The gouged out area of the bore in the ring gear is built up with brazing rod.
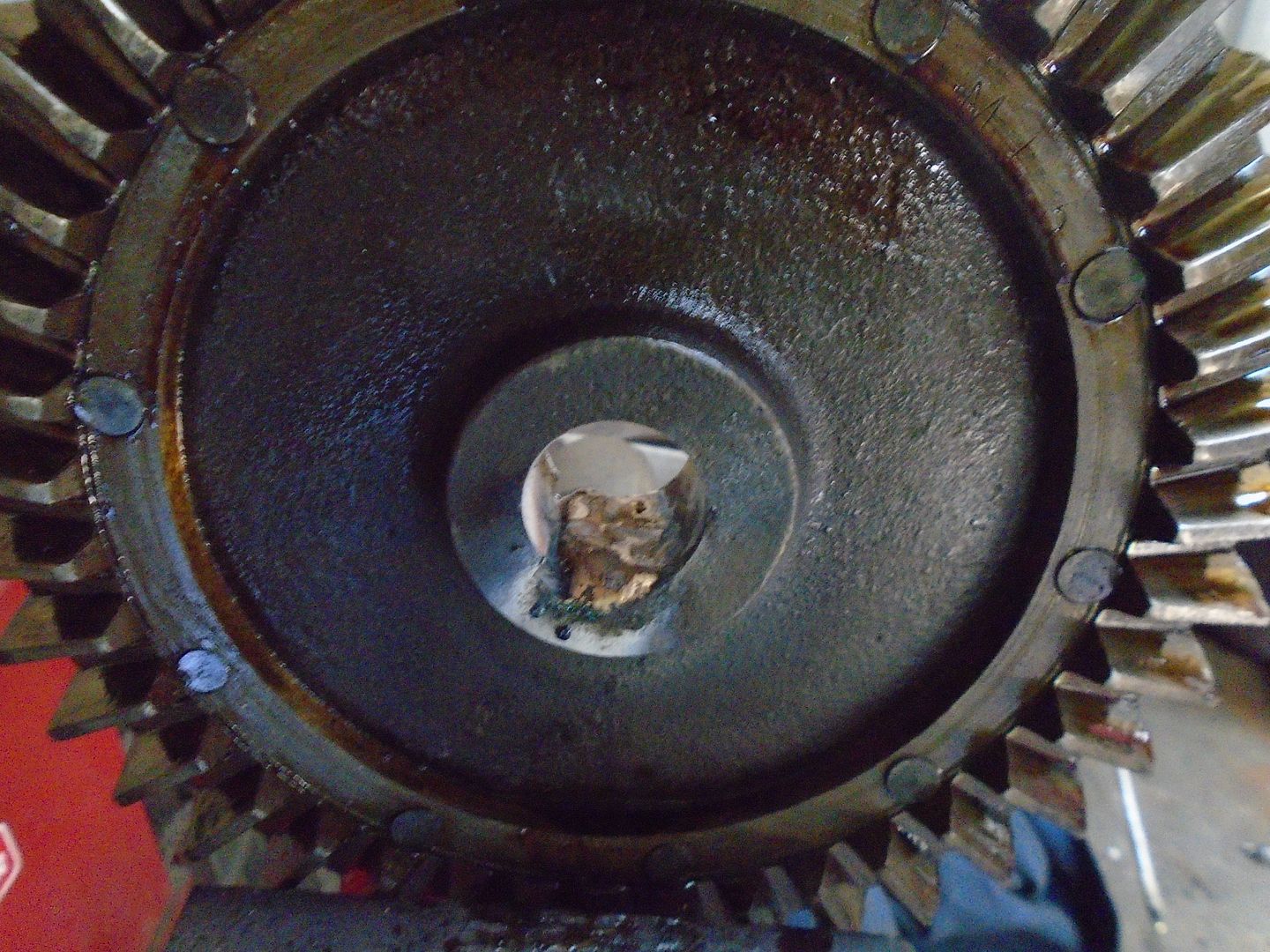
The shaft is built up with brazing rod also.
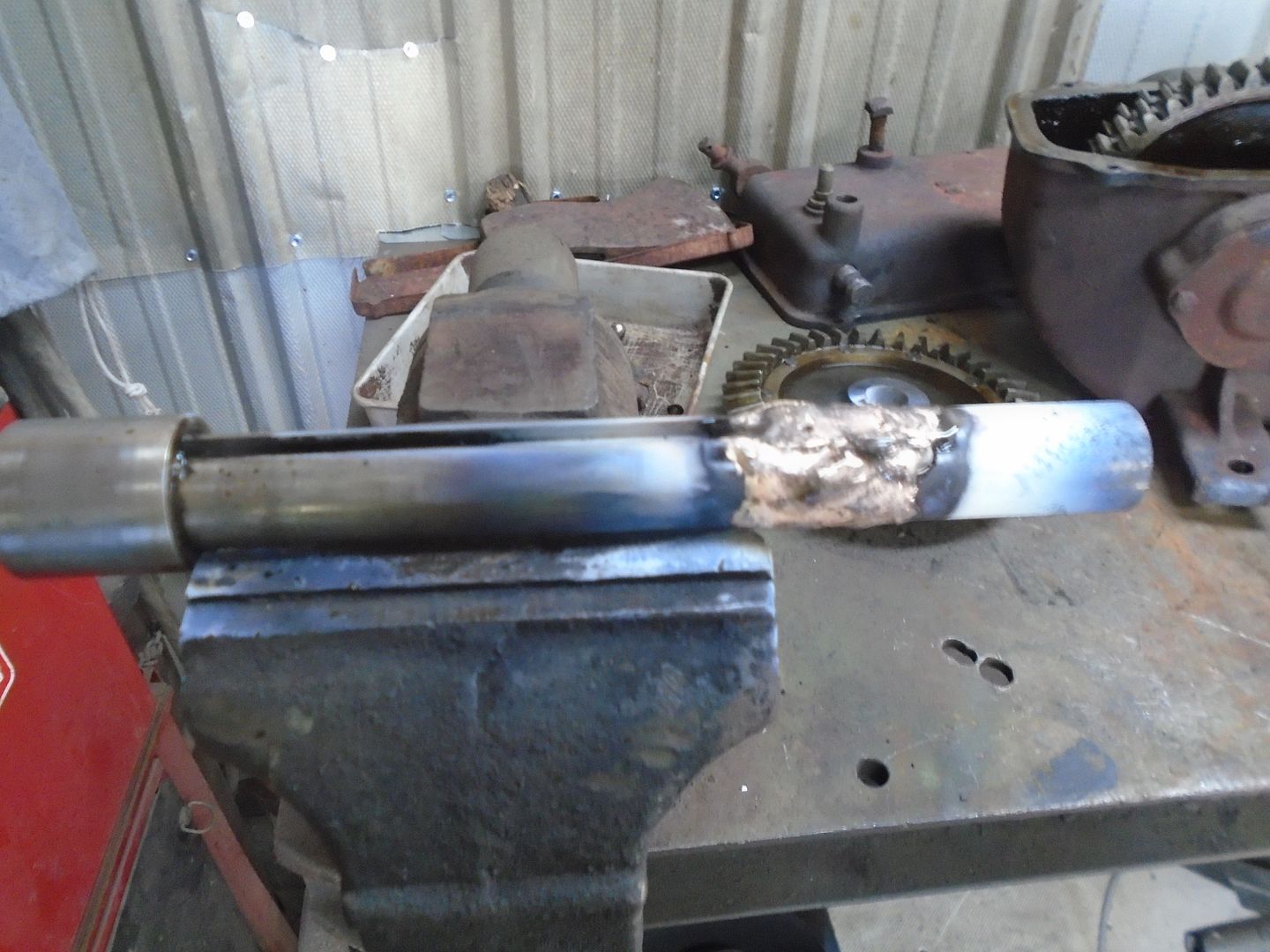
I chucked the ring gear up in the lathe to bore it out to size.
The hole in the ring gear was warn a little so I machined it .010 oversize.
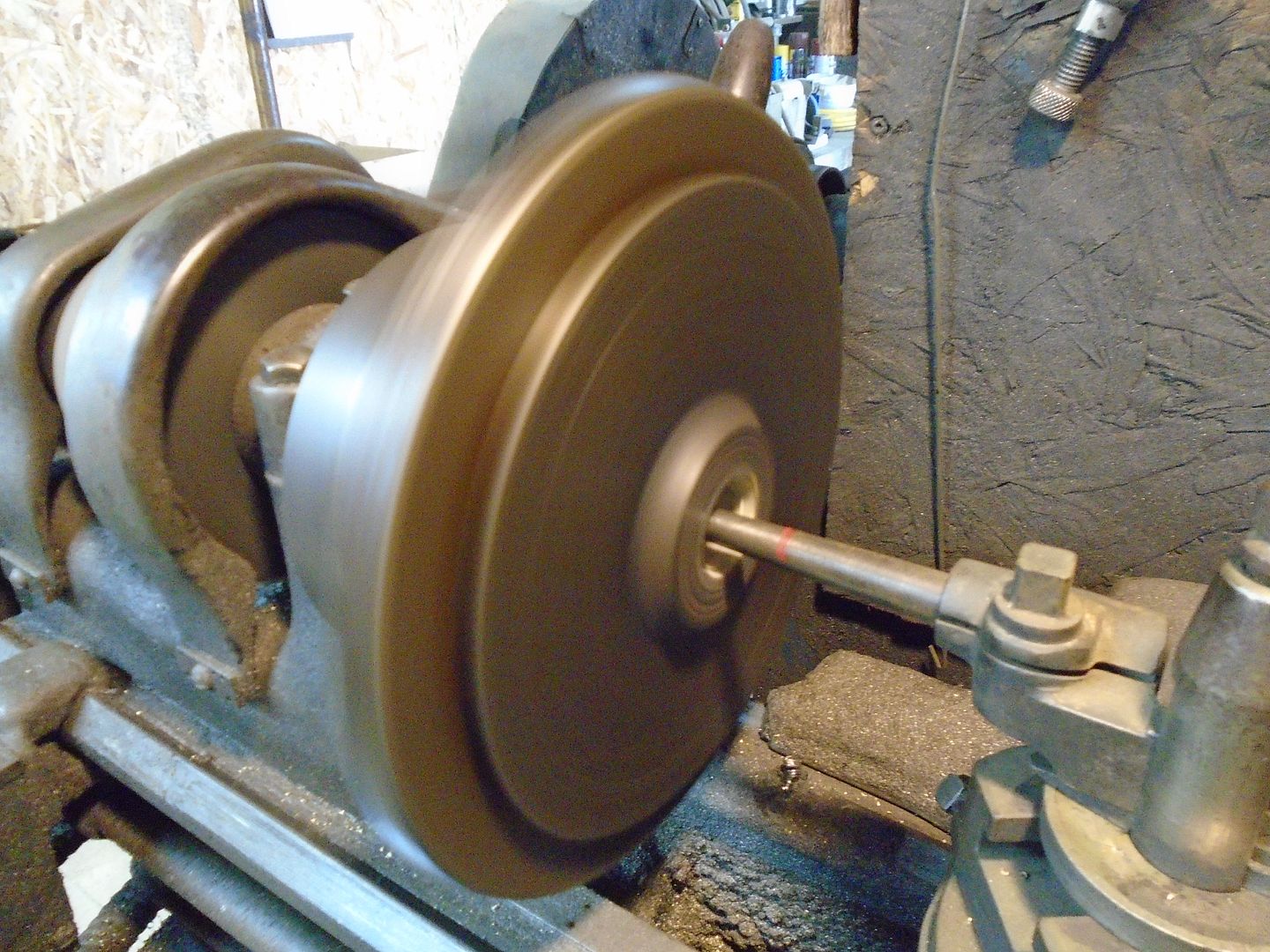
Then the key is re-cut using a key broach.
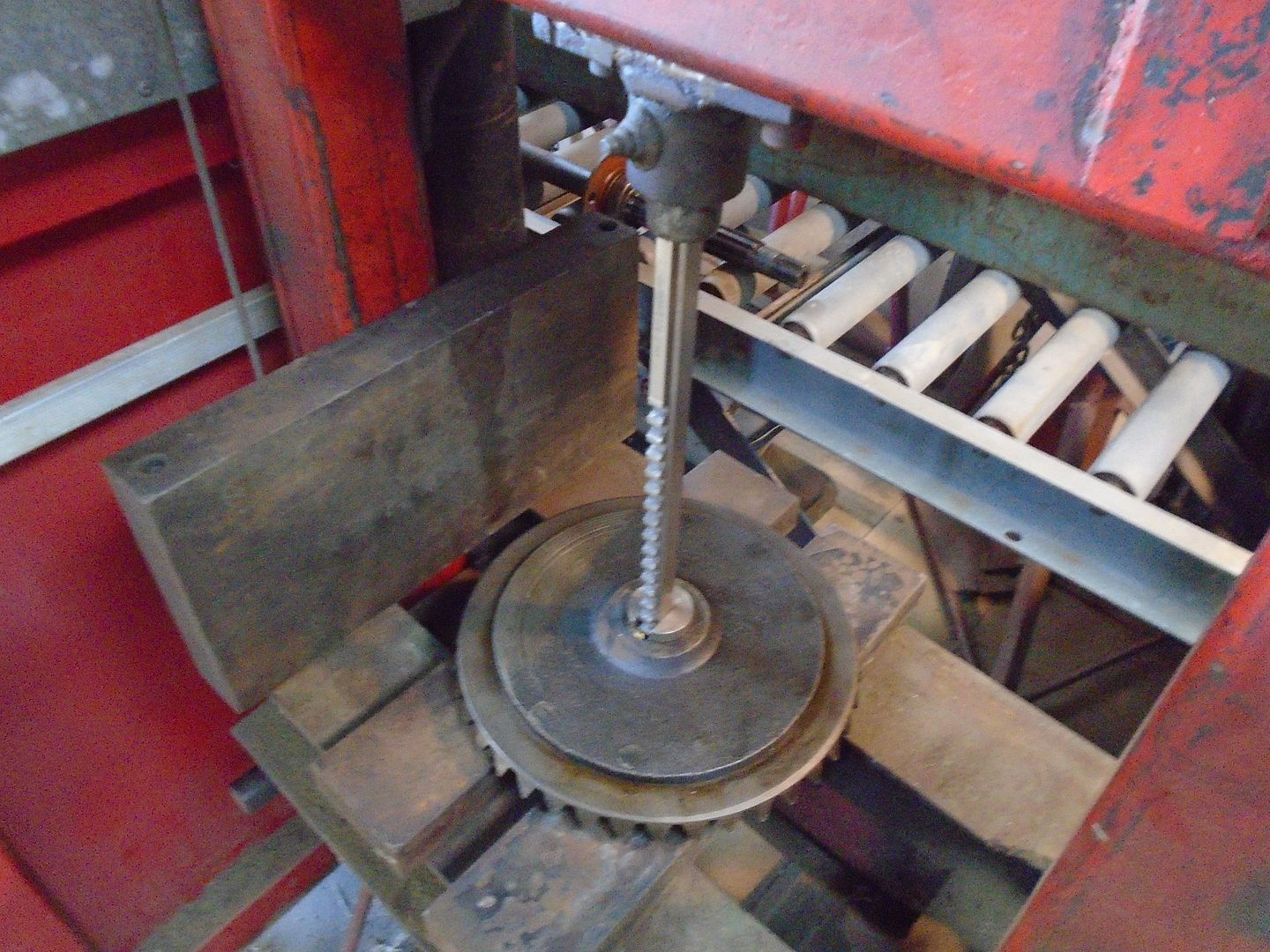
Here is the finished keyway.
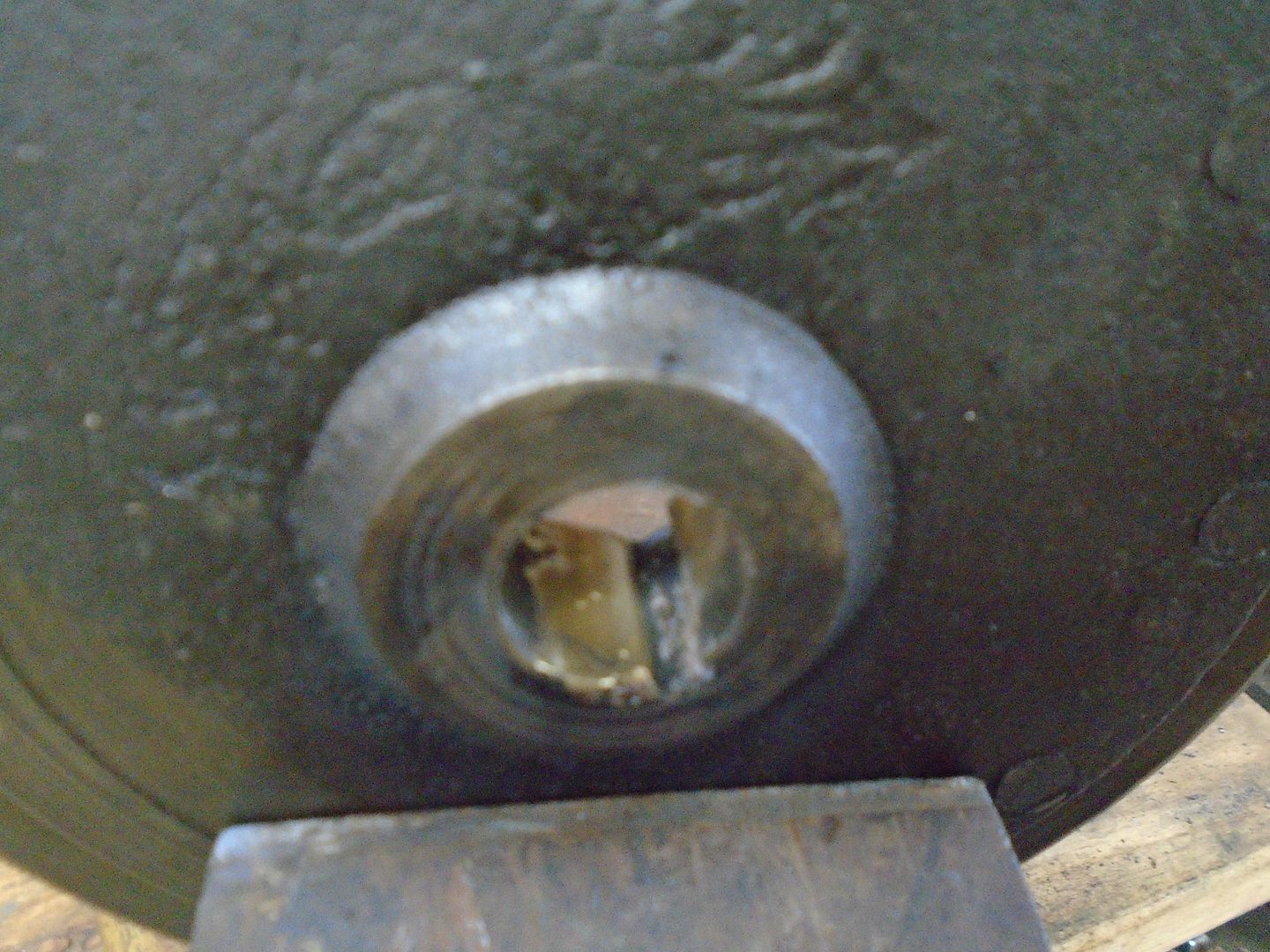
The shaft is chucked up in the lathe.
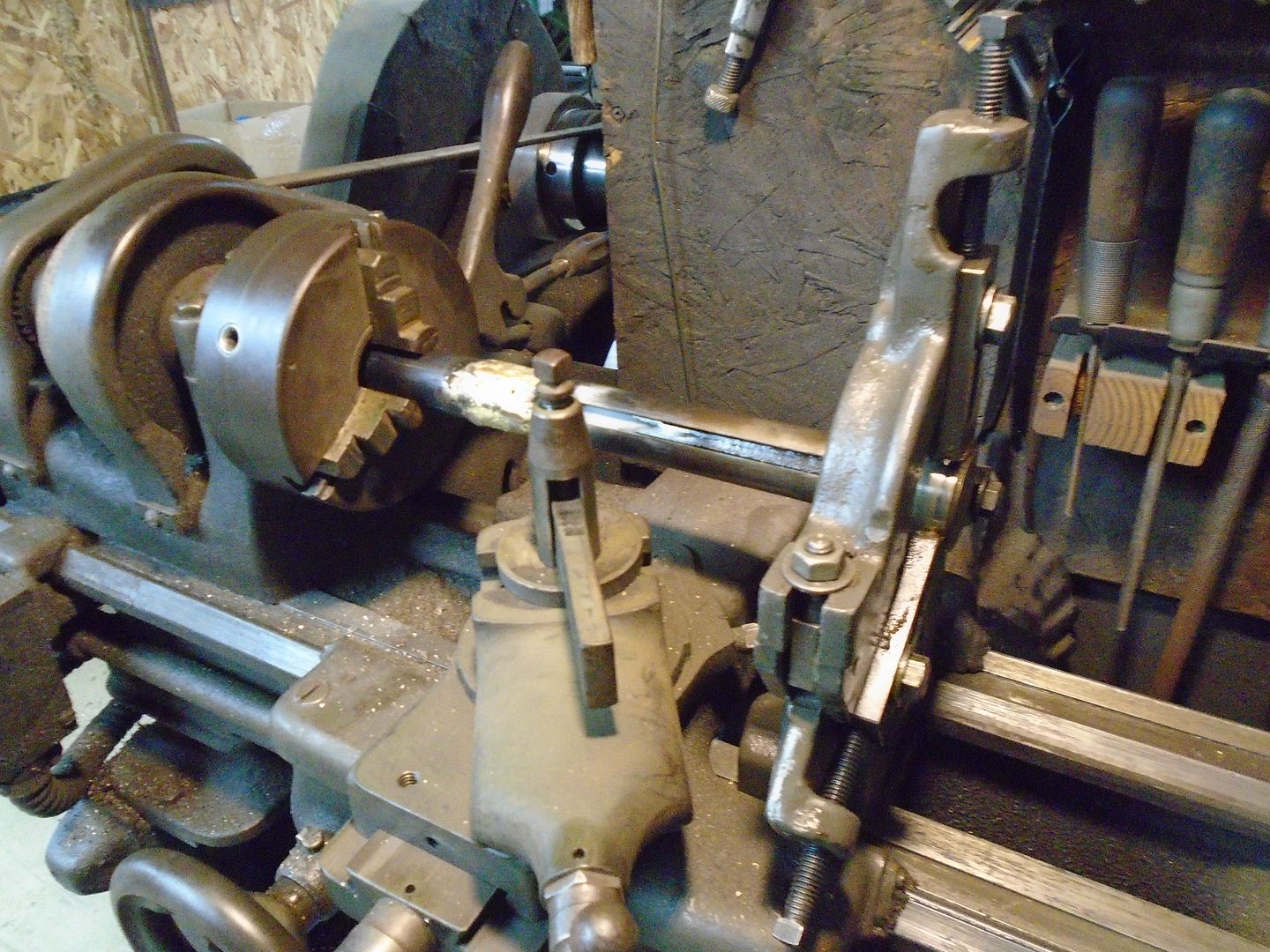
This is the finished cut on the shaft.
I made it real close to the size of the bore in the ring gear so the gear will have to be pressed onto it.
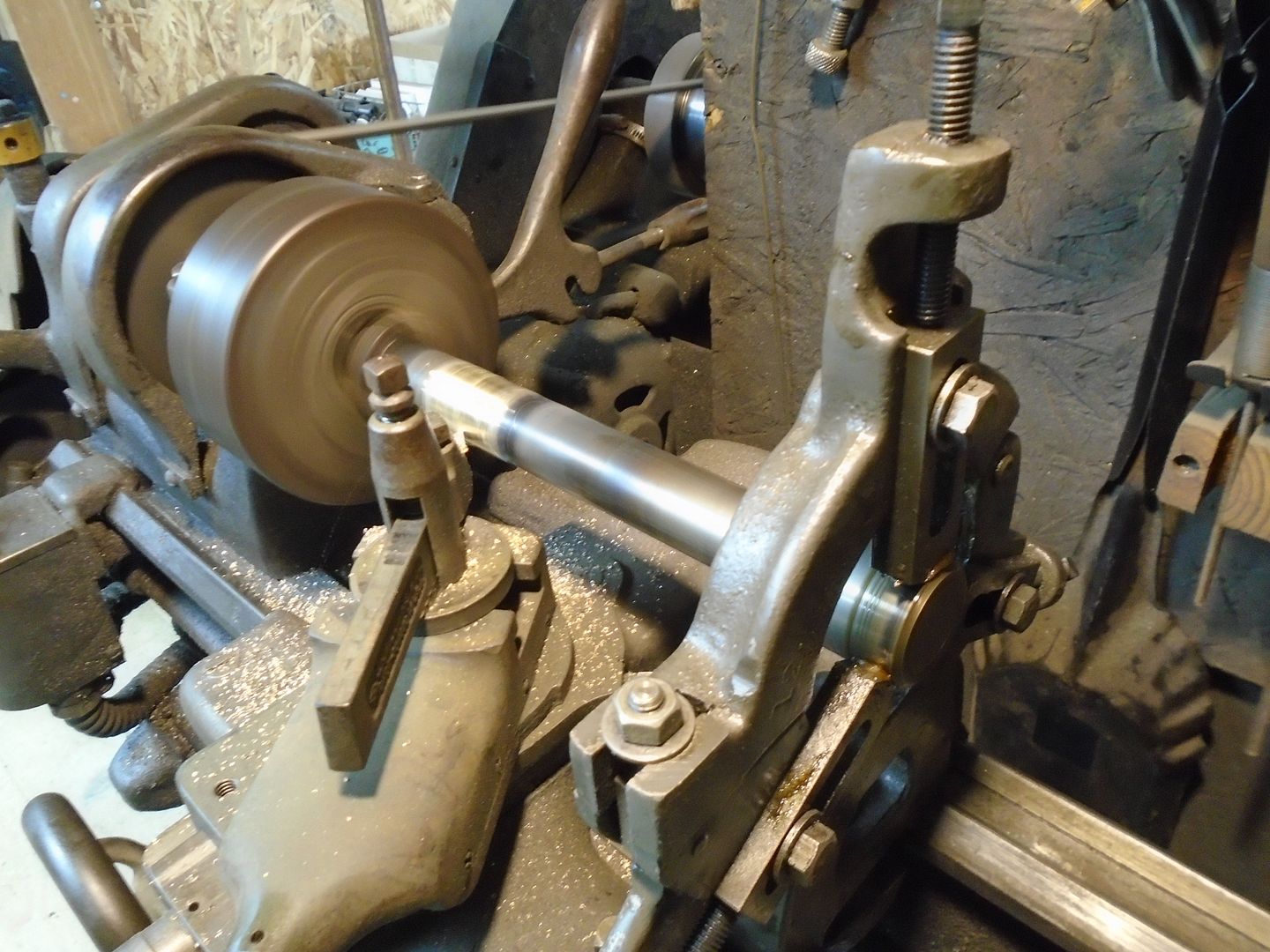
The keyway is being machined into the shaft.
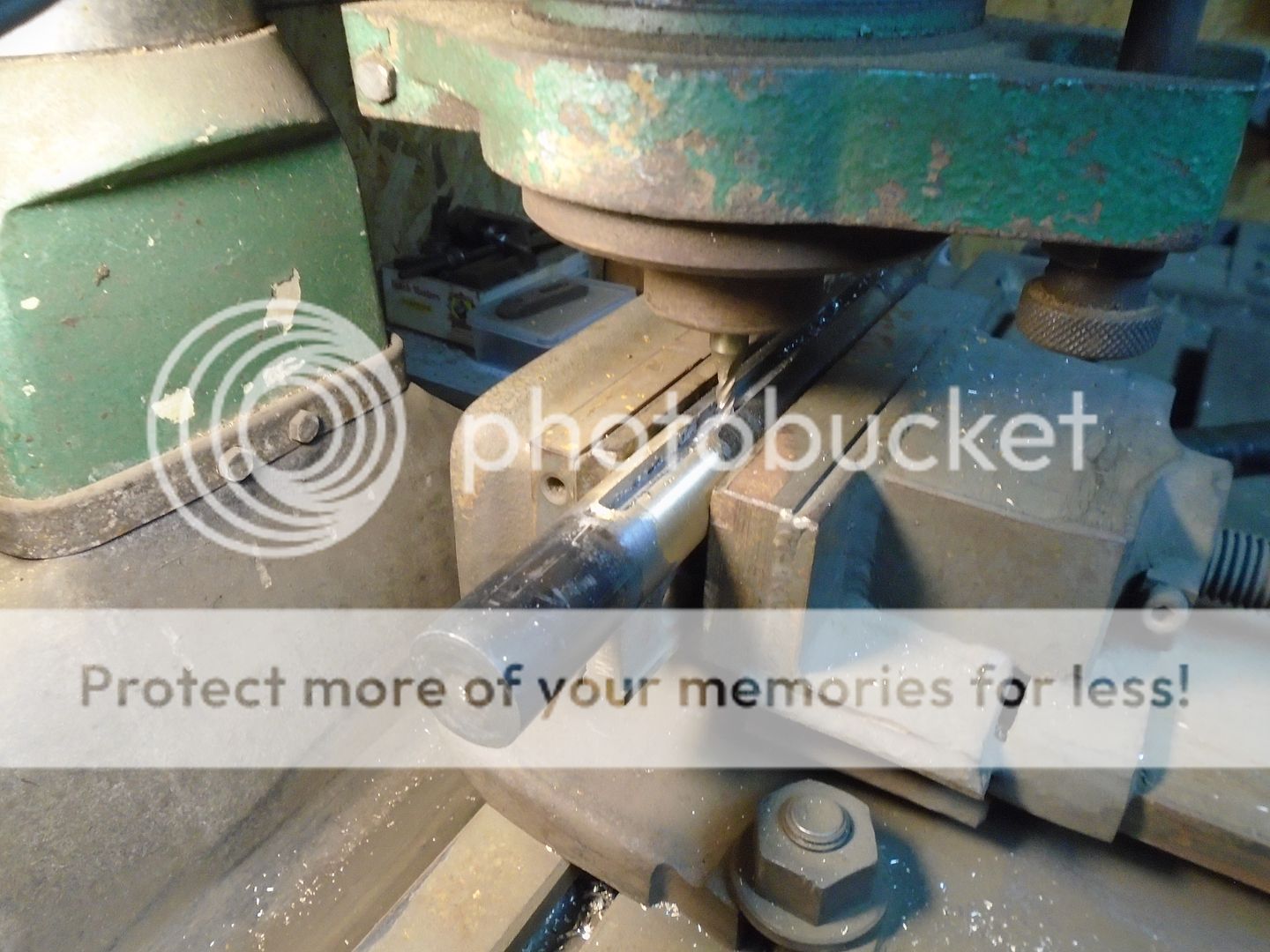
The shifter gear is slid onto the shaft and the bearing collar is pressed back onto that end.
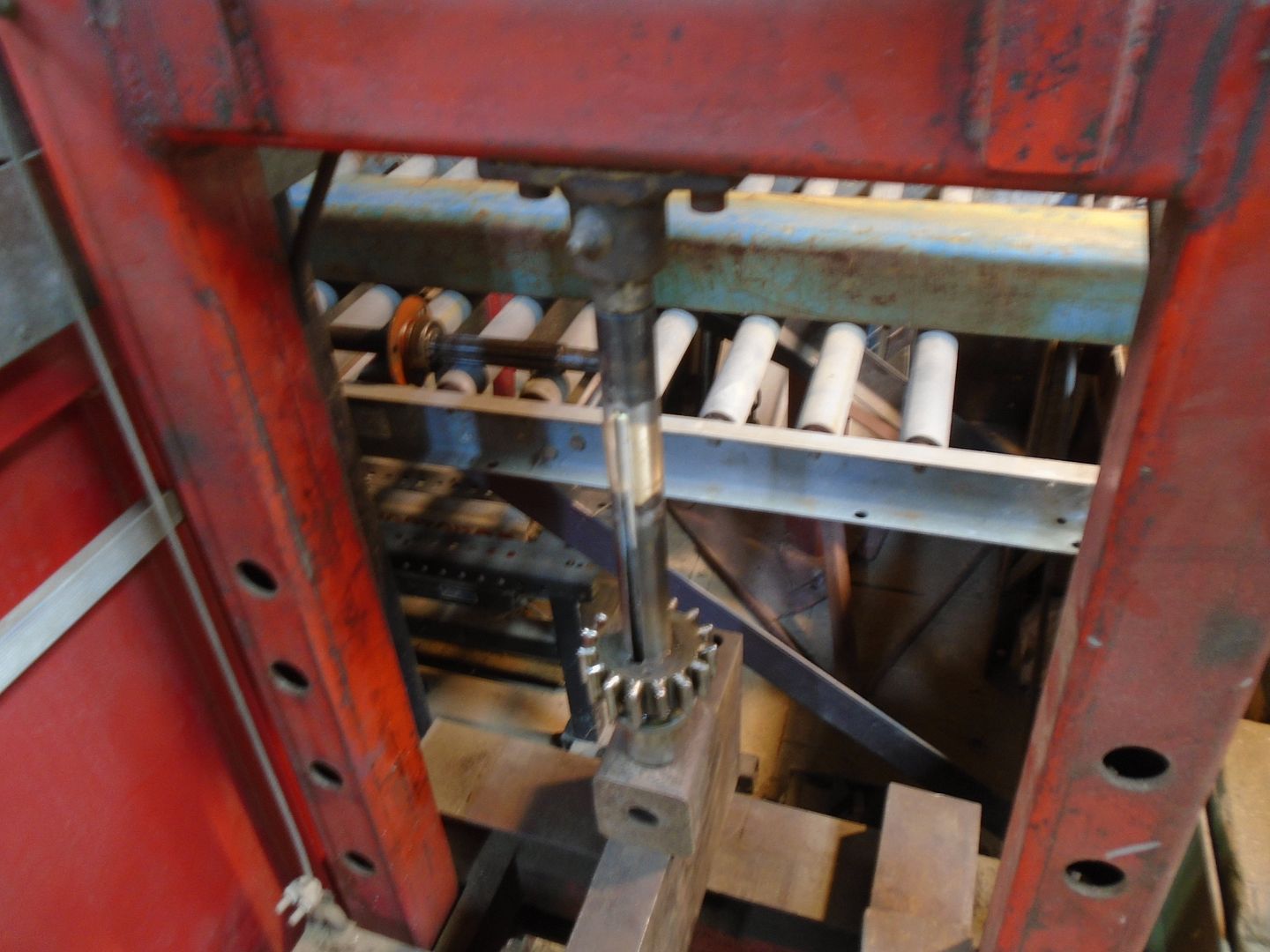
Using a brass punch, the shaft was hammered into the bore of the ring gear.
Then I used a socket that just fit over the shaft to drive the bearing collar on this end.
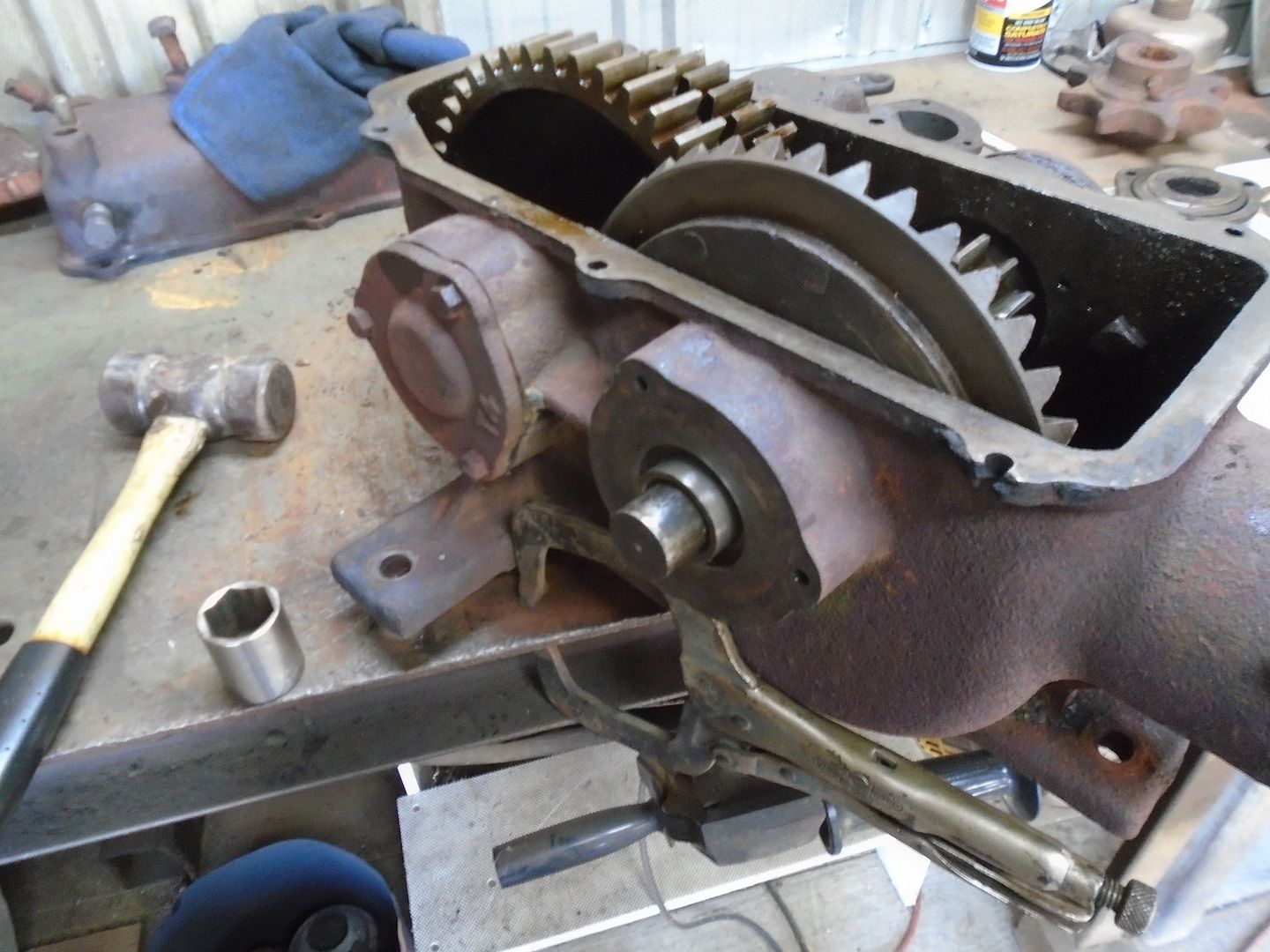
Both end caps are mounted on the sides of the transmission and everything mover smoothly.
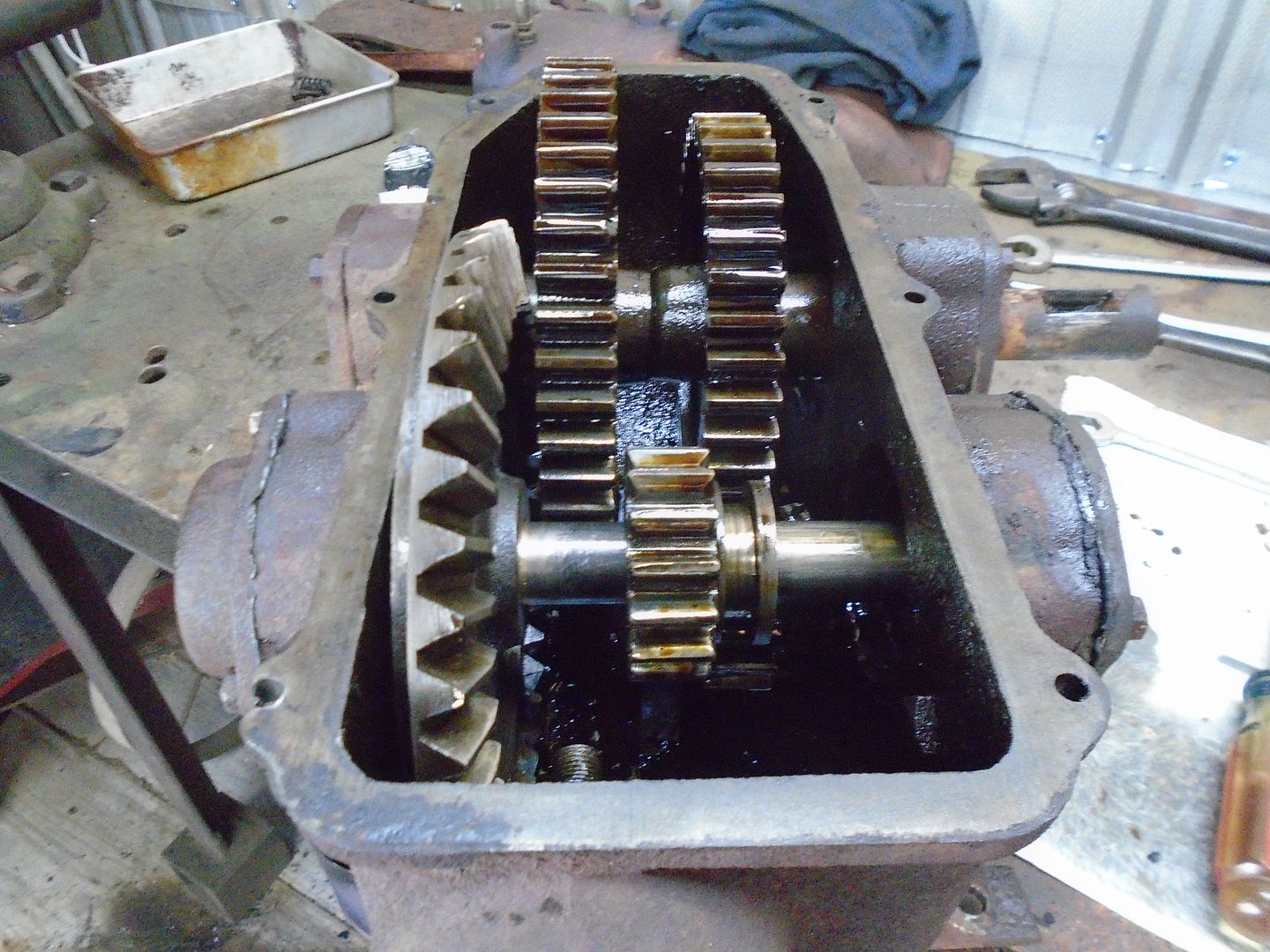
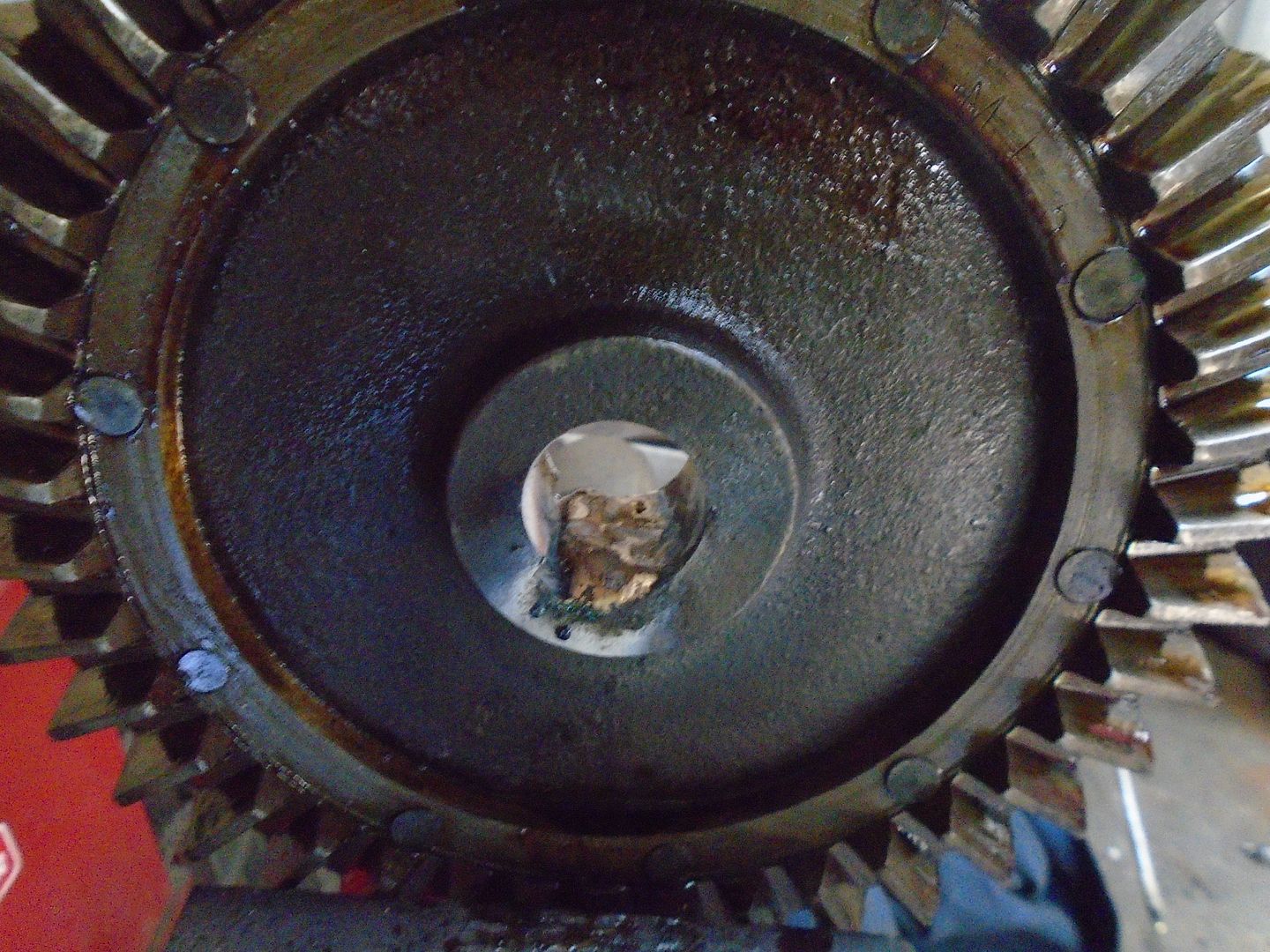
The shaft is built up with brazing rod also.
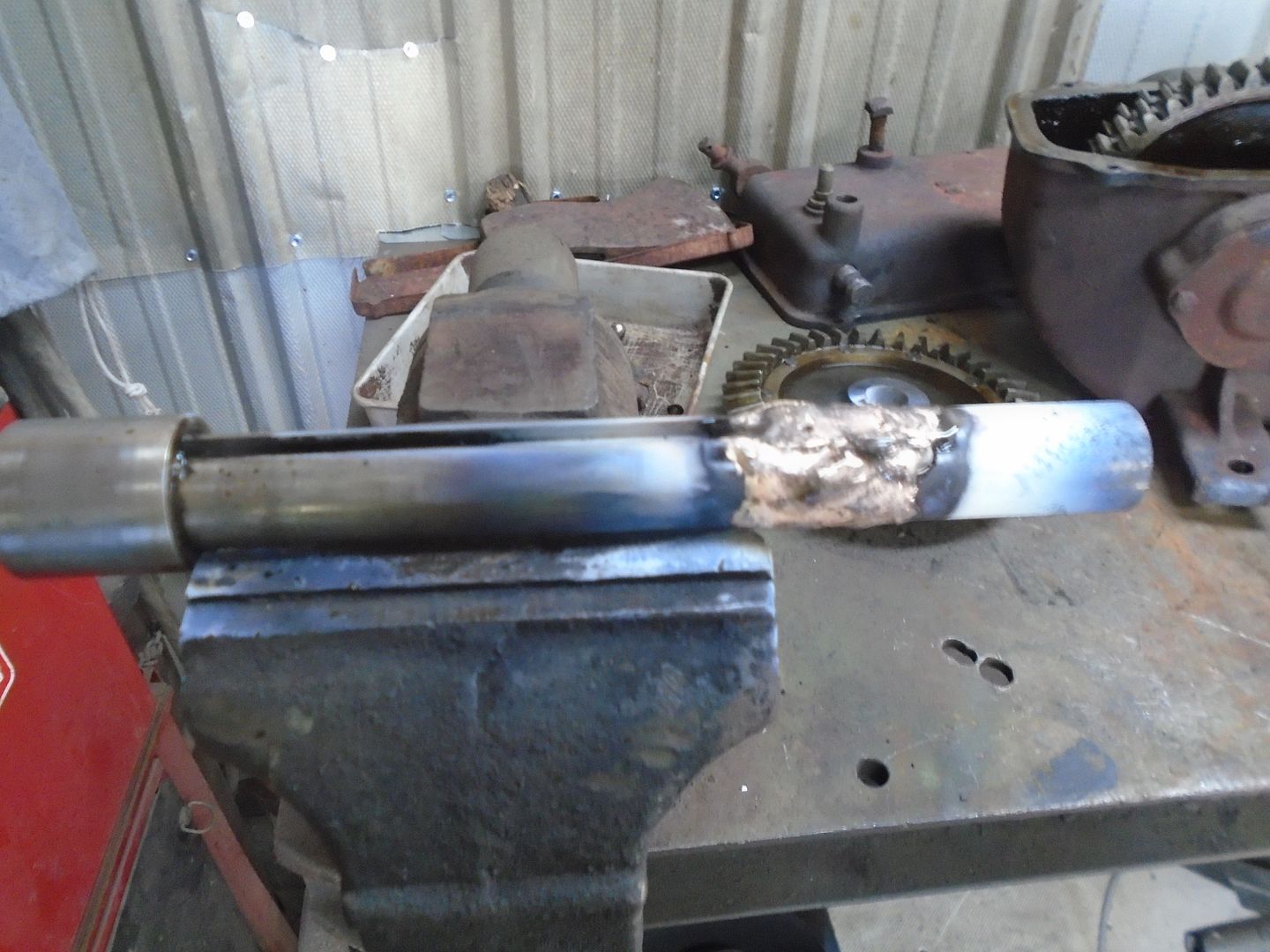
I chucked the ring gear up in the lathe to bore it out to size.
The hole in the ring gear was warn a little so I machined it .010 oversize.
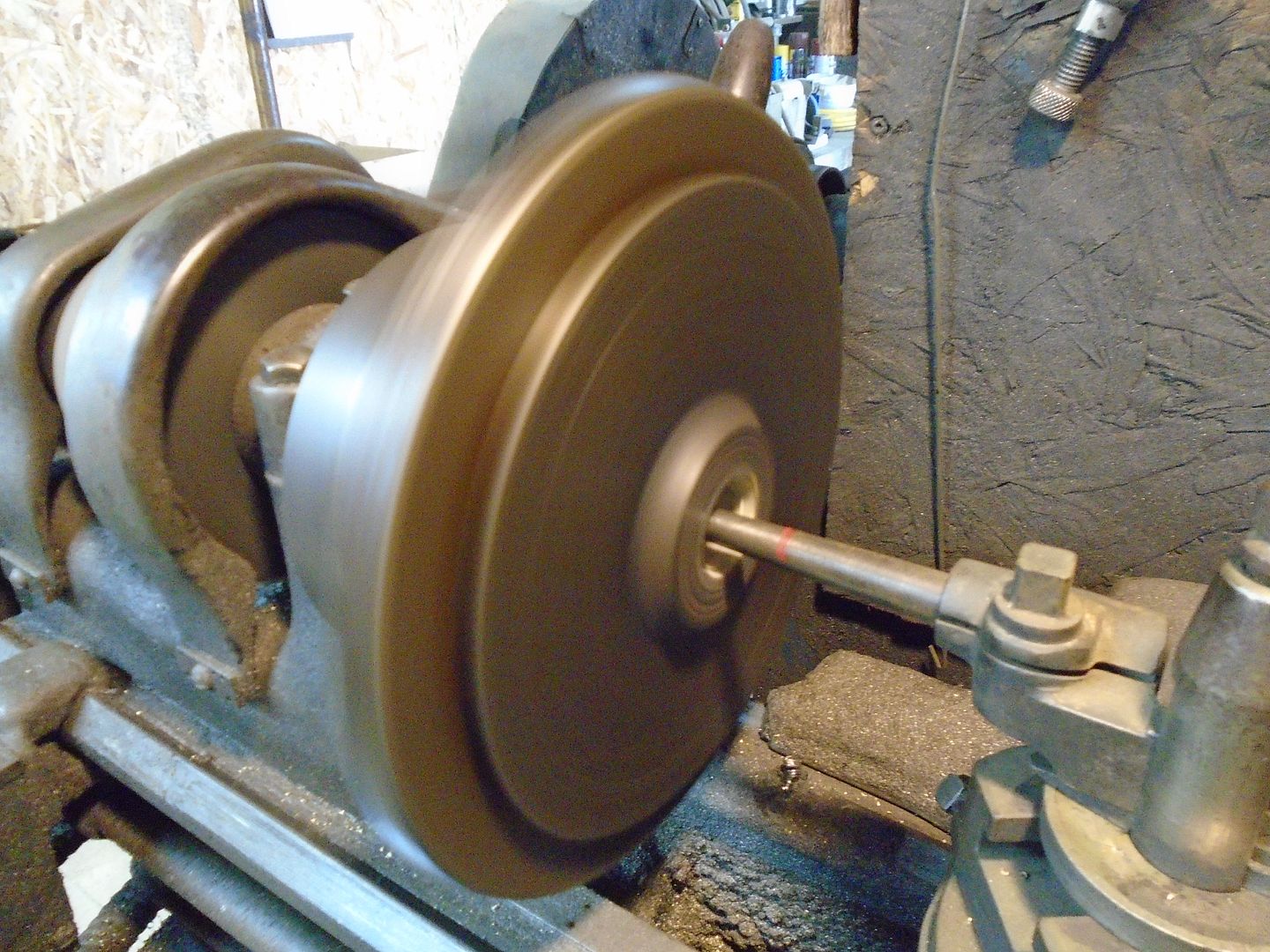
Then the key is re-cut using a key broach.
