The swivel caster yokes that I'm going to use are the correct length but they are an inch to wide for the 6 inch long shoulder axle bolts that I have.
I need to make them narrower so the first thing to do was to cut them apart.
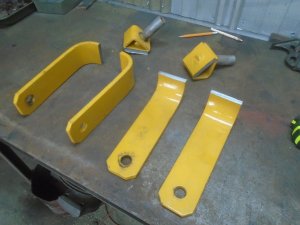
I made up a spacer tube the correct length and bolted the two arms together.
Then I welded them back onto the pivot mount.
I also welded a nut on one side that the shoulder bolt screws into and gets locked in place.
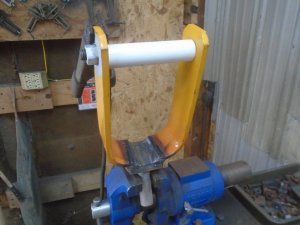
Both casters are done.

This gives you an idea of how they will look with the wheels mounted.
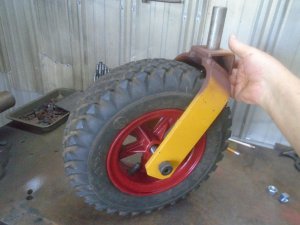
I'm still waiting on the bearings for these so I'll work on something else for awhile.
This tractor has band brakes on both sides and the operating lever is on the back side of the brake drum and pulls backward to operate the brakes.
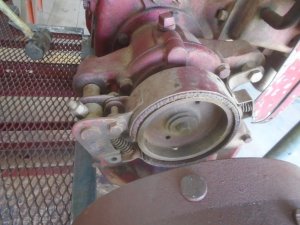
I don't want to have the operating linkage for the brakes in the area where my feet will be so I need to see if I can move the lever to the front side of the brake drum.
The mounting bolt for the brake assembly on the other side came off easily but this side doesn't want to move.
I ended up having to heat the housing up and it still took a long punch and a big hammer to get it out.
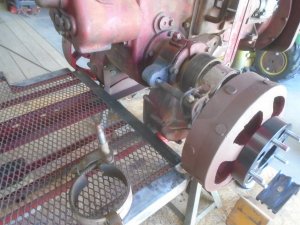
You can see here that the mounting hole in the back is 5/8 inch diameter and the mounting hole in the front is only 3/8 inch diameter.
I figure that I can take the brake assembly from the other side and move it over to this side but I have to drill the front mounting hole out to 5/8 inch diameter.
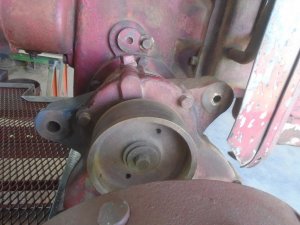
I'll start with this counter bore drill. It has a 3/8 inch pilot that will follow the 3/8 inch hole and keep the larger diameter cutting straight thru the housing.
This brings the front hole size out so it is only about .040 smaller then finish size.
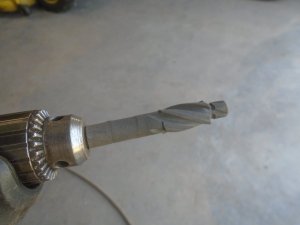
Then I'll use this 5/8 inch diameter reamer with the extension and a drill that has a level bubble on the top of it.
This makes it easier to ream the hole level and square with the housing.
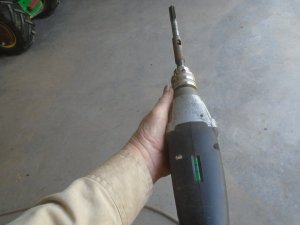
The brake assembly from the other side is now mounted on this side.
I drilled a 3/8 inch clearance hole thru a short 5/8 inch bolt and used it for the spacer for the rear hole.
The 3/8 inch bolt that fastened the front of the brake assembly in place had a 1/4 inch wide spacer between the bracket and the housing.
I cut the face of the 5/8 inch bolt head down to 1/4 inch thick so that bracket is still the correct distance out from the housing.
The operating lever for the brake is now in the front where there is plenty of room for the operating linkage.
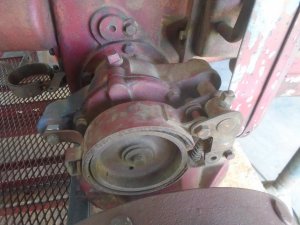
I need to make them narrower so the first thing to do was to cut them apart.
