With the back of the fender bolted down, I also want to bolt it down where the inside side panel comes down to the axle housing.
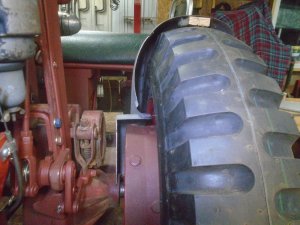
So I went hunting for something that would work and I found these two, 2-1/2 inch conduit clamps.
I found the first on with the short lag screw at Lowe's but they only had the one clamp.
I found the other one with the long threaded rod at the third place that I went to.
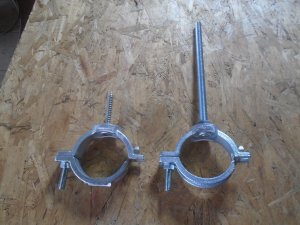
These clamps are made out of forged steel.
I cut one side off the round area and ground it down flat with that side.
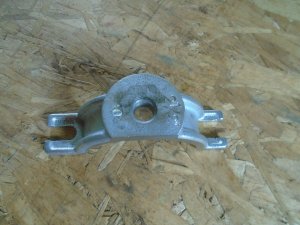
Then I cut the head off a pair of 1/2 inch bolts and tightened the threaded end in the vice to flatten the threads out a little.
Using a vice grip, I screwed them into the clamps so they are a very tight fit.
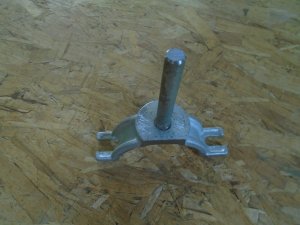
The clamps are just the right size to fasten around the axle housing.
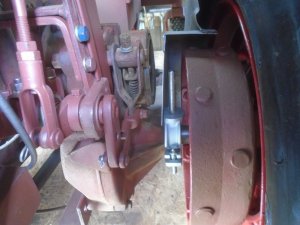
I bent up a bracket from 1/8x3/4 inch flat steel and drilled several holes in it.
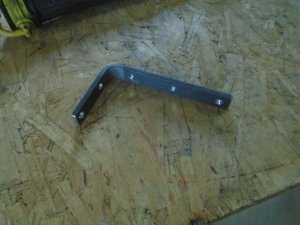
This is fit up inside the fender and held in place with vice-grips.
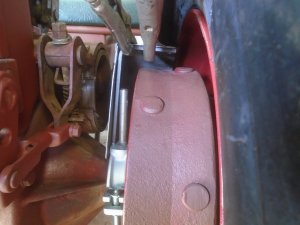
This bracket is then welded to the inside of the fender.
Instead of welding the second hole in the lower part of the bracket, I drilled this hole out thru the sheet metal of the fender and I'll explain why I did that later.
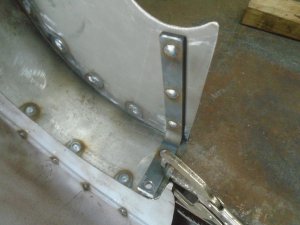
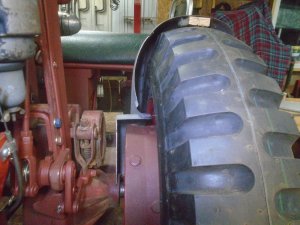
So I went hunting for something that would work and I found these two, 2-1/2 inch conduit clamps.
I found the first on with the short lag screw at Lowe's but they only had the one clamp.
I found the other one with the long threaded rod at the third place that I went to.
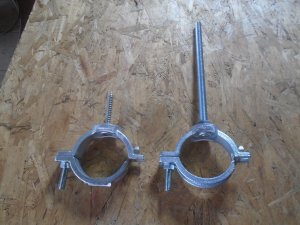
These clamps are made out of forged steel.
I cut one side off the round area and ground it down flat with that side.
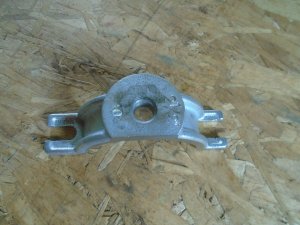
Then I cut the head off a pair of 1/2 inch bolts and tightened the threaded end in the vice to flatten the threads out a little.
Using a vice grip, I screwed them into the clamps so they are a very tight fit.
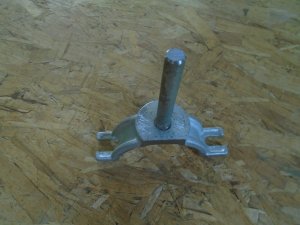
The clamps are just the right size to fasten around the axle housing.
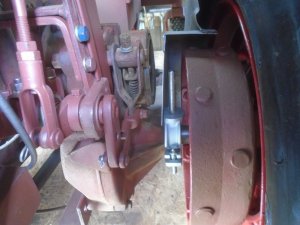
I bent up a bracket from 1/8x3/4 inch flat steel and drilled several holes in it.
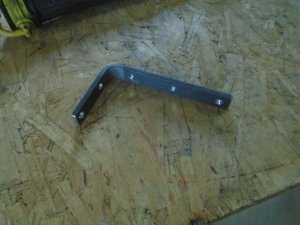
This is fit up inside the fender and held in place with vice-grips.
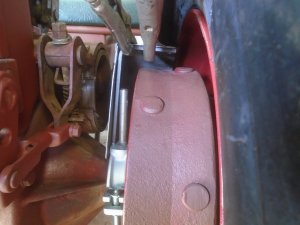
This bracket is then welded to the inside of the fender.
Instead of welding the second hole in the lower part of the bracket, I drilled this hole out thru the sheet metal of the fender and I'll explain why I did that later.
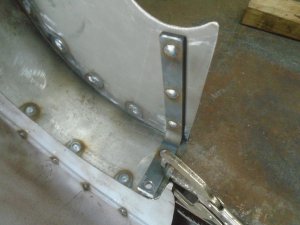