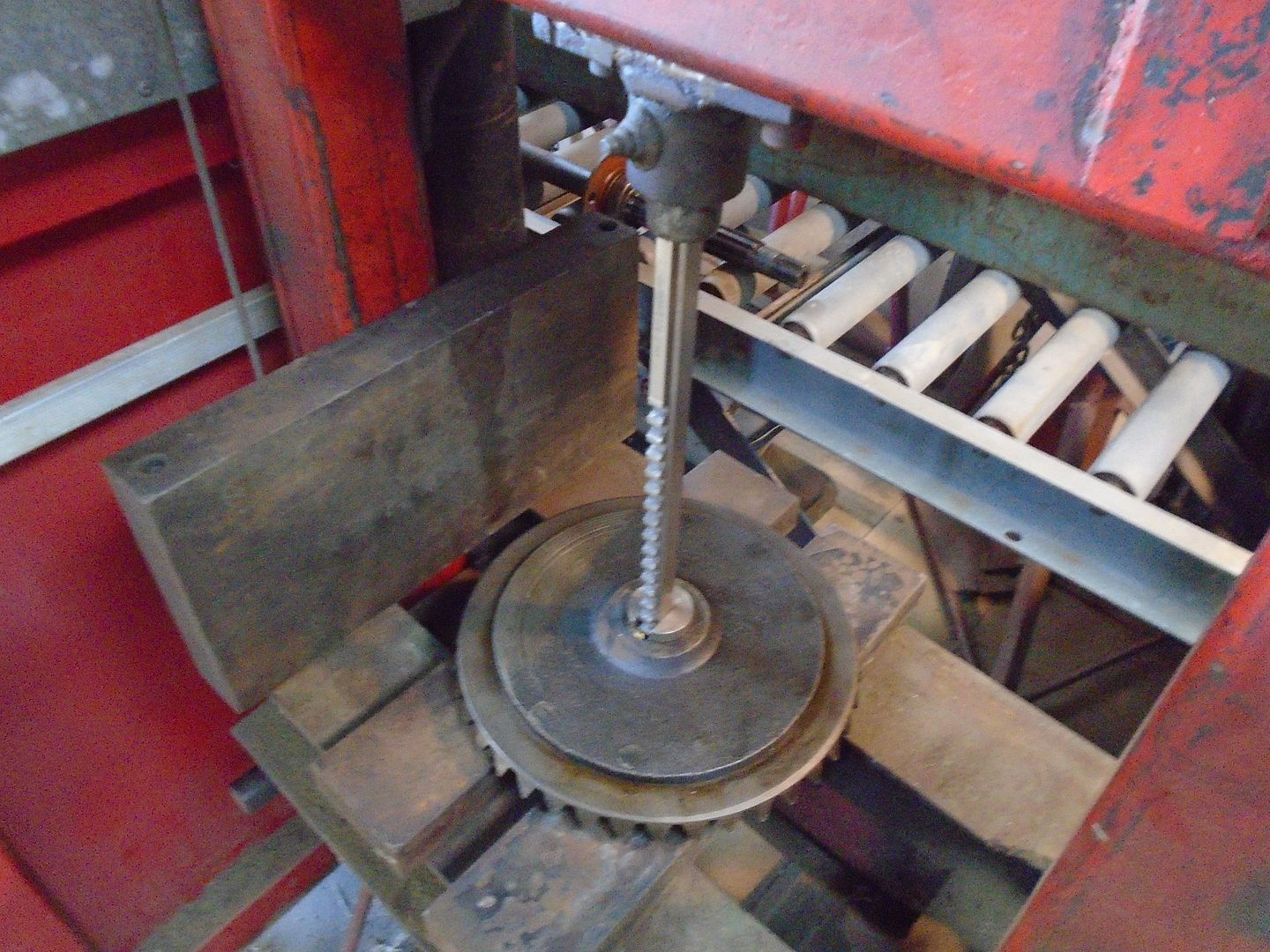
Here is the finished keyway.
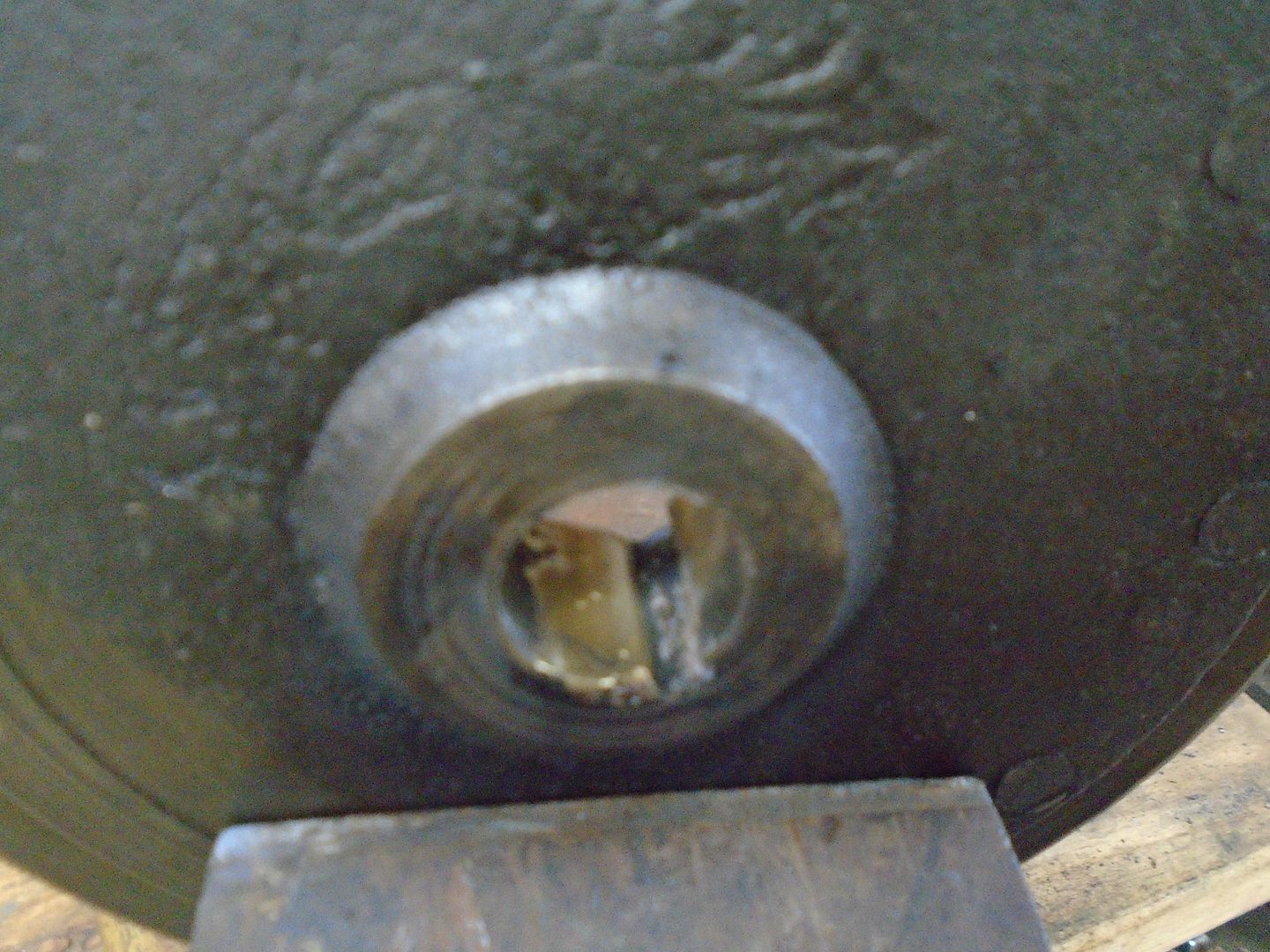
The shaft is chucked up in the lathe.
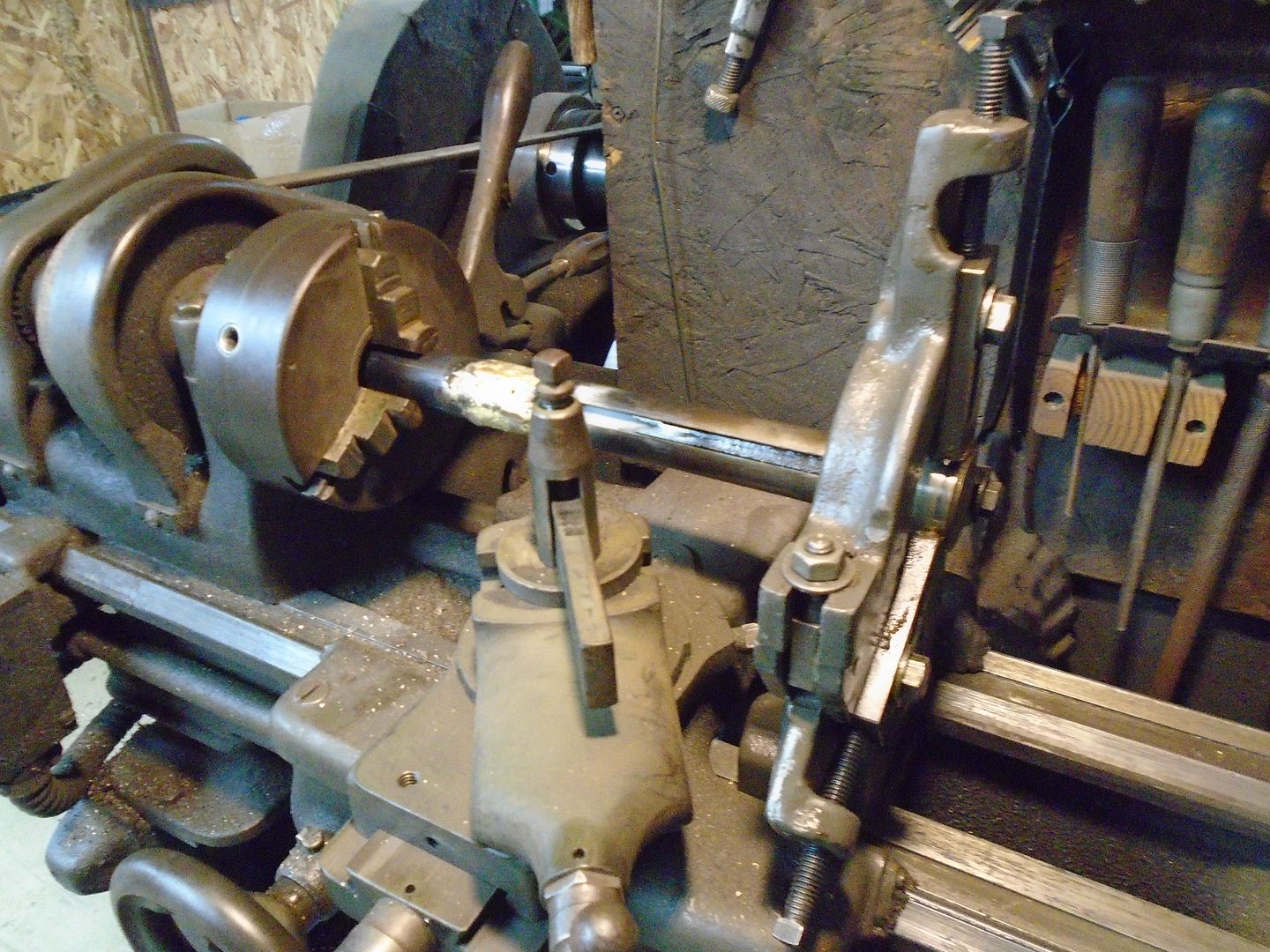
This is the finished cut on the shaft.
