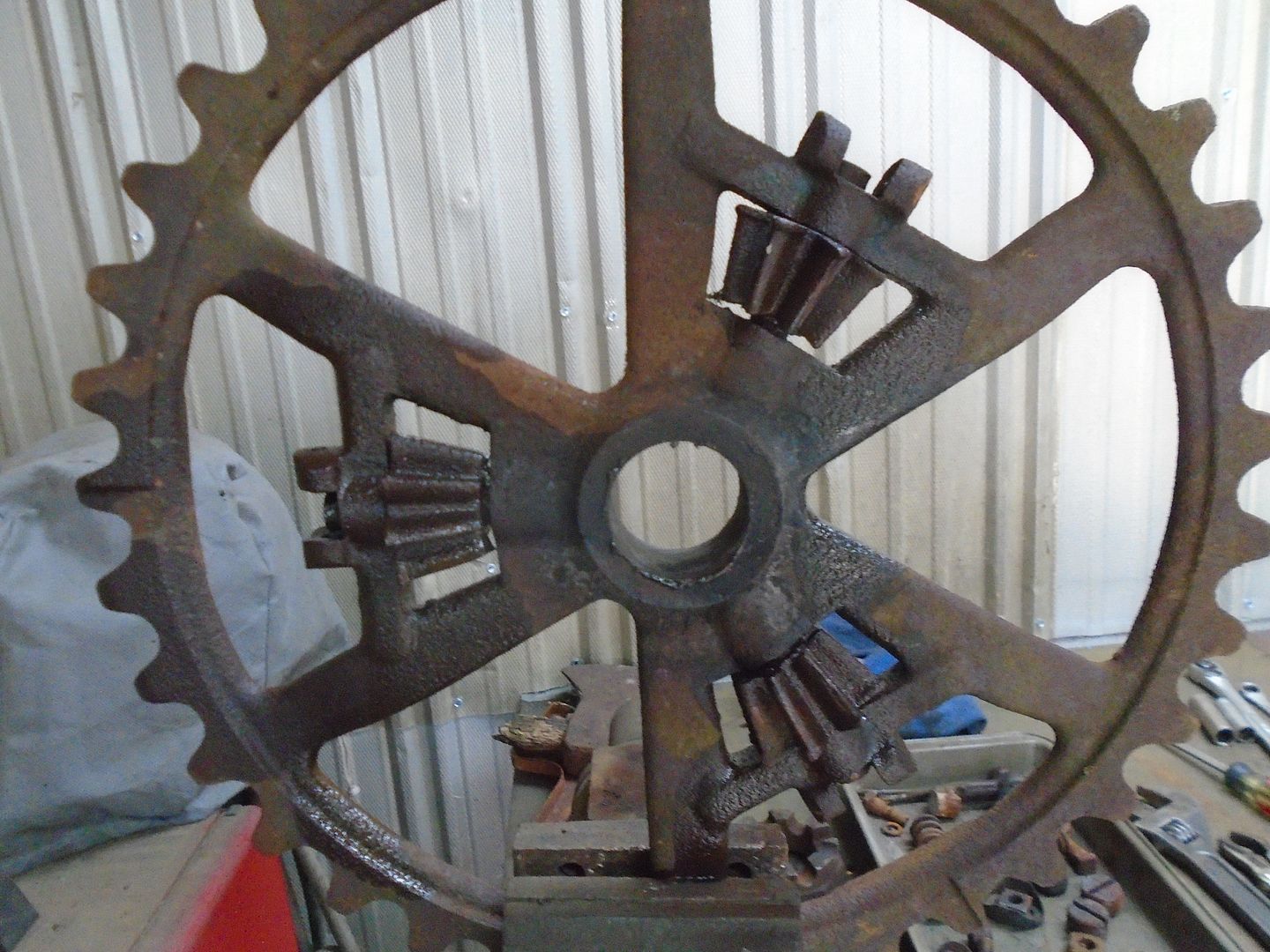
The pin that holds them in place is put into a blind hole so I can't get to the other end of the pin to use a punch to get them out.
I have gotten the gears to rotate but the pins are rusted into the gears so it is the pins that are rotating in the housing and not the gears rotating on the pins.
I have decided to leave them this way.
These pinion gears only rotate when the tractor is making a turn and the inside wheel needs to go a little slower then the outside wheel.
The pinion gears themselves don't rotate very much at all to allow the tractor to make the turn and with this tractor just being taken to tractor shows, these gear pins will never wear the holes out in the casting.
