I bore out a piece of round steel and put in brass bushings to make the pivot mount for the front axle.
The front of the frame is then cut out.
And the pivot mount is welded in place.
The wheels were mounted on the spindles and the axle assembly is mounted to the frame.
... Note ... the two lower bolts holding holding the spindle mounts to the axle bar are longer then the two upper bolts.
The radius rods will fasted to these longer bolts.
These are the radius rods that keep the front axle from moving backward or forward.
Obviously, they need a little work.
They were straightened by pressing them in between two flat steel bars.
I kept rotating them around as I operated the press until they were straight.
Then they were sand blasted and primed.
To make it easier to put these radius rods on, I picked the front of the frame up and turned it over.
With the frame now upside down, I put a pair of screw jacks under the axle to keep it from rocking from side to side.
Whoever originally converted this walk behind tractor to a riding tractor had the radius rods mounted on the two longer bolts with the nuts tightened down on them.
This did not allow the front of the radius rods to pivot.
With them being bent like they were, I'm guessing there was enough flexing in the rods that it didn't matter that much if the front ends were fastened down tight.
To correct that problem, I drilled the mounting hole in the front of the radius rods to a larger size.
Then I got longer nuts and machined a boss on them.
The front end of the radius rods can now pivot on the nuts with the nuts fastened down tight to the axle.
The other end of the radius rods have an Ford Model - A, adjustable ball and socket style tie rod end.
In my junk I found a pair of angle mounts off something that will work well to mounting the back end of these radius rods.
I put them up in the mill and bored a 1-1/8 inch hole in them.
I had already turned the back of the tie rod balls to a 1-1/8 inch diameter.
The tie rod ball is fit into the hole in the bracket and clamped in the vice.
Then it is welded in place.
Here is how the brackets look from the front side.
The radius rods are fastened to the front axle and the rear mounting brackets are welded to the underside of the frame.
The frame is then picked back up and turned back over on its wheels.
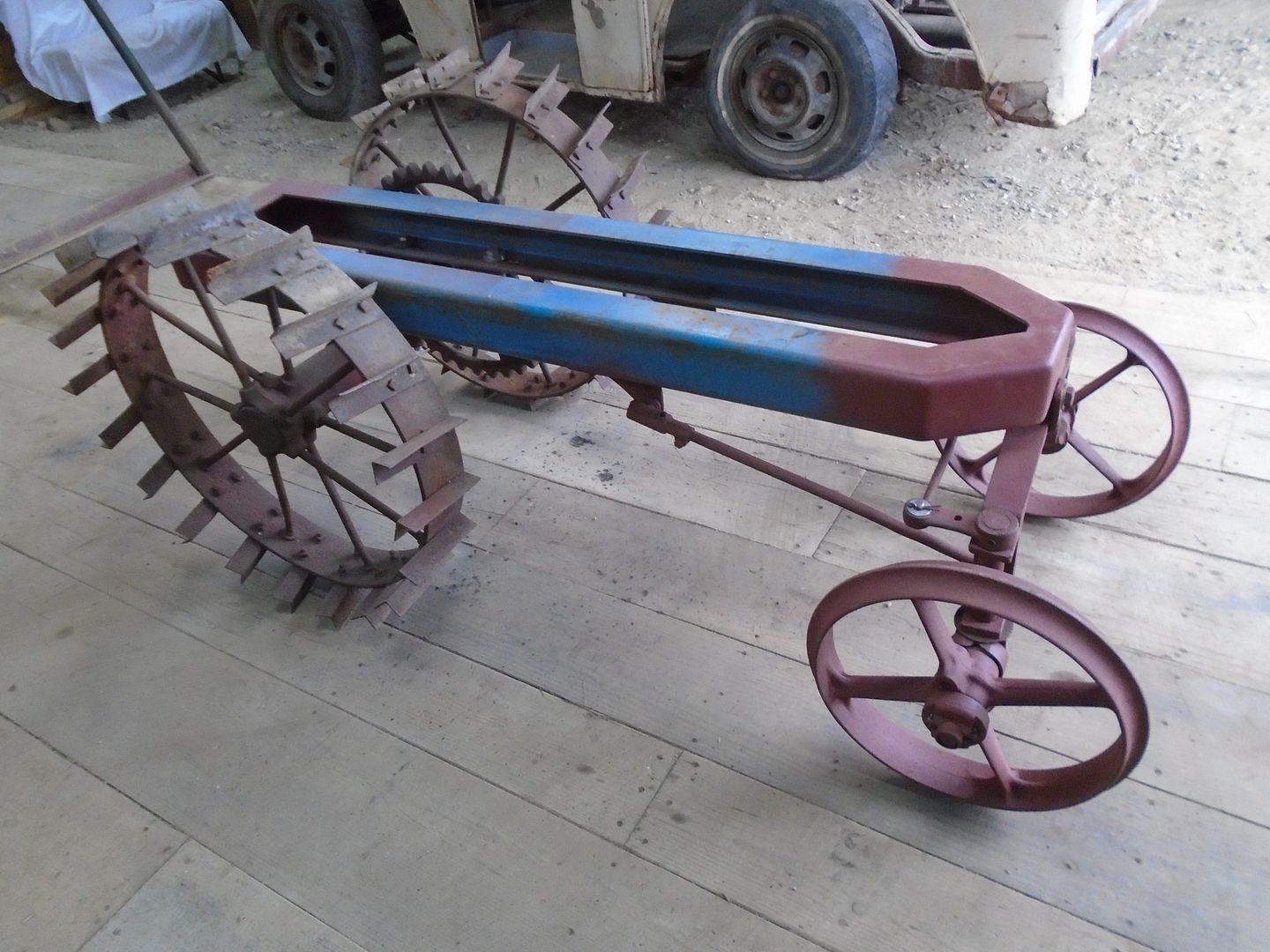