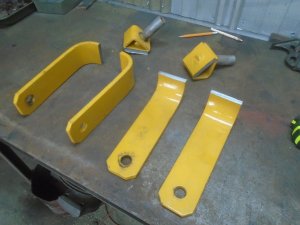
I made up a spacer tube the correct length and bolted the two arms together.
Then I welded them back onto the pivot mount.
I also welded a nut on one side that the shoulder bolt screws into and gets locked in place.
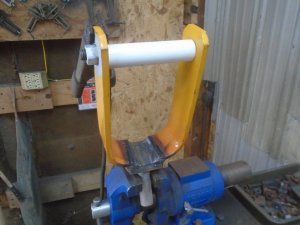
Both casters are done.

This gives you an idea of how they will look with the wheels mounted.
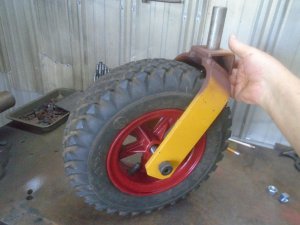
I'm still waiting on the bearings for these so I'll work on something else for awhile.
This tractor has band brakes on both sides and the operating lever is on the back side of the brake drum and pulls backward to operate the brakes.
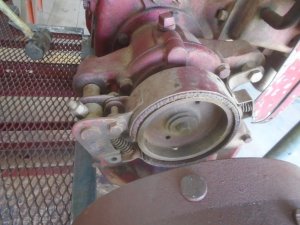
I don't want to have the operating linkage for the brakes in the area where my feet will be so I need to see if I can move the lever to the front side of the brake drum.
The mounting bolt for the brake assembly on the other side came off easily but this side doesn't want to move.
I ended up having to heat the housing up and it still took a long punch and a big hammer to get it out.
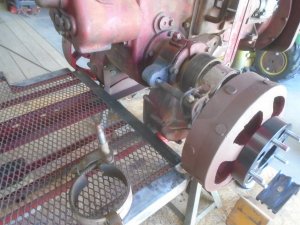
You can see here that the mounting hole in the back is 5/8 inch diameter and the mounting hole in the front is only 3/8 inch diameter.
I figure that I can take the brake assembly from the other side and move it over to this side but I have to drill the front mounting hole out to 5/8 inch diameter.
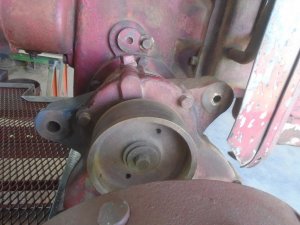
I'll start with this counter bore drill. It has a 3/8 inch pilot that will follow the 3/8 inch hole and keep the larger diameter cutting straight thru the housing.
This brings the front hole size out so it is only about .040 smaller then finish size.
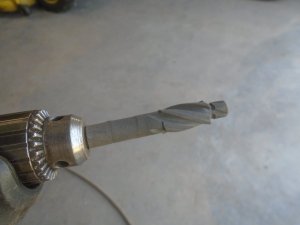
Then I'll use this 5/8 inch diameter reamer with the extension and a drill that has a level bubble on the top of it.
This makes it easier to ream the hole level and square with the housing.
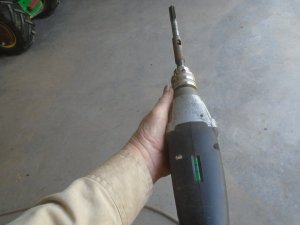
The brake assembly from the other side is now mounted on this side.
I drilled a 3/8 inch clearance hole thru a short 5/8 inch bolt and used it for the spacer for the rear hole.
The 3/8 inch bolt that fastened the front of the brake assembly in place had a 1/4 inch wide spacer between the bracket and the housing.
I cut the face of the 5/8 inch bolt head down to 1/4 inch thick so that bracket is still the correct distance out from the housing.
The operating lever for the brake is now in the front where there is plenty of room for the operating linkage.
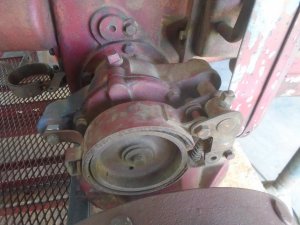