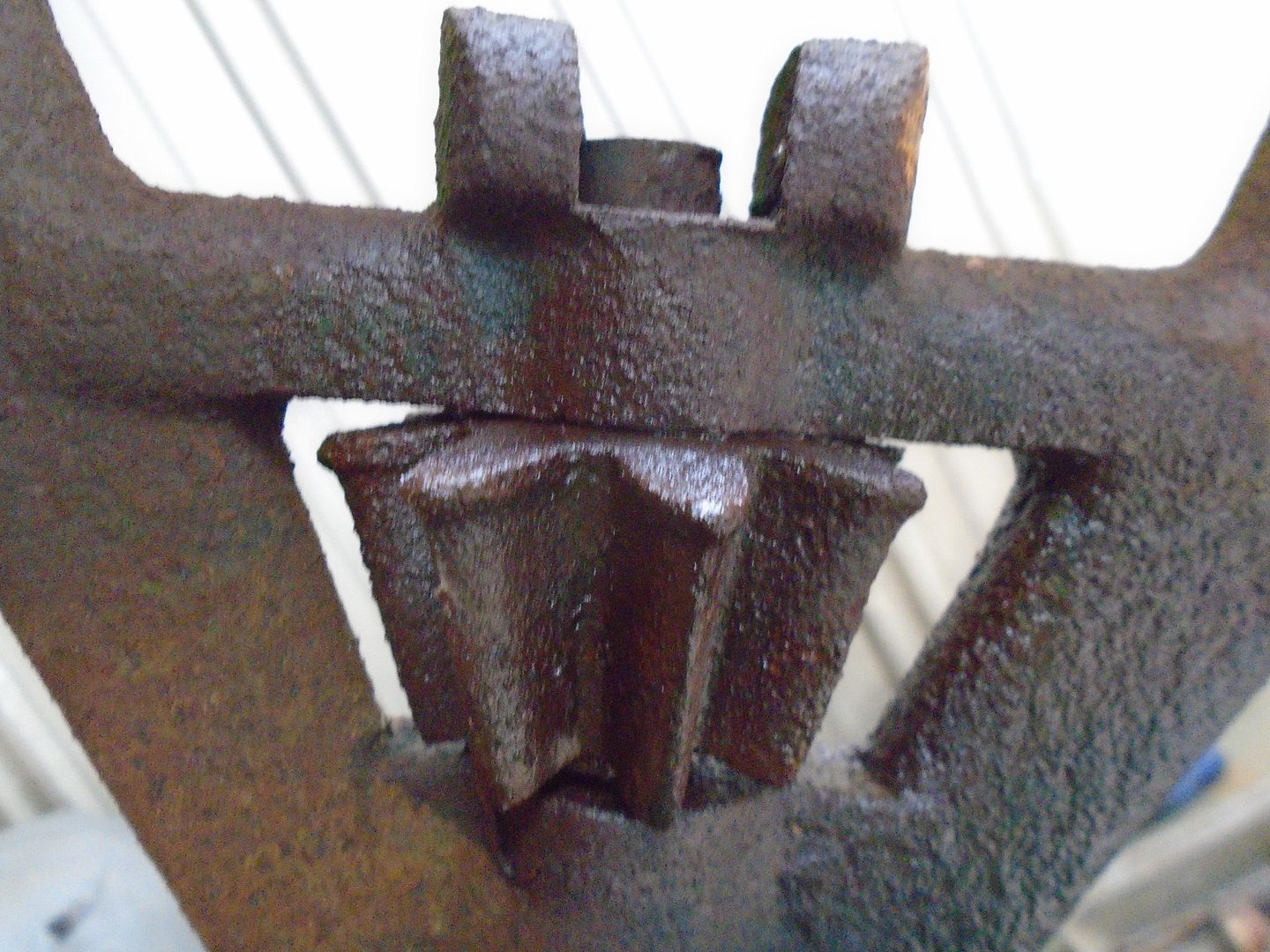
I was also glad to see that the cap came off the grease cup on the axle housing without any problem.
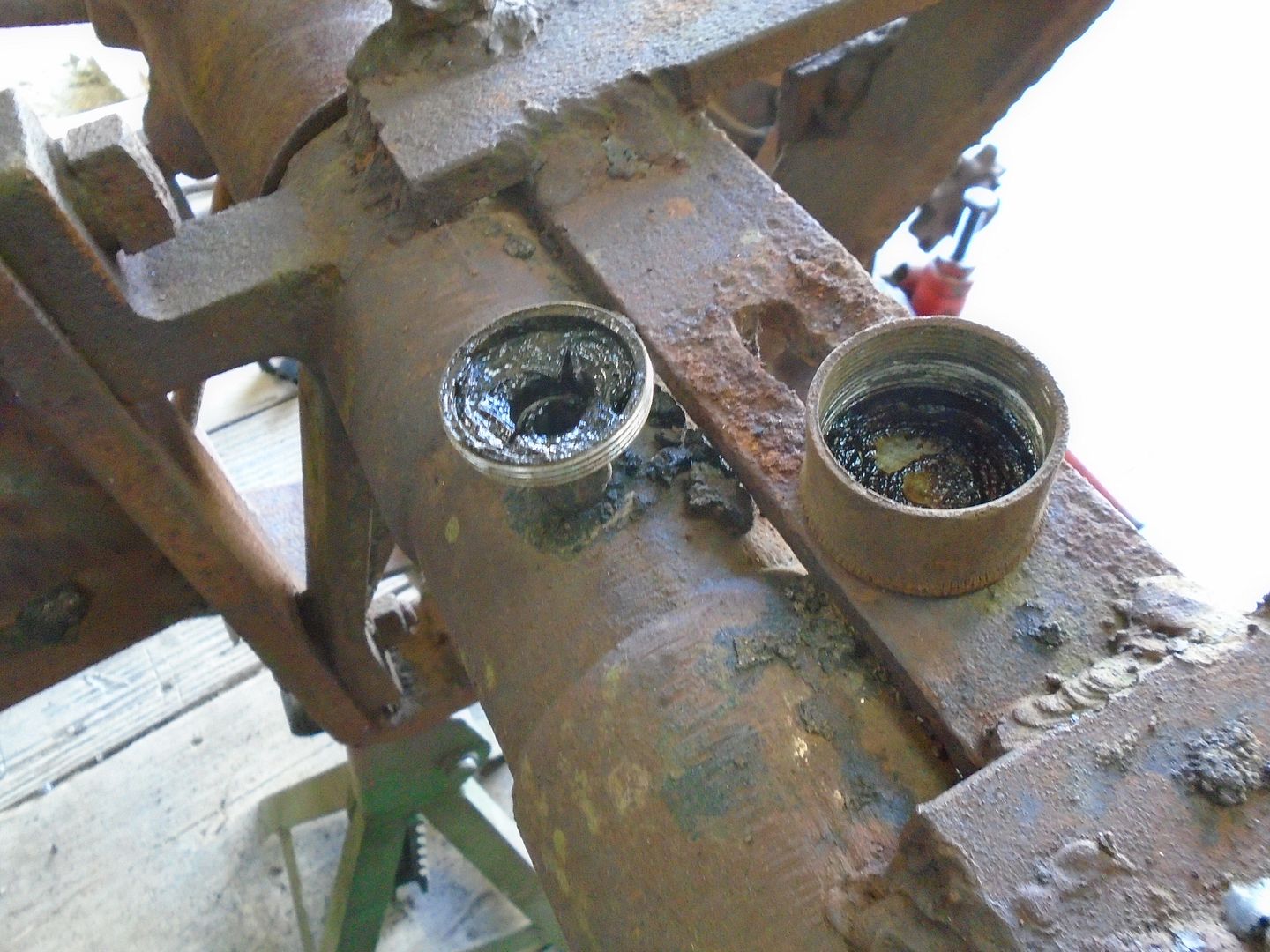
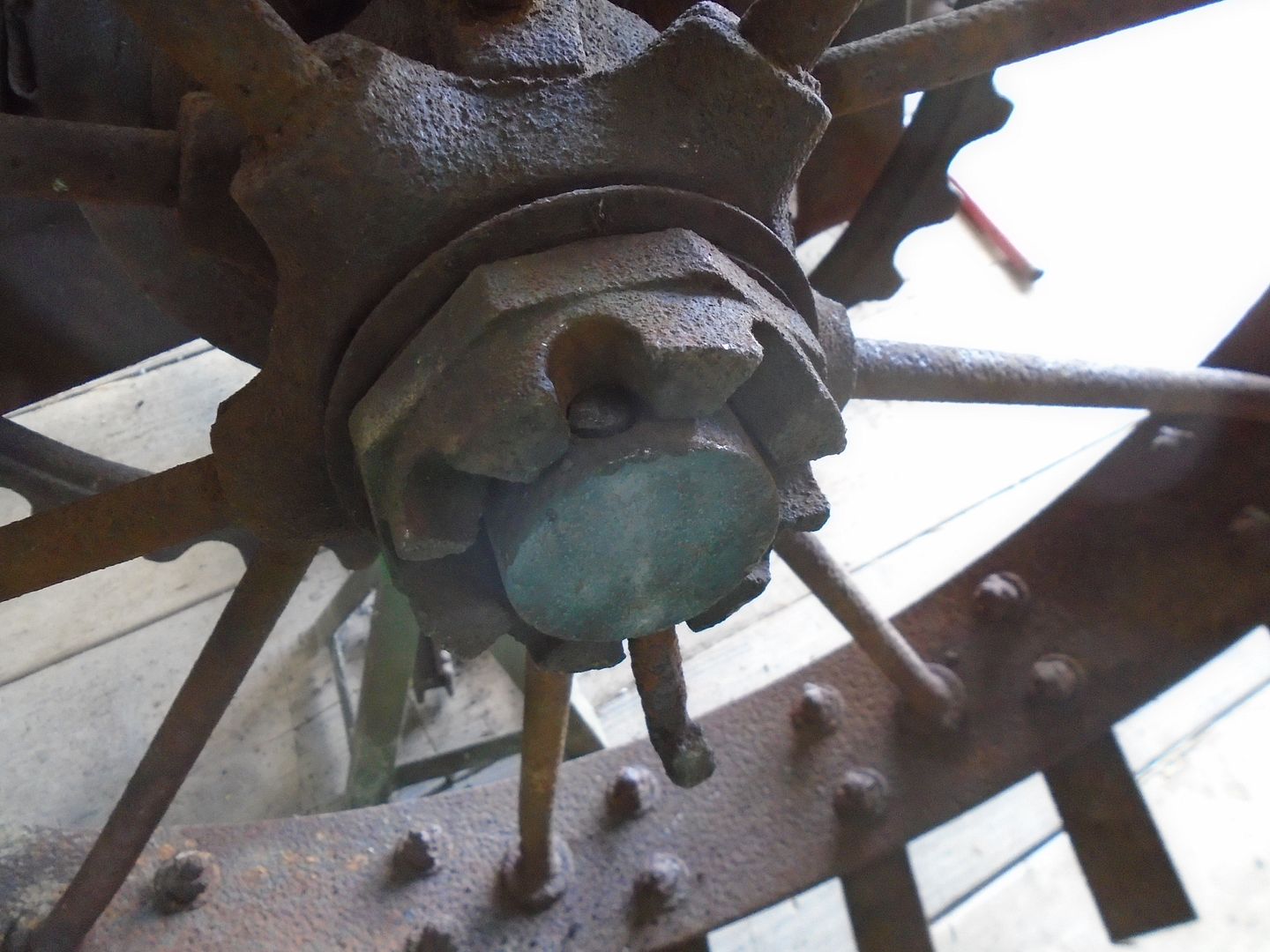
And was able to remove the spacing nut and the washers without any trouble.
This is not a threaded nut, it has three pin grooves machined into it and each one is at a different depth from the face of the nut.
You set the clearance for the ring and pinion gears and then rotate this spacer nut until one of the pin grooves lines up with the hole in the axle.
Then you put the pin in place to hold the wheel on.

This wheel has a grease cup on it and there was enough grease still inside the hub to keep it from rusting to the axle so it slid right off.
