The drive chain is disconnected from hydro transmission so I can get the parking brake band in around the brake drum.
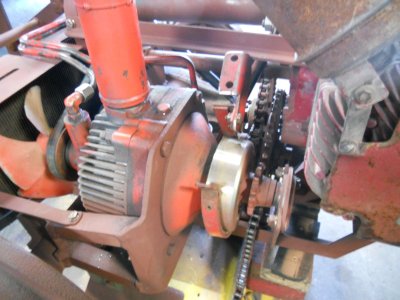
Ths mount for the brake band is fastened in place and the chain is put back on.
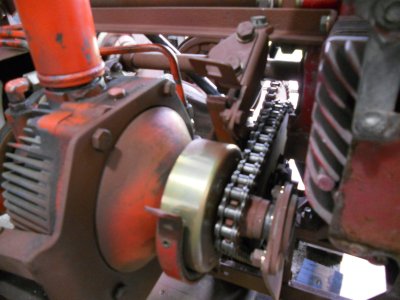
The mounting bracket for the brake cable is bolted on and the cable is installed.
This is the position with the brake off.
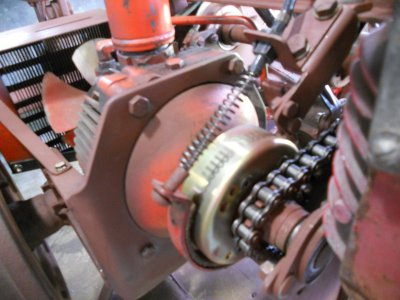
The other end of the cable is attached to the lever that was used to raise and lower the toolbar.
The cable is attached to the end of the 1/2 inch bolt with the spring around it.
This is the off position.
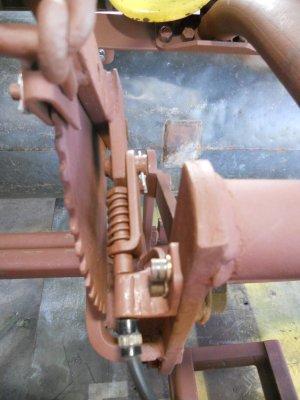
This is the position of the lever with the parking brake off.
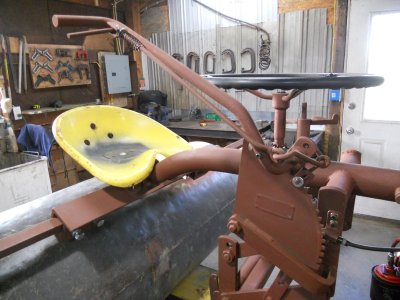
This is the position with the parking brake on.
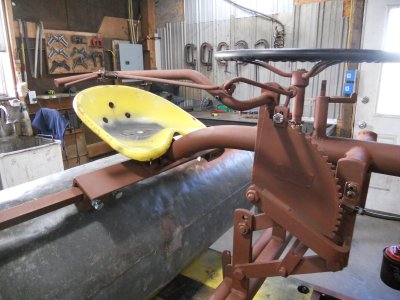
Notice that the spring around the 1/2 inch bolt is now compressed. This makes sure that there is good pressure on the brake band and allows the lever to be moved enough to get the lock pin into the next higher notch.
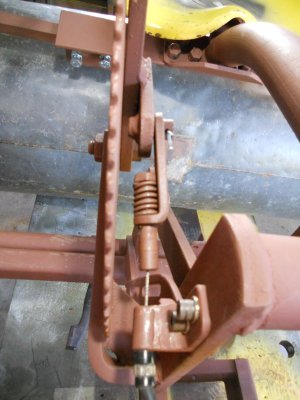
The brake band it tight around the drum.
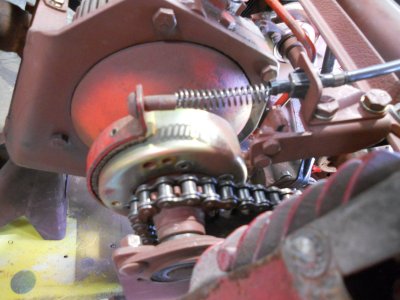
The brake cable runs around the steering post and there is no interference with turning in either direction.