I made it real close to the size of the bore in the ring gear so the gear will have to be pressed onto it.
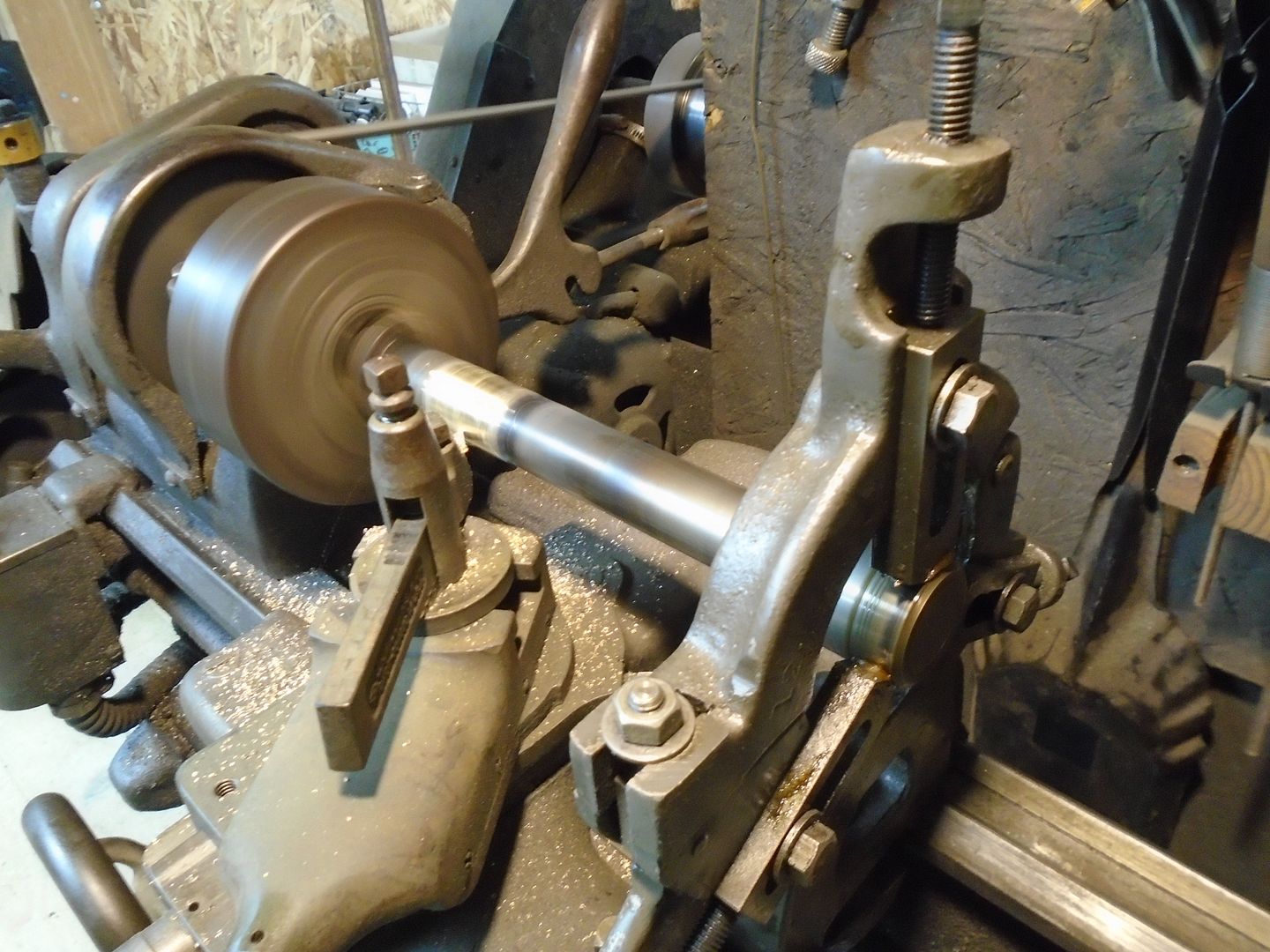
The keyway is being machined into the shaft.
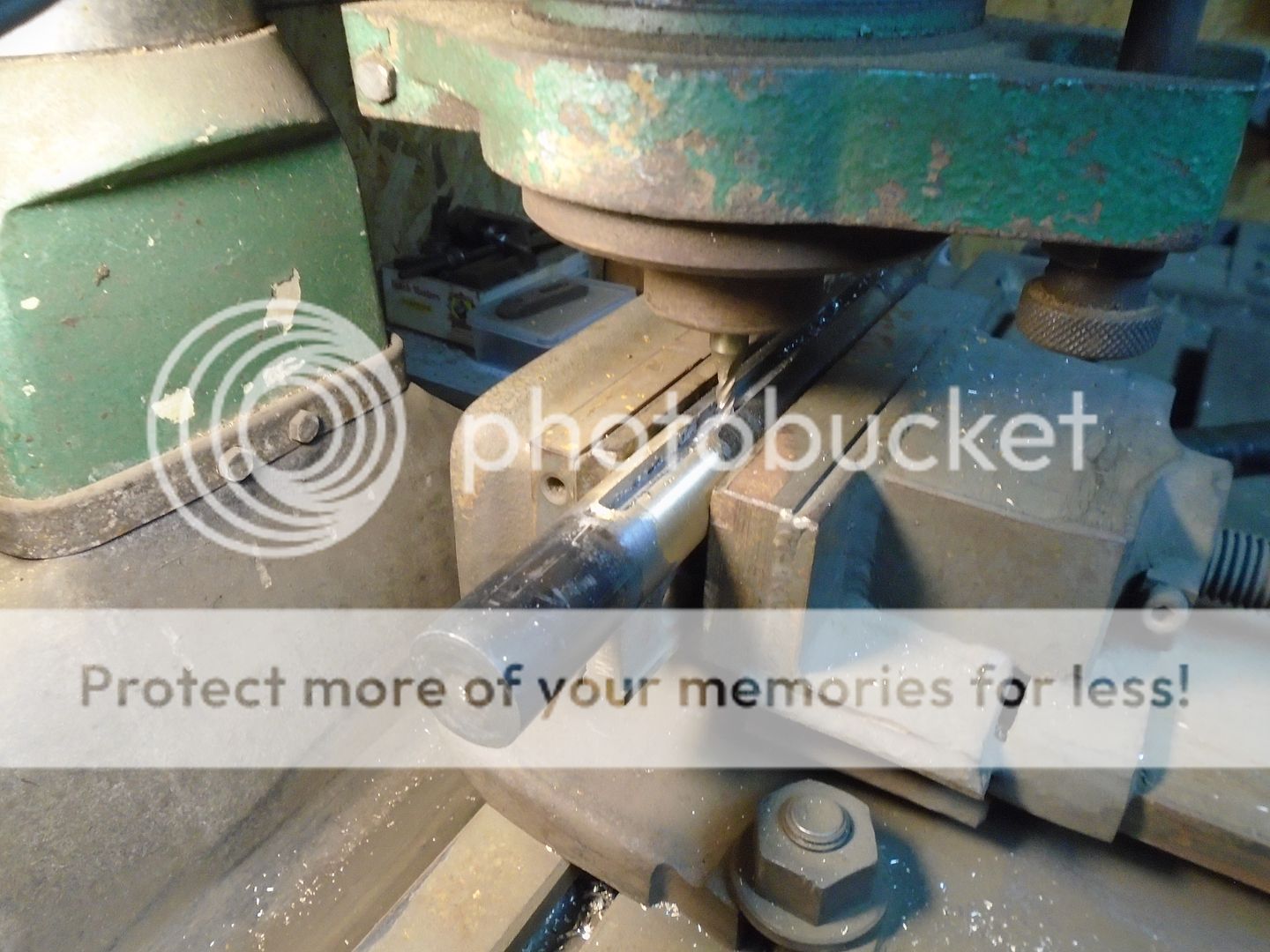
The shifter gear is slid onto the shaft and the bearing collar is pressed back onto that end.