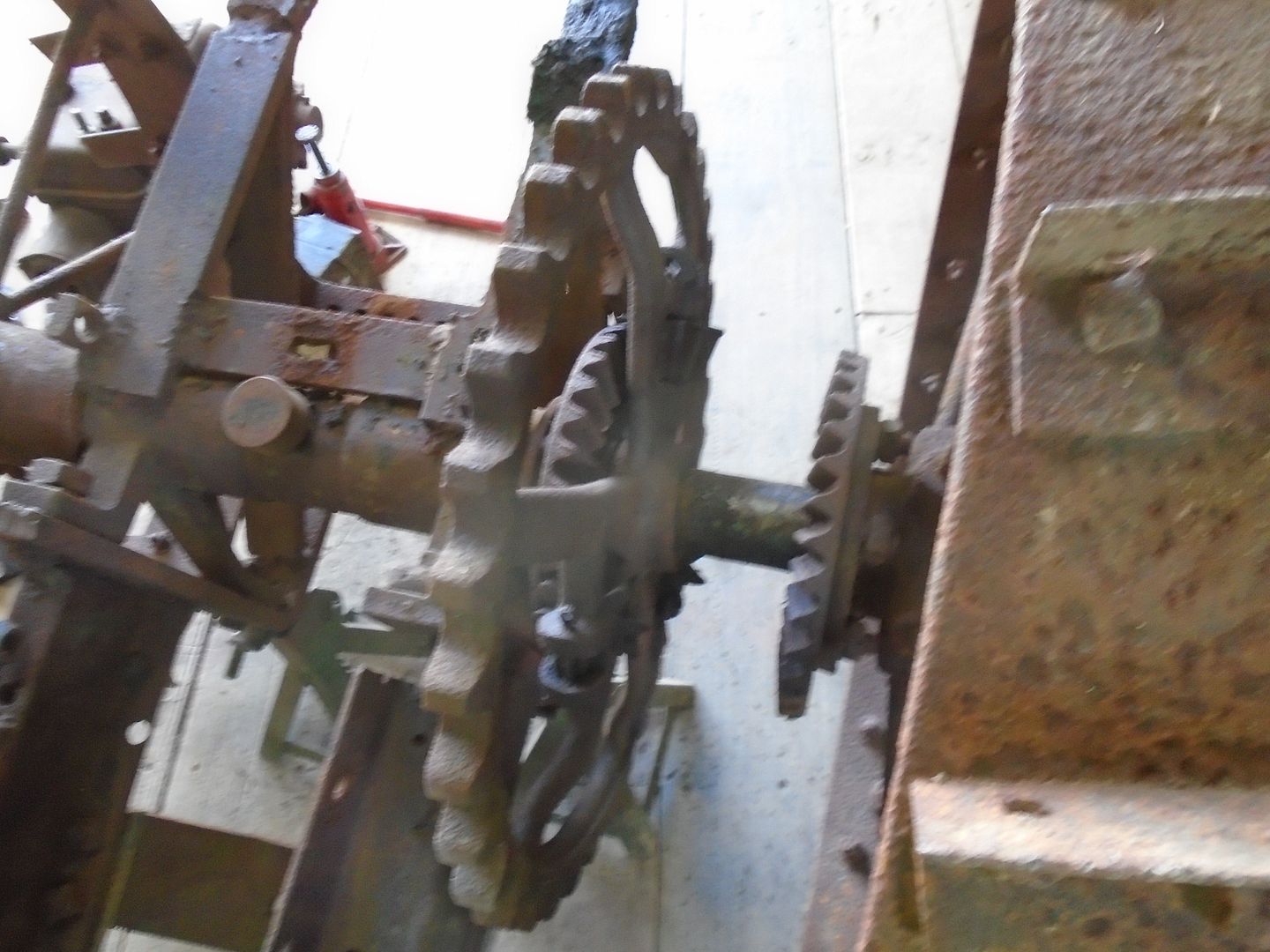
I was glad to see that none of the teeth are cracked or broken on this half of the ring gears.
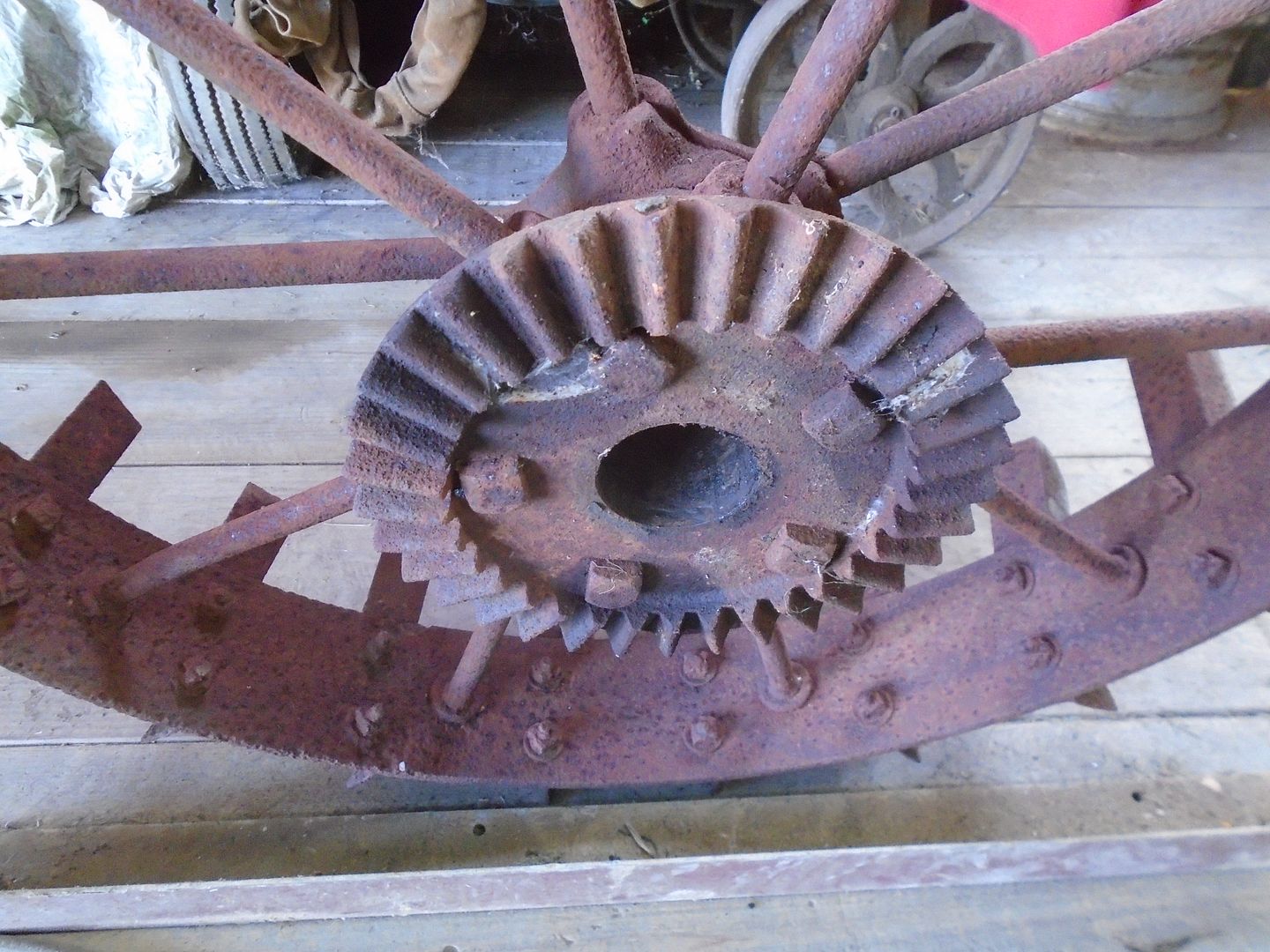
The sprocket does not have a grease fitting on it like the wheel and it took some time to get it worked loose.
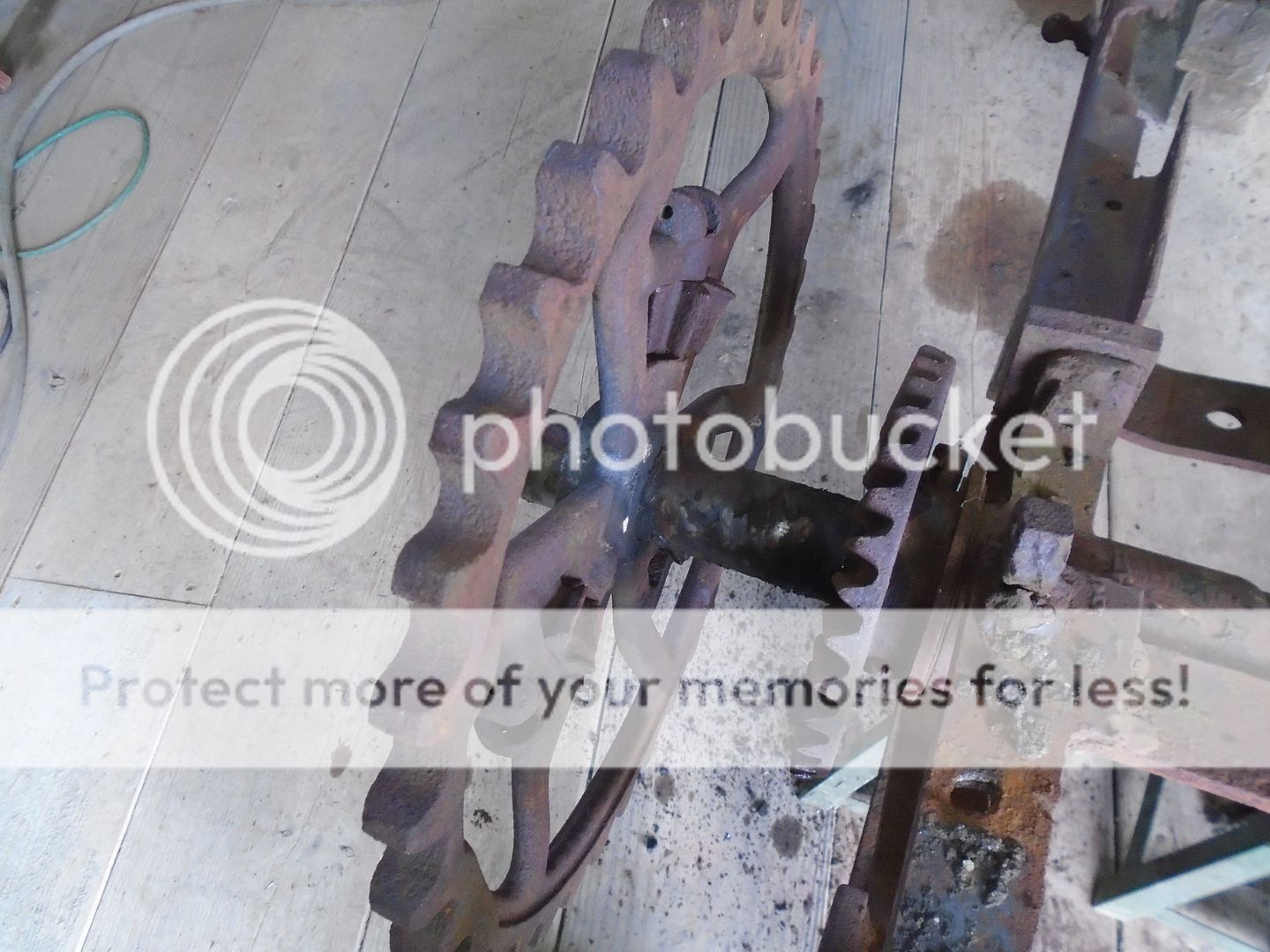
Again, I'm glad to see that there are no broken teeth on this half of the ring gear too.
