In these photos, you can see the steering column that came with this tractor.
At some point, a more modern steering wheel had been mounted to it.
I removed that steering wheel and then used a puller to remove what was left of the original steering wheel.
Then I was able to remove the steel tube of the column from the steering box.
Here are the parts of the column tube.
This is not Ford a model-T steering column but it had the same type of control levers like the Ford did.
Over the years, water has run down inside the column tube and rusted the steering shaft tight to the steering box.
By heating up the steering box, I was able to knock the rust out between the box and the shaft.
That was all that was keeping the steering shaft from moving and it moves freely now.
As you can see, the ball mount for the drag link is twisted around 90 degrees to the steering box.
I was able to remove the steering arm without having to use heat on it.
The splines and threads are all still in good condition on the steering shaft.
I heated up the end of the arm and twisted the ball back around so it is now inline with the shaft coming out of the steering box.
My next problem is that someone has welded a piece of flat steel to the cover on the steering box and they welded two of the bolts also.
I cut the welds with a torch to remove the piece of steel.
After removing the cover, you can see that the gears are in good shape.
I clamped the cover up on the lathe.
This lets me hold it securely and still be able to rotate it as I grind the welds down with a small air grinder.
Here's how it looks mounted back onto the steering box.
Instead of splines like on a more modern steering shaft, this has a taper with a keyway to hold the steering wheel.
At this point I ran into something that has never happened to me before.
I have had this old wooden steering wheel for well over 40 years.
This steering wheel has a taper with a keyway and If you look closely you can see that the center of the steering wheel is the same size and shape as the part that came off this steering column.
And this wood steering wheel fits perfectly on this steering shaft.
I am convinced that this steering wheel came off the same model of car that this steering column came out of.
I am most likely going to have to shorten this steering shaft so when I cut it off, I'll put the end that the steering wheel fits on up on the lathe and cut new threads into the end of it.
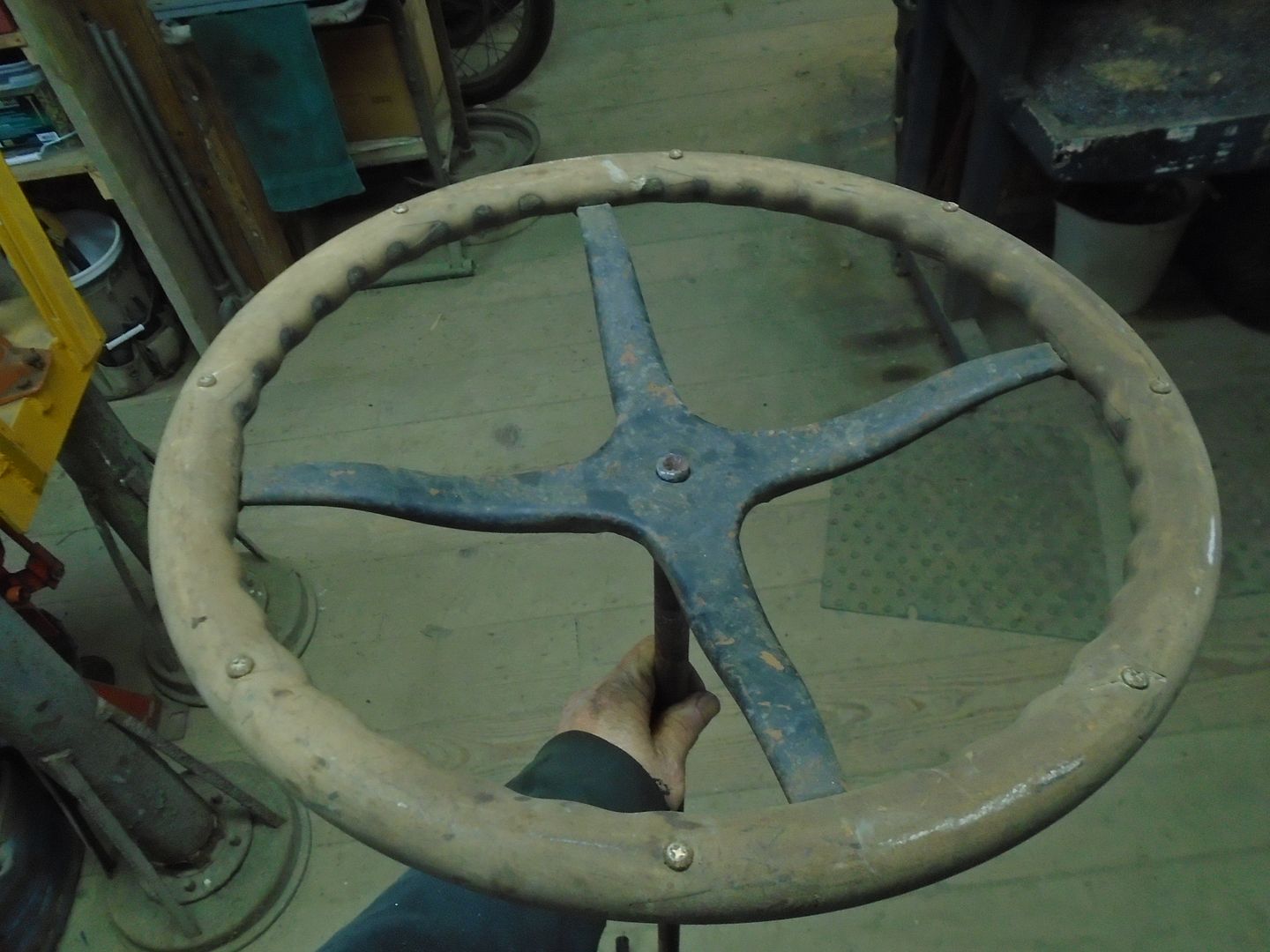