Being currently held up on the model-T project for awhile, Ive decided to do some more work on building the powered law roller.
Here is the link to the previous posts.
Back on the powered lawn roller idea.
I had been looking for a Bolens Ridemaster frame and hadn't found one yet so I stopped working on this project about a year and a half ago.
I want to thank Bryan Spray of Hobbs, Michigan ( close to Tipton ) and Jerome Wilber of Elsie, Michigan for helping me get the Ridemaster frame that I needed.
I was able to trade some parts with Bryan for the frame which I picked up when I went to the tractor show at Tipton. Jerome and his dad were there and he helped me get the parts together and load them onto my truck.
Here is the main Ridemaster frame.
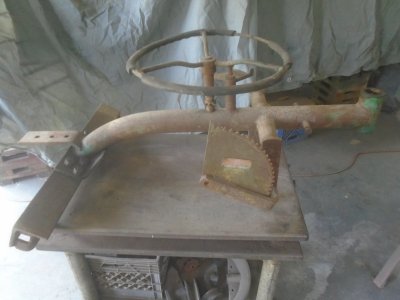
The toolbar, rear axle arms and lift mechanism.
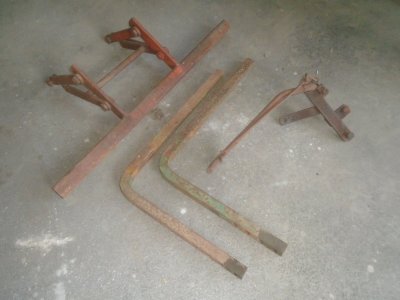
The agreement with Bryan was for a complete frame less the wheels, drive transmission and engine. However I was not able to get the large steering pulley that mounts over the front wheels that the steering chain wraps around.
So I'm still looking for one of those. If any of you have a spare that you want to sell .. please contact me. I can pay you thru Papal.
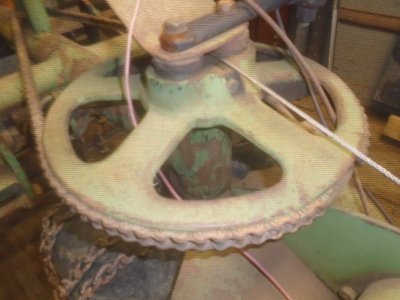
This is the drive assembly that I had built up in the first posts.

Here is the link to the previous posts.
Back on the powered lawn roller idea.
I had been looking for a Bolens Ridemaster frame and hadn't found one yet so I stopped working on this project about a year and a half ago.
I want to thank Bryan Spray of Hobbs, Michigan ( close to Tipton ) and Jerome Wilber of Elsie, Michigan for helping me get the Ridemaster frame that I needed.
I was able to trade some parts with Bryan for the frame which I picked up when I went to the tractor show at Tipton. Jerome and his dad were there and he helped me get the parts together and load them onto my truck.
Here is the main Ridemaster frame.
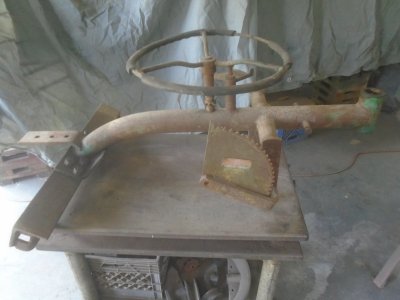
The toolbar, rear axle arms and lift mechanism.
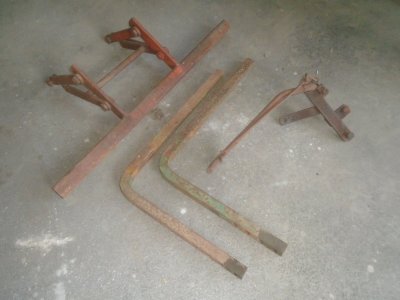
The agreement with Bryan was for a complete frame less the wheels, drive transmission and engine. However I was not able to get the large steering pulley that mounts over the front wheels that the steering chain wraps around.
So I'm still looking for one of those. If any of you have a spare that you want to sell .. please contact me. I can pay you thru Papal.
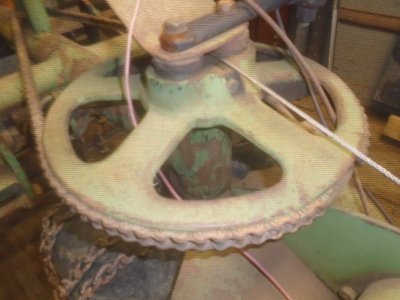
This is the drive assembly that I had built up in the first posts.