The axle turns freely in the housing so this is as far down as I'm going to go with this rear end.
I'm working with cast iron that is anywhere from 94 to 96 years old and it was most likely not a high grade cast iron to start with, not like you will find in more expensive tractors and in cars.
I consider myself extremely lucky that I haven't already cracked or broken anything with all of the heating and hammering that I've been doing on it.
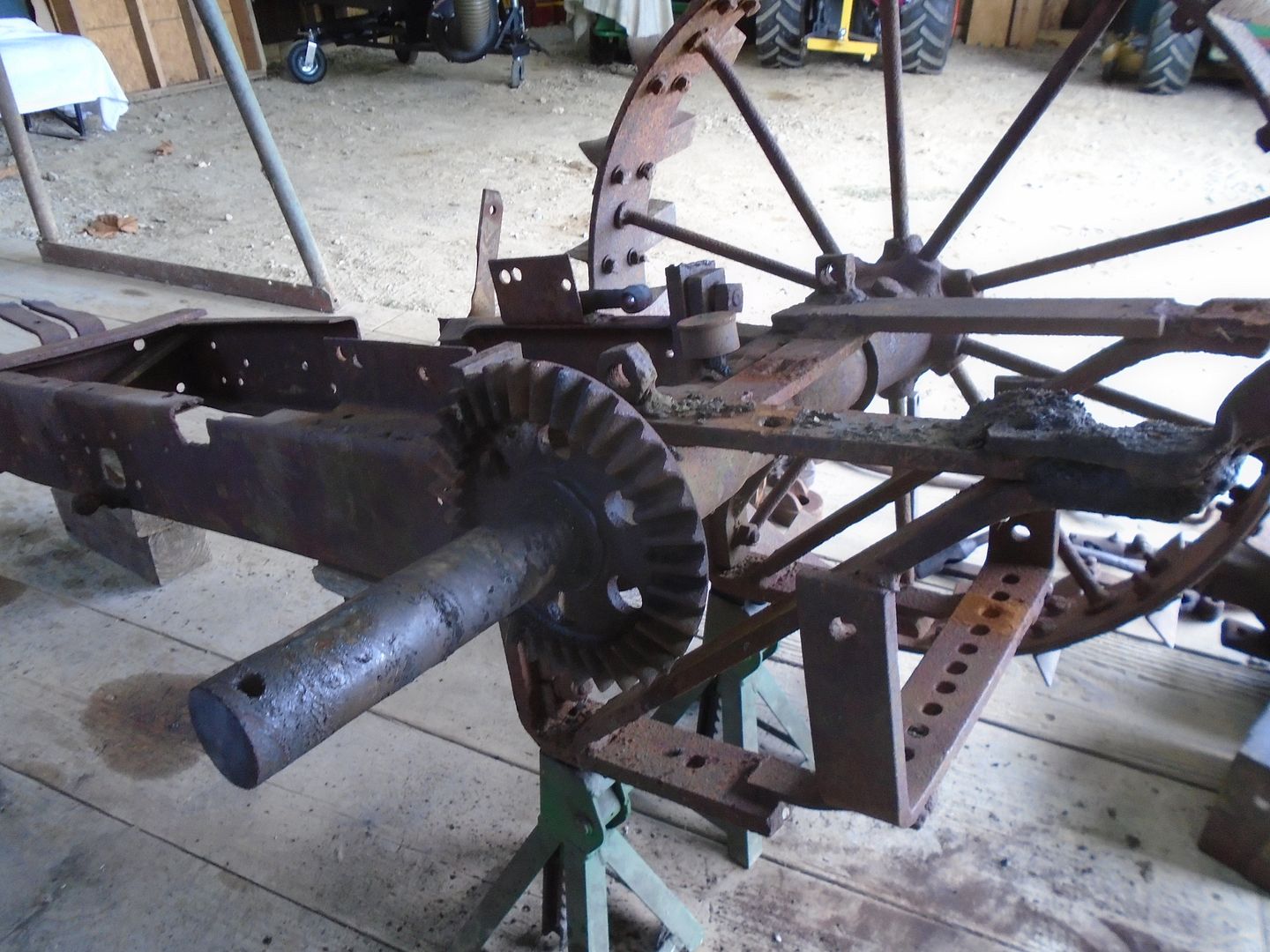
I clamped the sprocket up in the vice to work on getting the pinion gears loose.
