This is the rear part of the drive shaft and even though it doesn't have anything really sticking out that would easily grab anything, I still want to put a guard over it.
Here is what I formed up for it.
Here is how it looks mounted on the tractor.
Next is to make up the throttle and choke cables.
There is already a bracket on the side of the engine to hold the throttle cable housing but there isn't a bracket to hold the choke cable housing.
I took the strap bracket off the bottom of the carburetor that holds the air cleaner in place and welded a piece of steel to it to clamp the cable housing to.
Both cables are mounted in place and hooked up.
Here you can see how the choke cable housing is held in place on the side of the carburetor.
The other ends of the cables are mounted to the brackets and levers on the steering column.
The cables are operated by the two levers under the steering wheel.
The throttle is on the right and the choke is on the left.
Tomorrow I should be ready to start it up and take it for a test drive. ............................................................
I haven't gotten as much done on building this tractor as I had hoped to during the winter and now that the weather is getting warmer, I being pulled away from it to work on other things.
I'm getting out some of my other tractors and getting them ready to start taking them to the tractor shows.
The last few times that I have had this Ridemaster running, I have noticed that it is starting to get a rod knocking noise so I have pulled the engine out of it to work on it.
The cylinder looks really good but as long as I have the piston and rod out, I've gone ahead and ran the hone in a few strokes and I'll put new rings in it also.
At the same time, I'm also working on the FMC.
It had been stored up in the loft all winter and when I pulled it down I saw that one of the original rear tires had blown out the sidewall on one side.
I bought two new tires and mounted both of them up on the tractor.
From the factory, this had two 1/2 inch dia. pins sticking out on either side of the drive belt and someone had cut them off.
These two pins keep the belt from flying out the sides when the engine it lifted up into the neutral position.
For the most part, this wasn't a problem but I have noticed that when I would drive the tractor around a lot and the belt would heat up some, then the tractor had a tenancy to creep forward in neutral.
With the belt being able to fly out on the sides, it pulled the bottom of the belt up enough that it would start to grab on the pulley when it was hot.
So I have welded two pins back in place to each side of the pulley and it doesn't creep any more.
However, it does make a nasty sounding clacking noise a few times every time the engine is lifted up into neutral position.
I figure that is why someone cut the pins off in the first place.
The clacking noise is caused by the metal connecting strip, that holds the two ends of the belt together, hitting the steel pins a few times before it stops spinning.
I'm going to make up two round sleeves out of Delrin/Acetal bearing material to fit over the pins.
This material will be able to rotate on the pins and I'm hoping that the metal connecting strip won't make as much noise against the plastic like material and may also be a little quieter with that material being able to rotate with it.
It is a total experiment so I'll see how it goes.
If it doesn't work, then I see if I can get a continuous flat belt made up so it won't have the metal connector strip.
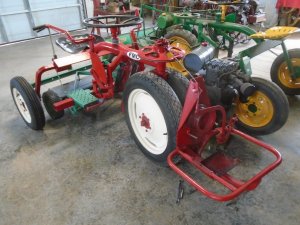