Looks to be tightly sealed to the block casting, Kenny. We use two-part putty at work that will set up like steel. Can drill and tap it even. Hopefully this stuff is as good.Hope the oil doesn't seep out around the putty.
Yeah, Noel, I did rotate the crank and cycle the rod. No problems there. The hole in the rod is toward the cam. The kit I got did have two pan gaskets. One was shaped like this block, and one was shaped like the oil pan. The dip stick housing bolts to the side of the block in this application rather than going through plumbing plugs in the base.Doug just a couple of questions. Did you slowly rotate the engine to see that the splash dipper on the rod clears the base. Pictures make it look like it might hit. Another thing is the hole in the rod to lube rod and crank. Did you put the hole toward the camshaft.
I have a couple of those engines with the different base that fits those engines. My Case 224 has that style of engine. Those cut outs are for dip sticks. Did the kit you get have two different base gaskets Doug. ?
Noel
I rigged up a "stand" with some old small block Chevy long starter bolts. Chased the threads in the pan and on the bolts. Didn't want to take a chance on boogering up those aluminum threads for the motor mount plates. That will sure make it easier to assemble the rest of the components. Will be a bit tough to torque the head I think though. It may not get torqued until in the chassis since I think a couple of things attach to head bolts.
Now I have a question. Is it safe to clean the flywheel magnets and the stator with brake cleaner? I do have some throttle body cleaner that is supposed to be safe on modern plastics. Of course the insulation on the stator is not modern materials, as well as the glue holding on the flywheel magnets.
After I got the engine up on the stand bolts,
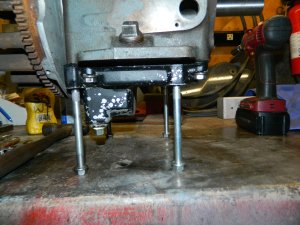
I slid the flywheel on and rotated the engine a couple times faster than I could by just rotating the crank ends. It felt smooth and solid.
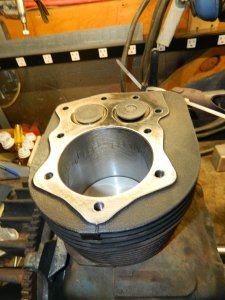
So far so good. May not get anything done tomorrow night. My wife has to work Sunday so I told her I would watch the "Duels at Daytona" with her tomorrow night. Probably head in the house right after work. Saturday is the only day of the week we both have off at the same time.
DAC