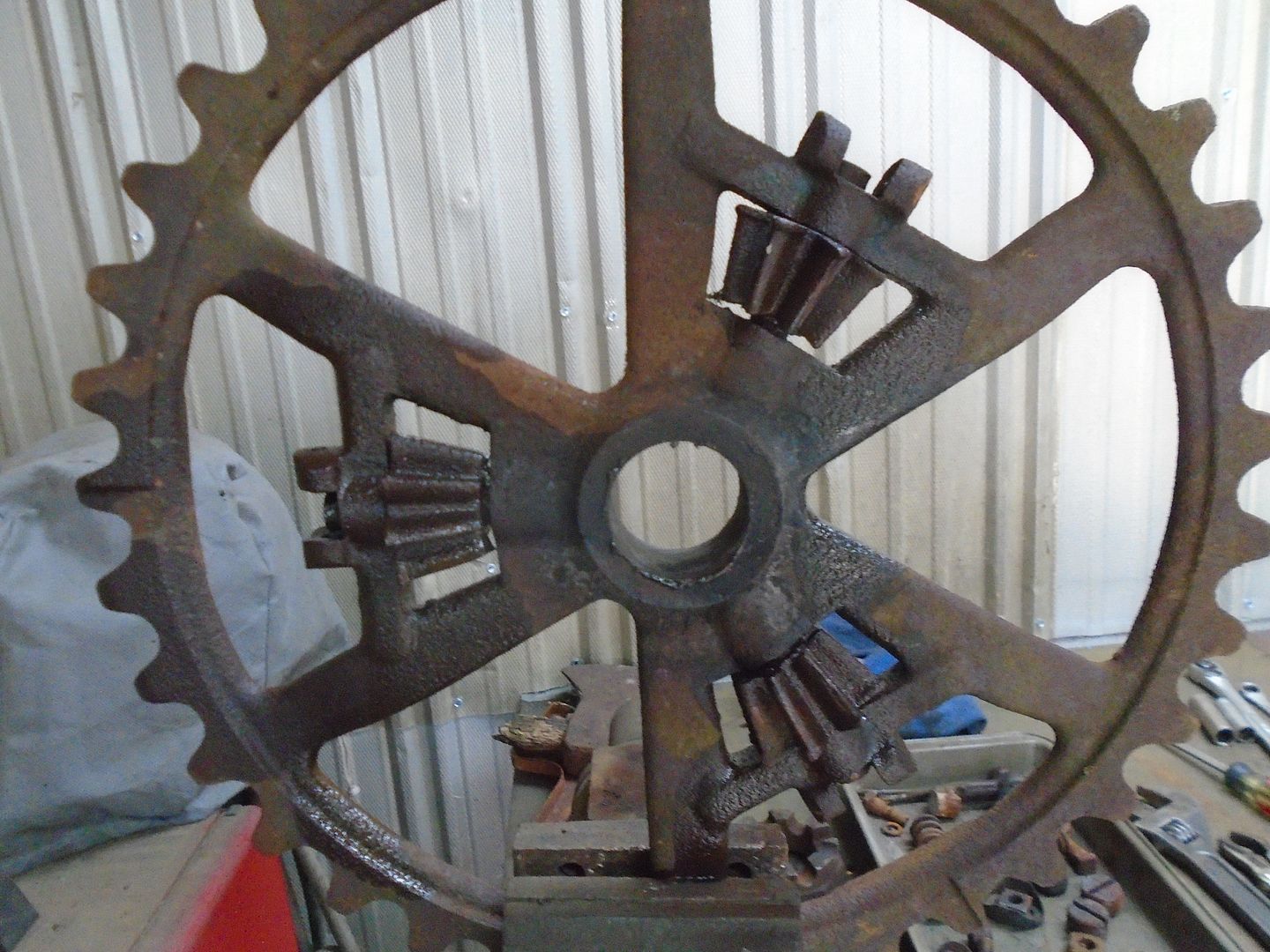
The pin that holds them in place is put into a blind hole so I can't get to the other end of the pin to use a punch to get them out.
I have gotten the gears to rotate but the pins are rusted into the gears so it is the pins that are rotating in the housing and not the gears rotating on the pins.
I have decided to leave them this way.
These pinion gears only rotate when the tractor is making a turn and the inside wheel needs to go a little slower then the outside wheel.