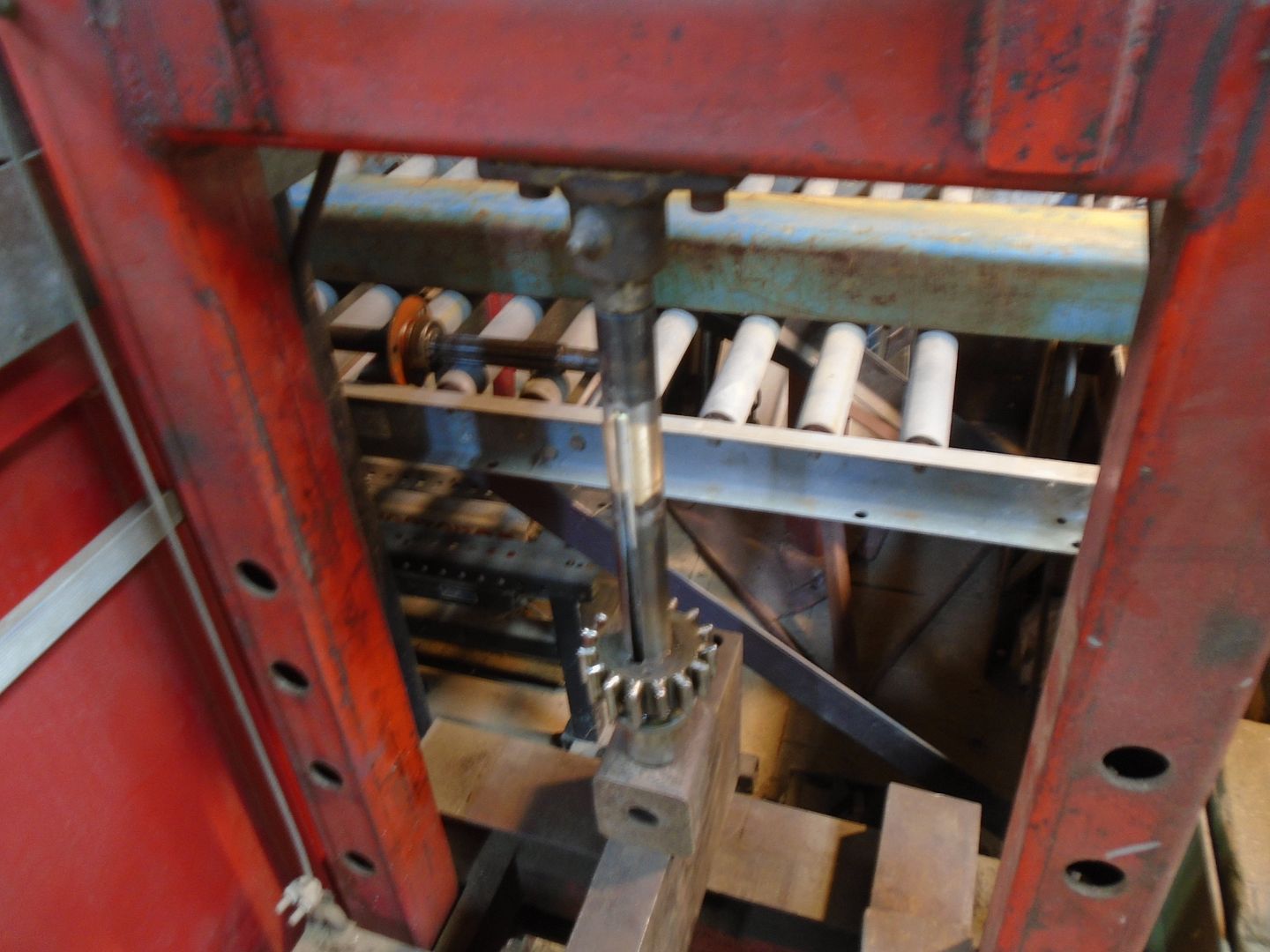
Using a brass punch, the shaft was hammered into the bore of the ring gear.
Then I used a socket that just fit over the shaft to drive the bearing collar on this end.
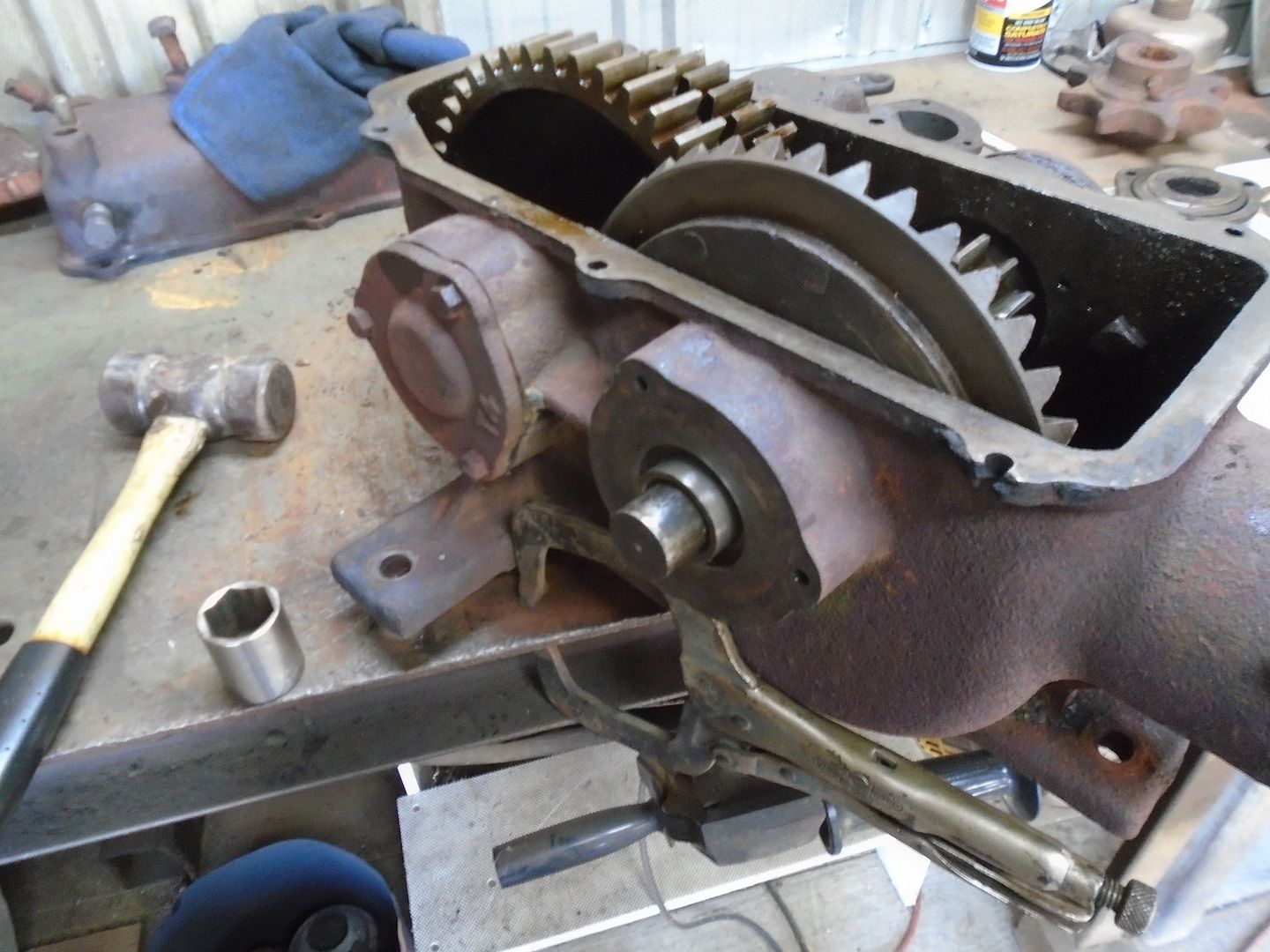
Both end caps are mounted on the sides of the transmission and everything mover smoothly.
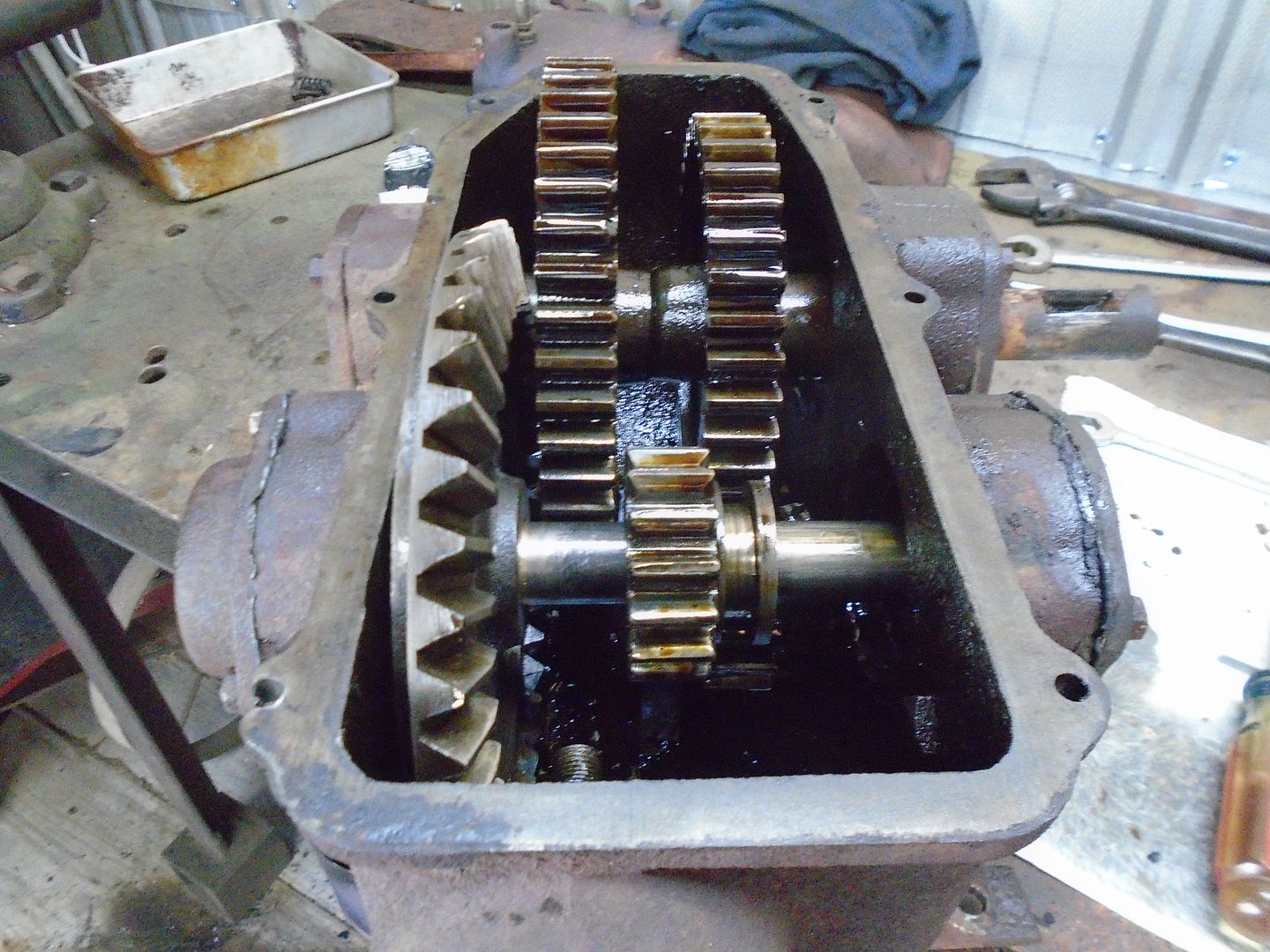