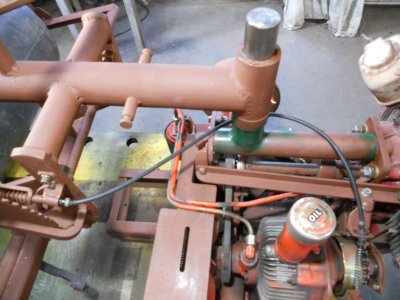
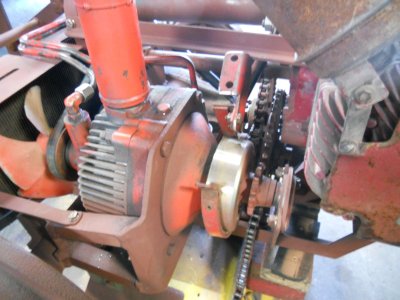
Ths mount for the brake band is fastened in place and the chain is put back on.
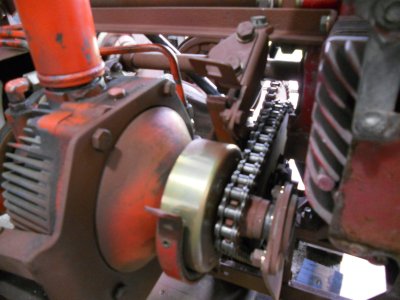
The mounting bracket for the brake cable is bolted on and the cable is installed.
This is the position with the brake off.
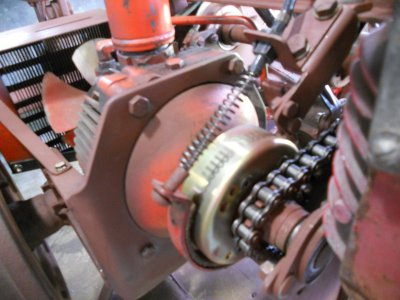
The other end of the cable is attached to the lever that was used to raise and lower the toolbar.
The cable is attached to the end of the 1/2 inch bolt with the spring around it.
This is the off position.
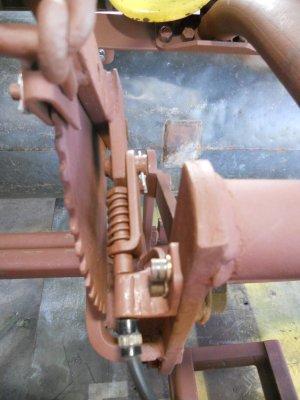
This is the position of the lever with the parking brake off.
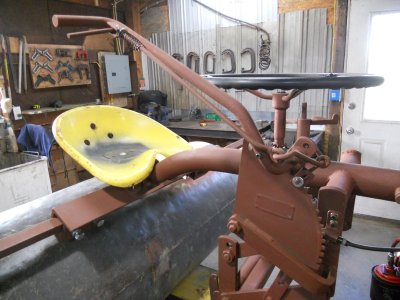
This is the position with the parking brake on.
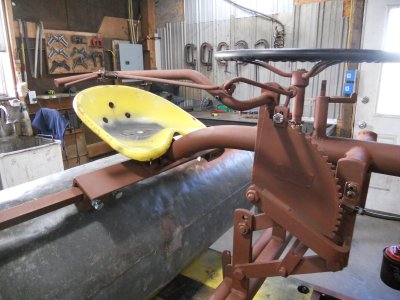
Notice that the spring around the 1/2 inch bolt is now compressed. This makes sure that there is good pressure on the brake band and allows the lever to be moved enough to get the lock pin into the next higher notch.
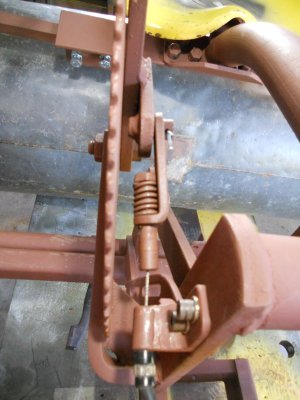
The brake band it tight around the drum.
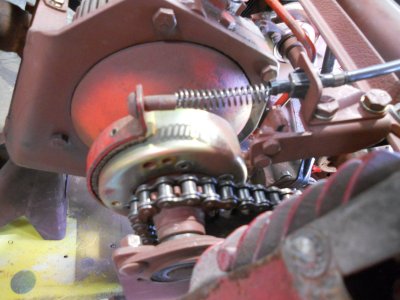
The brake cable runs around the steering post and there is no interference with turning in either direction.
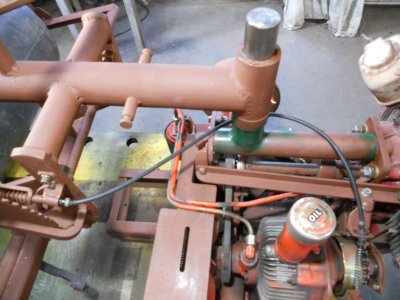