The new alternator/stator is mounted on the front of the engine and I have put the flywheel back on.
Here you can see that the old voltage regulator is mounted up on top of the flywheel shroud.
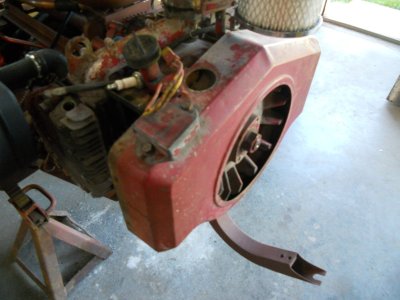
I have mounted the new voltage regulator down under the side of the shroud next to the starter.
The fan pulley and screen are fastened on the front of the flywheel. I also put two screws into the mounting holes for the old voltage regulator and I found a rubber cap that fits the large hole in the top of the shroud.
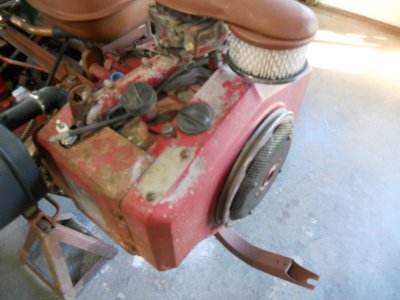
I'm assuming the red wire on the voltage regulator goes to the amp gauge and then on to the battery terminal on the switch ?
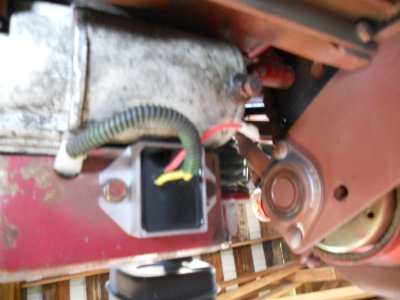
On the left side of the engine there is a terminal that has a black wire coming up from the coil.
Assuming again, this is to connect a wire that will ground out the coil to stop the engine ?
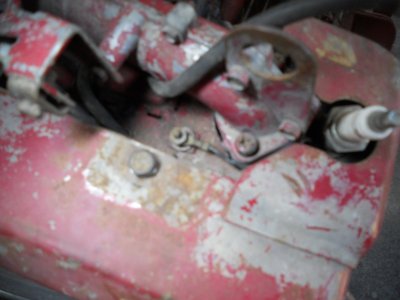
Here you can see that the old voltage regulator is mounted up on top of the flywheel shroud.
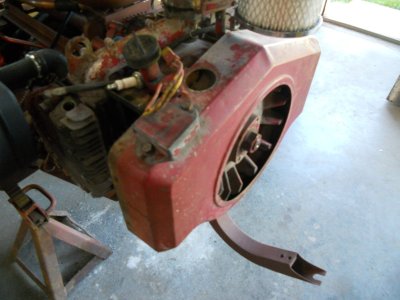
I have mounted the new voltage regulator down under the side of the shroud next to the starter.
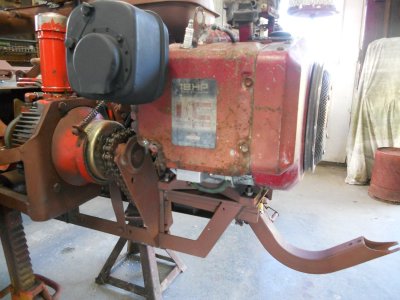
The fan pulley and screen are fastened on the front of the flywheel. I also put two screws into the mounting holes for the old voltage regulator and I found a rubber cap that fits the large hole in the top of the shroud.
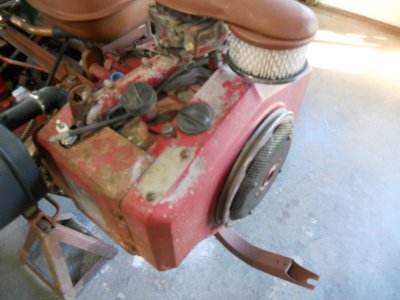
I'm assuming the red wire on the voltage regulator goes to the amp gauge and then on to the battery terminal on the switch ?
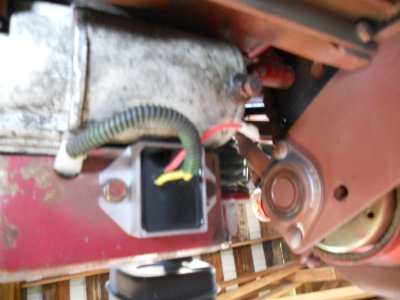
On the left side of the engine there is a terminal that has a black wire coming up from the coil.
Assuming again, this is to connect a wire that will ground out the coil to stop the engine ?
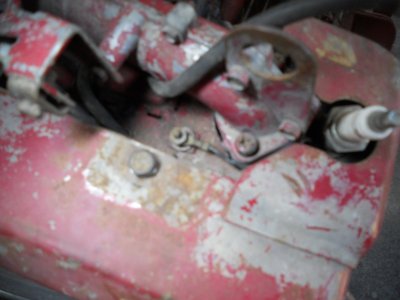