Turning a GT48DXLS into an actual Light Duty Garden Tractor.
I want to show the process as it unfolds as best I can, mistakes and all, to hopefully inspire someone in my position (with a buckled frame) that finds himself on the fence, questioning, if you can do this, or to just pay the $500 to $600 as quoted from the Dealer to have the same problem frame. It is my hope that the answer is "if that guy can do it....so can I".
This build will start with a $70 Harbor Freight canopy for shade. The Temperatures in Aug here in Florida are a Brutal 90F plus 80% t0 100% humidity with a thunderstorm 4 times a week to interrupt the personal sweat shower.
My tractor is in pieces on the back porch, lawn, and canopy.
Here is the new frame arrival,
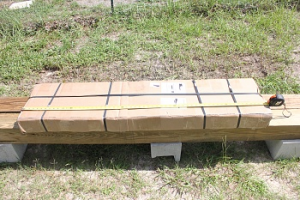
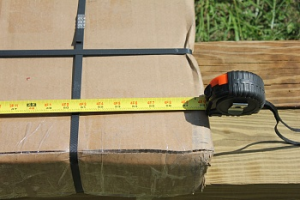
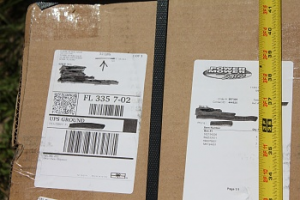
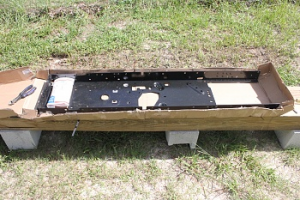
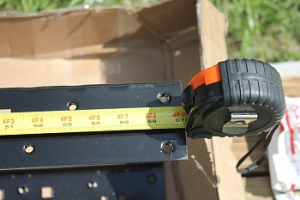
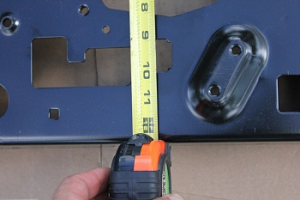
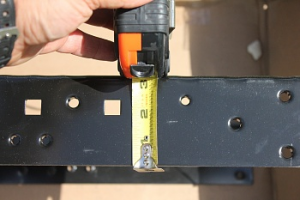
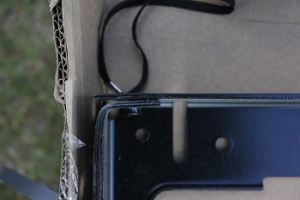
I want to show the process as it unfolds as best I can, mistakes and all, to hopefully inspire someone in my position (with a buckled frame) that finds himself on the fence, questioning, if you can do this, or to just pay the $500 to $600 as quoted from the Dealer to have the same problem frame. It is my hope that the answer is "if that guy can do it....so can I".
This build will start with a $70 Harbor Freight canopy for shade. The Temperatures in Aug here in Florida are a Brutal 90F plus 80% t0 100% humidity with a thunderstorm 4 times a week to interrupt the personal sweat shower.
My tractor is in pieces on the back porch, lawn, and canopy.
Here is the new frame arrival,
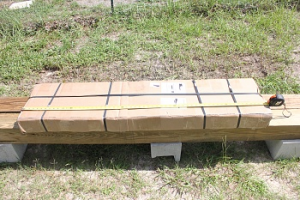
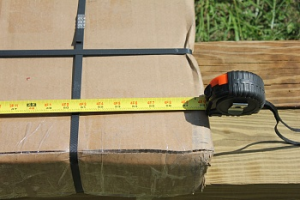
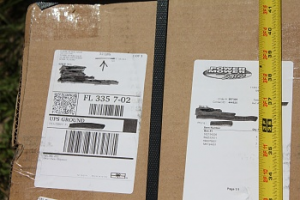
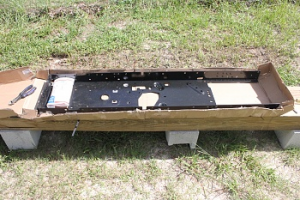
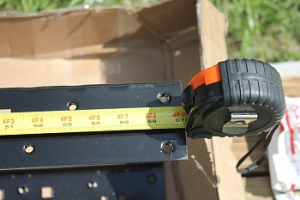
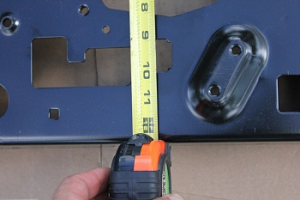
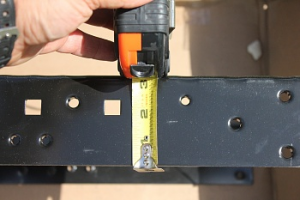
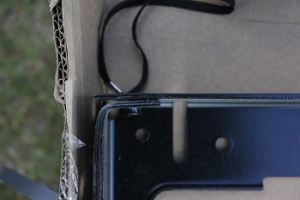