I have been able to find the parts that I need on ebay so while I'm waiting for them to arrive, I decided to go ahead and work on the brakes.
I'm going to use this old implement lever arm for my brake handle.
First thing is to take it all apart.
This lever was set up so that the plunger was always pushed down into one of the notches and the trigger on the handle had to be squeezed to lift it up so the lever arm could be moved.
Because this is going to operate the brakes, I want to change that so that the plunger is kept up so the lever arm moves freely without having to squeeze the trigger.
The lever arm is cut off to shorten it and a notch is milled into the end where the handle bolts on.
I'm going to fasted the handle onto the other side of the arm and the front of the handle fits into that notch.
The front part of the handle where the pivot pin went thru is trimmed off.
The center hole on the trigger where the lifting wire was attached is brazed shut and a hole for a shoulder bolt is drilled thru it.
I bent up a U-shape bracket to hold the trigger and drilled and tapped it for the shoulder bolt.
That U-shape bracket is welded to the underside of the handle.
The trigger is mounted in place and the handle is bolted onto the lever arm.
This will be the normal position of the trigger with it holding the plunger up.
Squeezing the trigger will push the plunger down.
This way, the lever arm can be pulled back freely to operate the brakes without having to squeeze the trigger.
To operate the parking brake, the lever arm is pulled back and the trigger is squeezed to push the plunger down into a notch.
The pressure of the return springs on the brakes should be enough to keep the plunger engaged into a notch.
The brake lever assembly is just leaning up against the gas tank but it gives you an idea of how it will look when finished.
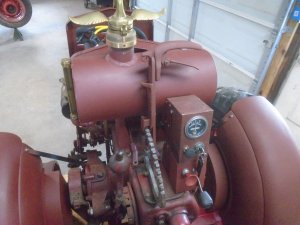