The pinion gears themselves don't rotate very much at all to allow the tractor to make the turn and with this tractor just being taken to tractor shows, these gear pins will never wear the holes out in the casting.
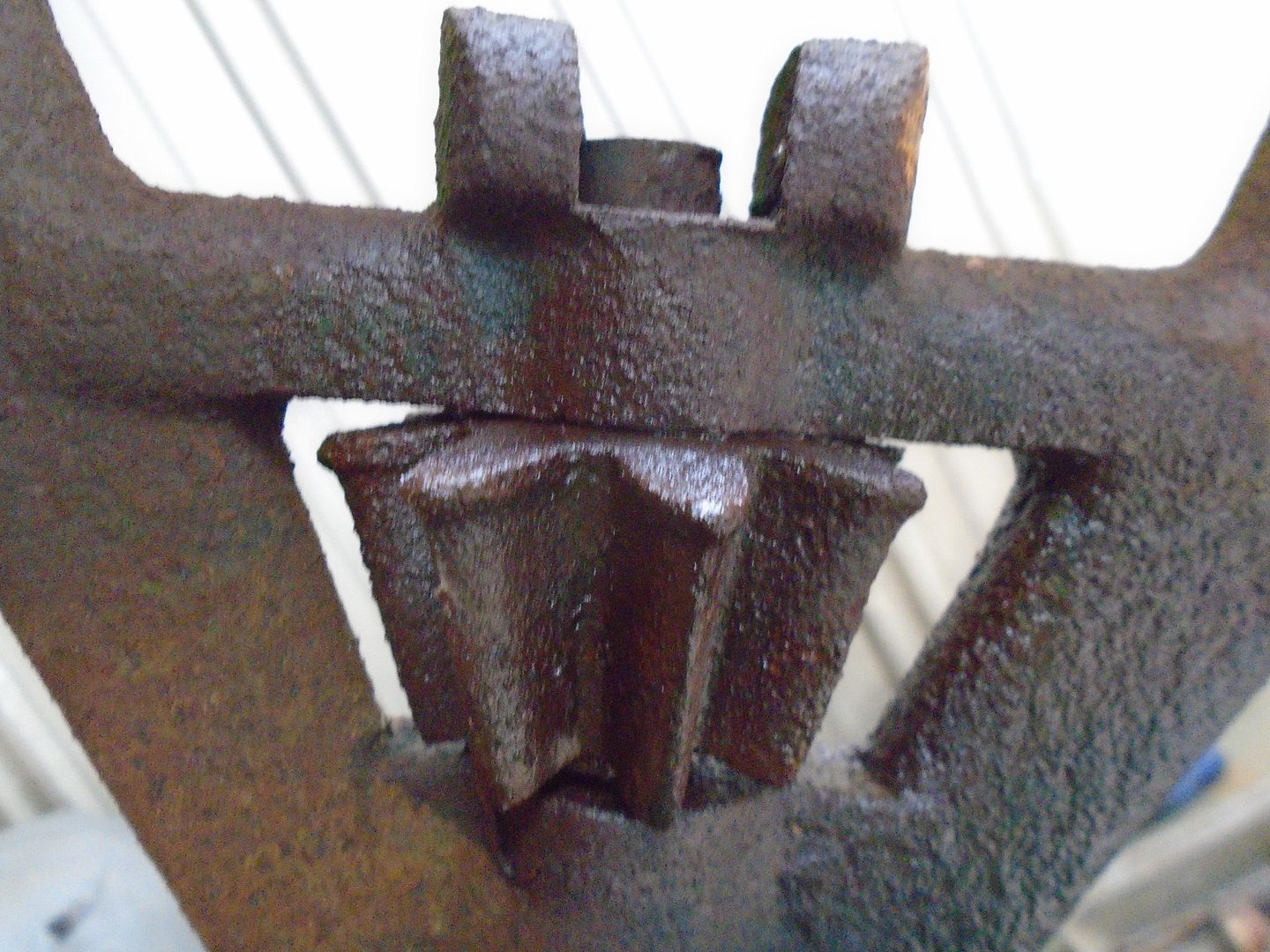
I was also glad to see that the cap came off the grease cup on the axle housing without any problem.
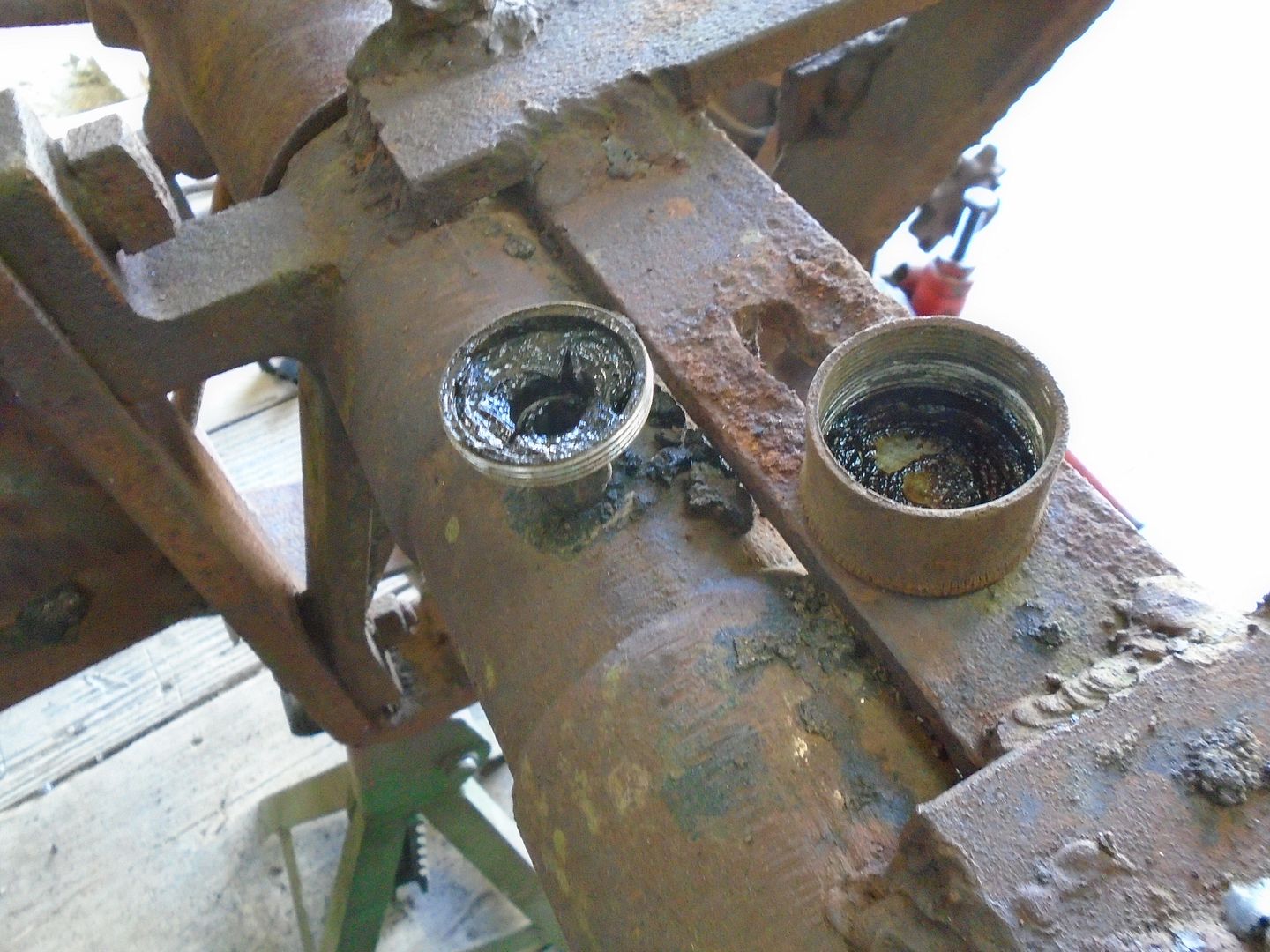