Was back on the CC1650 today. Motor is in and anchored down. Drive line lined up good. Can remover the engine by removing 2 nuts & 2 bolts and two out of the rive shaft. Today I did the wiring. Engine had key start so only had to remove all the old wiring and lengthen the key switch wiring to get it going. First two photos are of the engine to PTO adapter I had built. Round end goes against the flywheel, nut inside the tube.
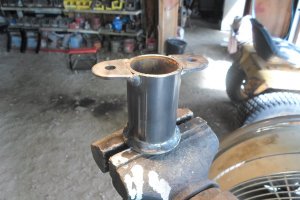
Welding in the back motor mounts from underneath. Not my favorite way to weld.
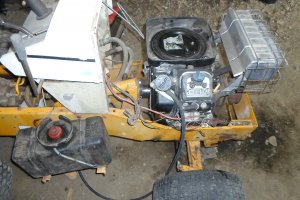
Old wiring removed and new inside the split tubing and tied up snug and out of the way. Throttle and choke cables replaced.
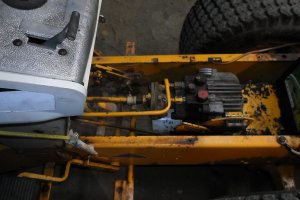
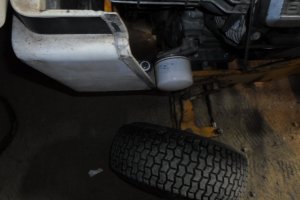
Put the nose on and then the hood. Nose cleared the oil filter by 1/4" so won't have to move it. Rag joints are nearly straight or square so very little difference between the end of the crank shaft and the input of the hydro. Fuel tank is a temp hook up just to get it running. Went for a drive down the road a ways and back. Hydro worked great, nice control and good slow speed control forward and reverse. Needs a few things yet like hydro fluid changed out and new filter, hydro fan installed, fuel tank mounted on the rear of the tractor and probably wouldn't hurt to throw some paint at it. Amp gauge and PTO switch need hooked up. All in all I feel the engine swap was a big success. Will get more photos after the fuel tank is mounted and it is up and running completely. Be glad to answer any questions you might have.
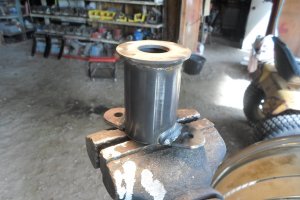
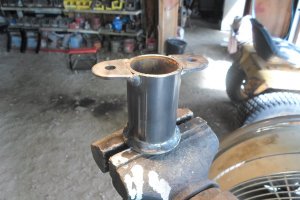
Welding in the back motor mounts from underneath. Not my favorite way to weld.
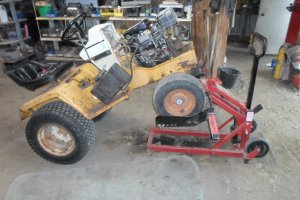
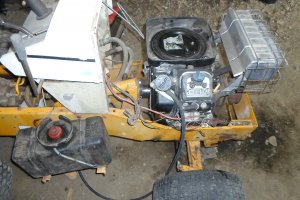
Old wiring removed and new inside the split tubing and tied up snug and out of the way. Throttle and choke cables replaced.
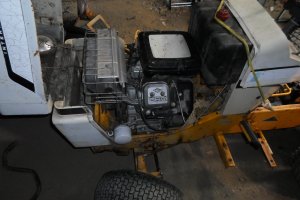
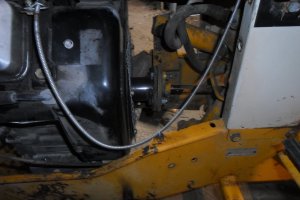
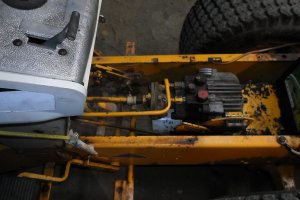
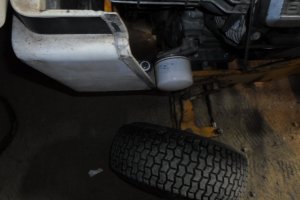
Put the nose on and then the hood. Nose cleared the oil filter by 1/4" so won't have to move it. Rag joints are nearly straight or square so very little difference between the end of the crank shaft and the input of the hydro. Fuel tank is a temp hook up just to get it running. Went for a drive down the road a ways and back. Hydro worked great, nice control and good slow speed control forward and reverse. Needs a few things yet like hydro fluid changed out and new filter, hydro fan installed, fuel tank mounted on the rear of the tractor and probably wouldn't hurt to throw some paint at it. Amp gauge and PTO switch need hooked up. All in all I feel the engine swap was a big success. Will get more photos after the fuel tank is mounted and it is up and running completely. Be glad to answer any questions you might have.
Attachments
Last edited: